
Drop forging manufacturer

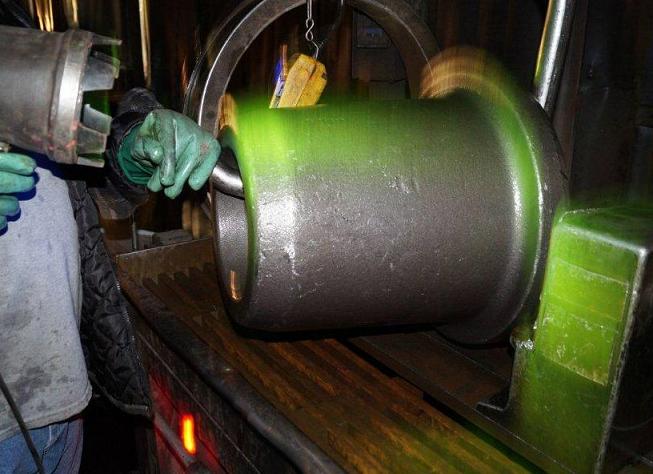
When it comes to drop forging, quality assurance is critical. Drop forging product testing is a step in the process that you simply cannot omit. There are a great many ways a drop forging can fail, and if those failures are allowed to slip through, it can be catastrophic to your finished products. There must be an effective quality control procedure in place to test for all the possible failure events a drop forged part can experience.
Product testing for quality assurance can be effective if you take the time to do it properly. It is extremely important because it helps you avoid sending defective parts to customers. Defective parts can cause customer production delays, excess costs, property damage and personal injury, and they can also tarnish your reputation. Quality assurance also helps you identify areas in your process you can streamline and improve to consistently produce a better product. We at CFS Forge believe strongly in the importance of good quality control.
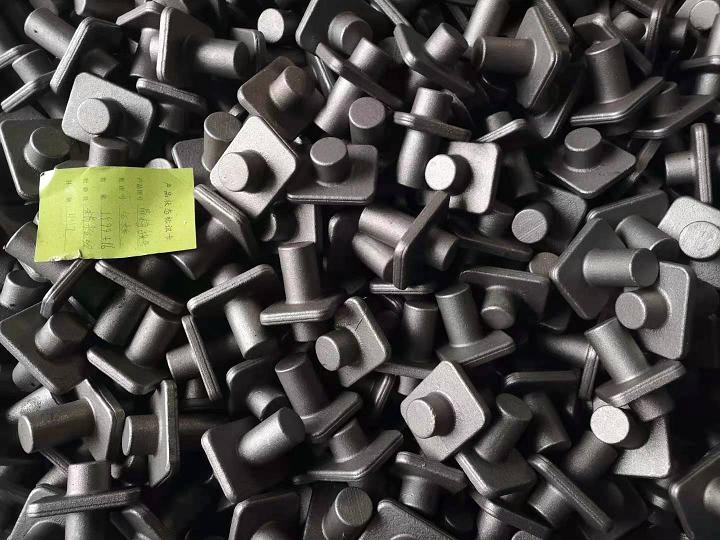
At CFS, we have over 150 employees on three shifts that are dedicated to making high quality drop forged parts that are within specifications and delivered on time. It is our goal to make continuous improvements on production, delivery, service and quality management.
Our Drop Forging Division has forging equipments in 2,500 tons, 1,600 tons, 1,200 tons, 1,000tons, 600 tons, 300 tons, etc. All these drop forging equipments enable us to drop forge products ranging from 0.2kg-30kgs. We have been supplying drop forged parts for any industry needed. We also have a complete Tool Room facility on the premises to build precise forging dies that insure process repeatability.
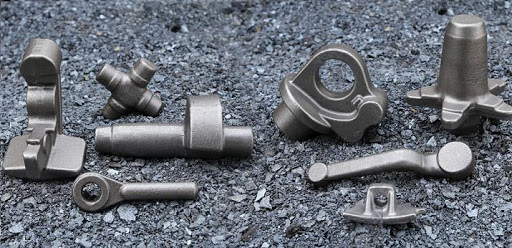
At the same time, steel is one of the easiest metals to forge, and steel drop forging for automotive parts offers numerous benefits. Steel drop forging combines a high level of production efficiency, superior quality and cost-effectiveness. Here’s our guide to using drop forging for automobile parts, including benefits, applications and the drop forging process in the industry.
