
Drop forging manufacturer

Home » Drop Forging products » Page 3

CFS Drop Forge is always keeping up with the highest quality standards.So there are a lot of advantages of making railway forging parts in our company as below:
- Integrated management system
- Moulding/forging/machining/heat treatment/welding are all available
- ISO certification
- Wide range of forged railway parts
- Conveninent delivery near Ningbo Port
In our company,many closed die forgings are used for automotive industry.Closed die forging will make automotive parts in a more stable working station. CFS Drop Forge provided forging solutions for automotive components.Our aim is to offer automotive companies high quality products.
As a TS16949 certified forging manufacturer,we can custom all the automotive forgings according to your specifications.Our services for both die/mould,forging and machining solutions will bring your better use or sell.Contact and send us your PFQ right now,we will reply you in the first time.
As a TS16949 certified forging manufacturer,we can custom all the automotive forgings according to your specifications.Our services for both die/mould,forging and machining solutions will bring your better use or sell.Contact and send us your PFQ right now,we will reply you in the first time.
Plastic forming and machining process of connecting rod are difficult,for the purpose of this forging production and machining process,which it is easy to appear the quality problem.The occurrence of these quality problems involve many factors. So for a long time,drop forging manufacturers are always continuously improving and discussing the material,forging process and mechanical processing manufacturing technology.Its purpose is to satisfy thetechnical performance and use requirements of products,and to be able to reduce costs,improve efficiency and increase economic benefits to the greatest extent at the same time.
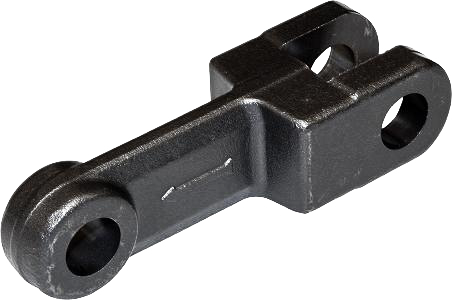
Our drop forged conveyor chains are manufactured in our chinese factory from high grade alloy steel,such as 42CrMo.Of course,we could make custom forgings according to your special requirements on other materials and heat treatments for high strength and wear resistance.Our drop forged conveyor chains have standard type,double type and triple link type.
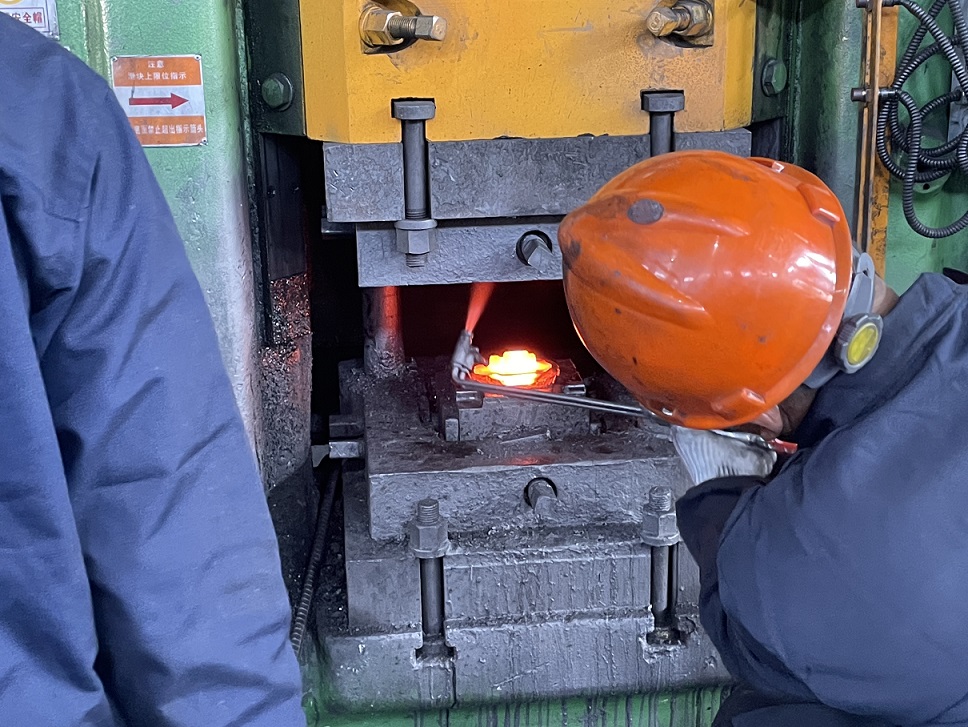
Custom forgings are the forgings made according to the drawings or sample from customers. Here the custom forgings we are talking about are using closed die forging method, not open die forging. Comparing with standard forgings,which have finished mold & dies developing, there is an extra cost for forging dies.