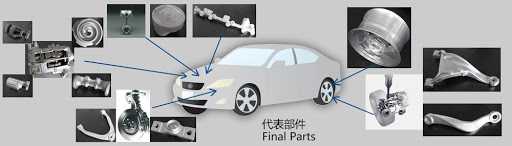
Most of the automotive parts are made from forged steel or forged aluminum. Steel has always ruled when it comes to automotive production. Forged steel is strong and when you forge it, it becomes stronger yet. However, forged steel is heavy and tends to corrode with road chemicals. There has been a push of late to reduce vehicle weight and reduce corrosion on equipment caused by road chemicals. One solution to these problems is the more extensive use of aluminum components.

Aluminum in its elemental form is a fairly soft and lightweight metal and is commonly alloyed with copper, magnesium, tin or zinc to increase its strength, durability, mass and workability. About 85% of aluminum parts are made by forging. Aluminum alloys are easily forgeable. Cast aluminum products are relatively low-cost due to its low melting point, however they do have lower tensile strength. Common forged aluminum alloys include: 6061, 6063, 6082, 7075, etc. Aluminum alloys are widely used in engineering applications and components where lightweight and resistance to corrosion is required. Forged aluminum parts are used in aerospace projects, automotive engine components, shipbuilding and other saltwater sensitive applications.
After understanding hot forging and cold forging methods, many people may still doubt the selection of forging methods of aluminum parts. Generally, cold forging is selected only when the shape of aluminum parts are simple and regular. Due to the expensive mold cost of cold forging, there is a high requirement on order quantity, normally above 30,000pcs. For irregular aluminum parts, hot forging is recommended, and most of the forged aluminum parts will be further machined to get finished parts. Both hot forged and cold forged aluminum parts could be heat treated and anodized when necessary. CFS Forge is professional on forging all types of aluminum parts. If you have any inquiry on forged aluminum parts, pls contact us timely!
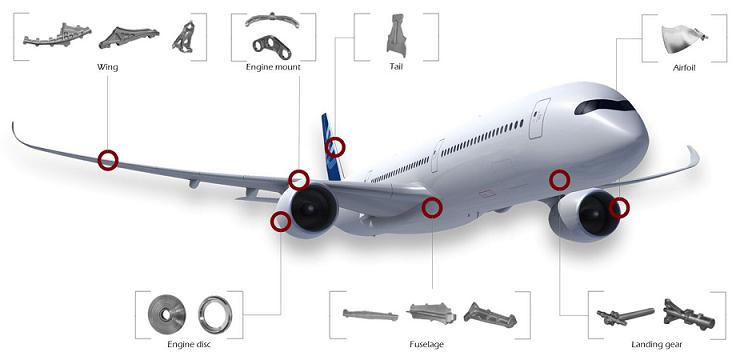
First, aerospace forgings generally choose materials with high specific strength and specific stiffness, and often adopt new materials, constantly putting forward new and higher requirements for drop forging production technology.The application of materials depends on advanced forging technology and also promotes the development of advanced forging technology and equipment. Due to high strength and low plasticity, large forging equipments are generally needed, which have low deformation speed, good deformation temperature control.
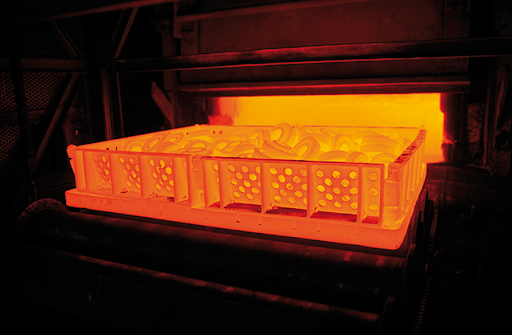
In drop forging process, stainless steel is one of the common forged materials. After forging, heat treatment is generally operated to release the stress and ease further machining job. CFS Forge, an experienced drop forging company in China, can customize stainless steel forgings with various heat treatment processes.
Austenitic Stainless Steel Forgings
Solid solution treatment: heating stainlesss steel forgings to solid melting temperature (1050 ~ 1100℃), making all carbide and cold processed Martensite melt into austenite, then fast cooling. This type of heat treatment can obtain the most soft and plastic effect.
Austenitic Stainless Steel Forgings
Solid solution treatment: heating stainlesss steel forgings to solid melting temperature (1050 ~ 1100℃), making all carbide and cold processed Martensite melt into austenite, then fast cooling. This type of heat treatment can obtain the most soft and plastic effect.
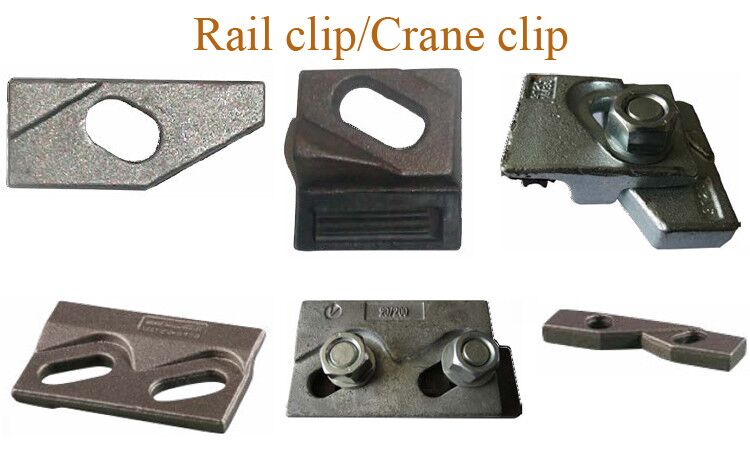
A rail fastening system is the way to fix rails to railroad ties or sleepers. It is required to be reliable in connection, simple in structure, easy to disassemble, and also needed the properties of elasticity, vibration damping and insulation. Different types of sleepers have different rail fastening system for use with ballast and ballastless tracks. Railway fastening system for wood sleeper includes dog spikes and tie plate. Rail fastening system for concrete sleeper is generally rail clip type and balde-type. The most commonly used types are elastic clip fasteners with SKL, clip, e-clip, Nabla or KPO clamp, etc. Generally, rail fastening system is consist of screw spikes, rail bolts and nuts, flat washers, rail clip, gauge block, and rail rubber pads.
In railway fastening system, rail clip is one of the components which ensure that rails will be fixed to ground. Rail clips undertake rail movements synchronously thanks to synthetic elastomer vulcanized to clip permanently in the portion to be contacted with rail.
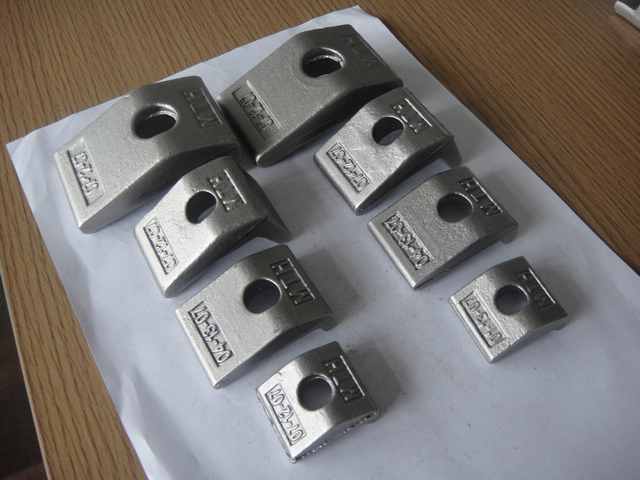
Drop Forging refines the grain structure of rail clamps and develops the optimum grain flow, which imparts desirable directional properties such as tensile strength, ductility, impact toughness, fracture toughness and fatigue strength. In addition, drop forged rail clamps are free from internal voids and porosity. The whole forging process achieves very consistent material uniformity, which results in uniform mechanical properties and a uniform, predictable response to heat treatment.
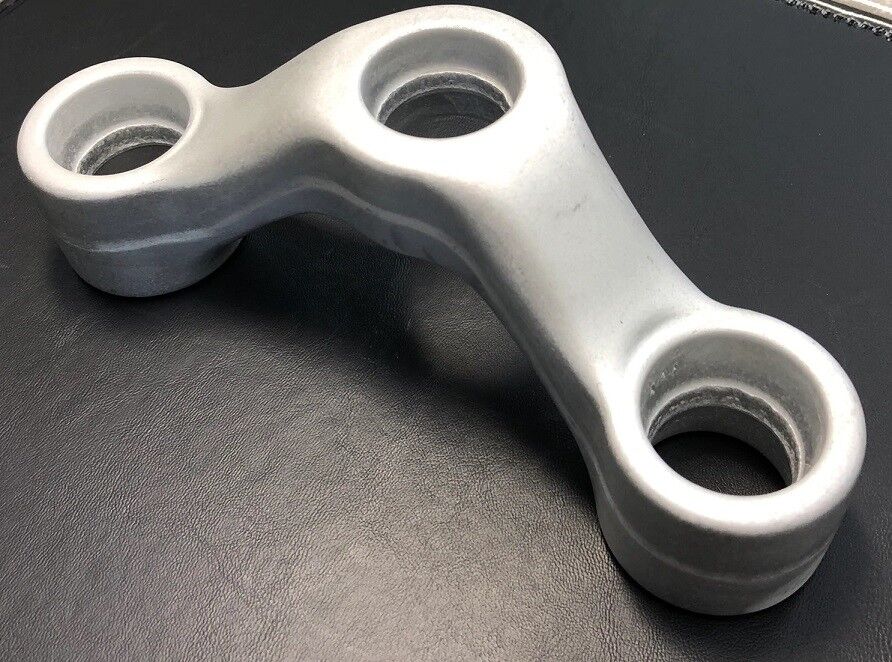
Aluminum forging is the common type that is easily accessible for its light weight and good strength. They are available in all shapes and sizes. Aluminium forging is not only easy but also quicker to establish. The net output is also light in weight and, hence, easy to carry around or transport compared to its rival counterparts. The strength of the produce through aluminium forging can also be controlled as per the maker's desire. They can be made subtle or strong depending on the need or end usage. Forged aluminum components have a direct strength to weight ratio so the manufacturer knows how much forging needs to be involved in order to gain the desired output. The best part about them is that they last for very long as they are rust-free and have high resistance against environmental changes, chemicals and toxic materials.