In our company, most drop forged products are all custom forgings excluding some standard high pressure pipe fittings. We are the manufacturer of custom forgings in China and could serve you custom forgings in high strength, close tolerances and low costs. Our forging buying guide will introduce buying procedure in detail.
In our closed die drop forging products,there is a top demand for wears parts.So called "wear parts" refer to metal components assembled to these machines which work in rather serious woking condition,such as mining,forest,agriculture,and so on.And these wear parts will directly work in soft soil,sandy soil or rock environment.So most of them are designed in drop forging process with better mechanical properties,although the cost might be higher than made in casting.In addition,to meet maximum wear resistance,wear parts manufacturers will use tungsten carbide tiled to forged wear parts body,so that they will have a longer woking life and save cost.
Production process of tungsten tiled wear parts
*Dies making for forged wear parts-according to the structure of wear parts,engineer will decide if they are fitted for closed die drop forging and decide the split line,then machine the forging dies with our advanced cnc machines.Normally the tooling cost is higher than that of casting for its precision dimensions and die material,normally between 2000-3000usd.
Production process of tungsten tiled wear parts
*Dies making for forged wear parts-according to the structure of wear parts,engineer will decide if they are fitted for closed die drop forging and decide the split line,then machine the forging dies with our advanced cnc machines.Normally the tooling cost is higher than that of casting for its precision dimensions and die material,normally between 2000-3000usd.
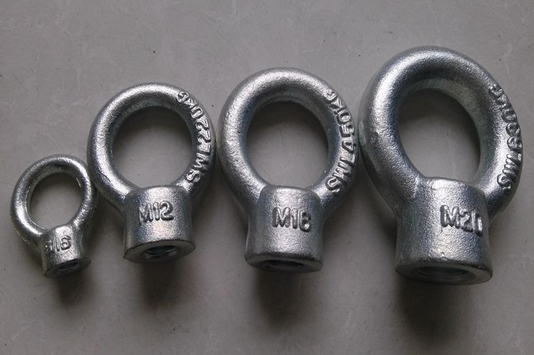
Of course,inspection of drop forged eye nuts is also very important.We should ensure that the products are regularly inspected and that the inspection should be done in accordance with the safety standards given in the country of use.This is required because the products in use may be affected by wear,misuse,overloading,etc.During using process,users should take in mind that Inspection should take place at least every six months and even more frequently.