A lot of properties possessed by forged aluminum components make them favorite amongst aluminum forging companies. Compared to other metals, aluminium conducts heat effortlessly which other metals would not be able to do at the same given price. This makes it economic for users to opine for it. When it comes to power consumption, again, forged aluminum components are given a higher preference compared to other metals since they conduct electricity very well and are more efficient.
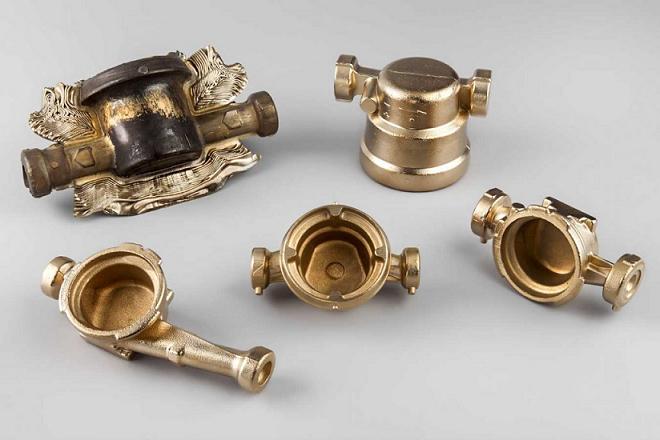
A water meter is a device that measures the volume of water delivered to a property. Some water meters measure water in gallons while others measure in cubic feet. The brass water meter fittings are commonly used for connecting to a water meter installation, but can also be used to connect network elements or other accessories provided with threaded connection.
Normally such water meter fittings are designed and produced by brass hot forging and machining. According to the drawings or samples from our customer, CFS Forge can forge and machine water meter brass fittings in different sizes.The brass hot forging process offers many advantages in comparison with the traditional casting techniques. Any inquiry on brass forged and machined water meter fittings, pls feel free to contact us!
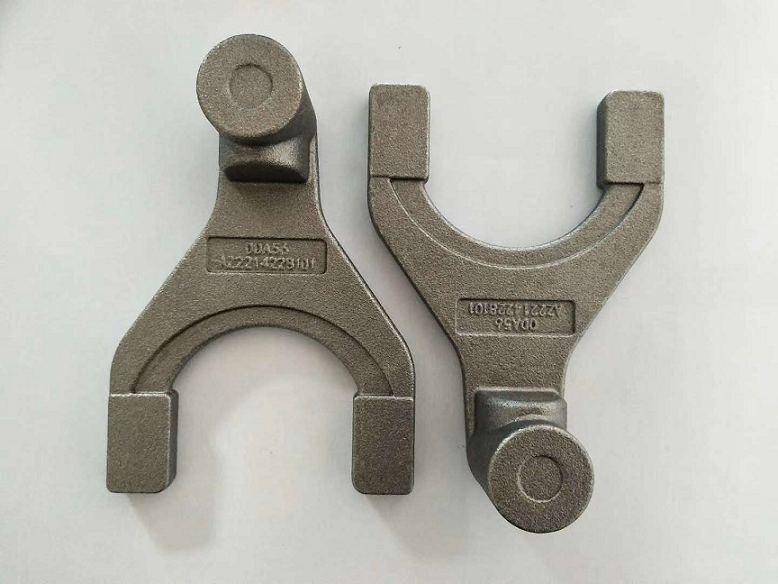
There are so many ways to forge metals, and each of these methods have their own peculiarities; One very well named metal forging method is called drop forging. Drop forgings are performed when a person inserts a sheet of metal into the press. This sheet is placed over top of a die, the shape of which is based on whatever has been ordered or what the company has decided to produce that day. Once the metal is securely in the machine, a hammer comes down, or rather drops down, and forces the sheet of metal to take the shape of the die. The hammer itself is called a power or drop hammer – hence the name drop forging – and they usually only need to be dropped on the metal once to get it to the right specifications.