Forged socket weld fittings are another kind of high pressure forged fittings we have made in our factory.A Socket Weld is a pipe attachment detail in which a pipe is inserted into a recessed area of a valve, fitting or flange. In contrast to buttweld fittings, socket weld fittings are mainly used for small pipe diameters (Small Bore Piping); generally for piping whose nominal diameter is NPS 2 or smaller.There are three pressure classes also:3000,6000,9000.Drop forging technology will help you to obtain good performance socket weld fittings,and you will no need to worry about any quality problem when using.As socket weld fittings can also be used in place of thread fittings,so there will exist much smaller leakage.Although they are used in many industries,but as socket weld fittings are not available for Ultrahigh Hydrostatic Pressure(UHP) in food industry,which may produce virtual leaks.Below is the dimension sheet of forged socket weld fittings we have in stock:
Threaded fittings are one of the oldest jointing methods used in piping systems.Similar to socket weld fittings,they are designed for small pipe diameters no more than NPS 2.Such threaded fittings are normally made in stainless steel or carbon steel.We can divide them into three pressure classes:2000,3000,and 6000.Forged threaded fittings are a kind of forged high pressure fittings widely used in low cost,noncritical applications like water&fire protection,industrial cooling water systems,ect.Currently,forged threaded fittings made in our company are 45° elbow,90° elbow,tee,cross,half couplings,full couplings,ect.Below are the detailed dimension sheet for forged threaded fittings we have developed:
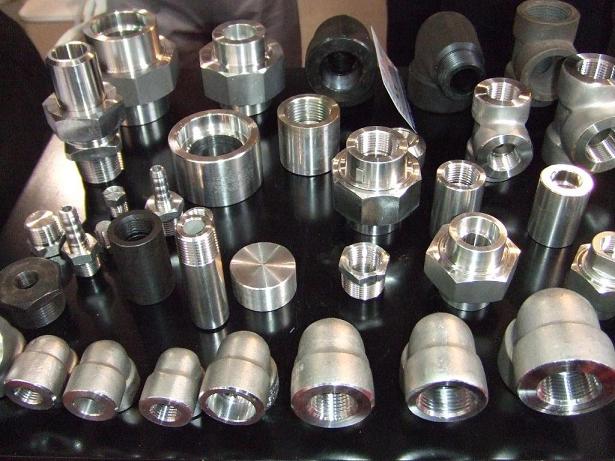
Materials:Due to the corrosion resistance and rustless of stainless steel,so it is commonly adopted for manufacturing forged fittings.Main material specifications are SS304 and SS316.Besides,there also exsits another carbon steel material(A105) used in the production of forged fittings.
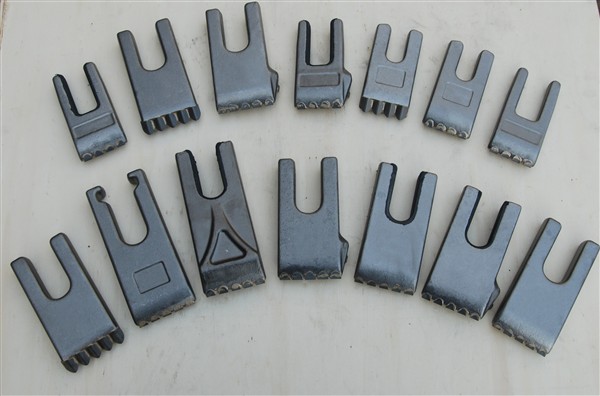
Benefits of drop forged auger teeth
- Drop forging can produce auger teeth that is strongerthan an equivalent cast part.As the metal bar is shapes during forging process,its internal grain deforms to follow the general shapes of auger teeth.
- Drop forged auger teeth respond more predictably to heat treatment and offer better stability.
- No internal defects will produce after forging
- Short lead time for large production runs
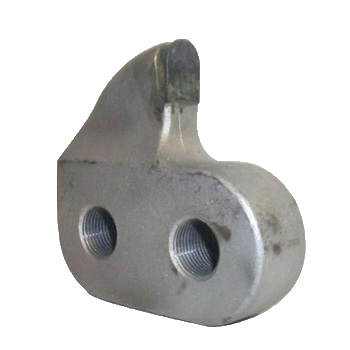
So the quality of stump grinder teeth will decide the using time.A stump grinder tooth is design by drop forging and then braze a small piece of tungsten carbide to enhance the strength so that it can work longer.After that such teeth will be fixed to the cutter wheel.Below is a picture showing how the stump grinder teeth are fixed to the wheel.