
Drop forging manufacturer

For the production of motorcycle parts, hot forging is one of the most commonly used methods. The process involves heating a metal to a temperature where it becomes malleable and then applying pressure to shape it into the desired form. One of the key components in a motorcycle's suspension system is the triple clamp, which is responsible for holding the front forks in place. In this article, we will explore the manufacturing process of an aluminum hot forged triple clamp, the material grade used, the advantages over other methods, and a top Chinese supplier of this product, CFS Forge.
Aluminum hot forged motorcycle triple clamps are essential components of the motorcycle steering system, ensuring stability and safety during operation. CFS Forge's aluminum hot forging process offers significant advantages over traditional casting and machining methods, resulting in stronger, more durable components.
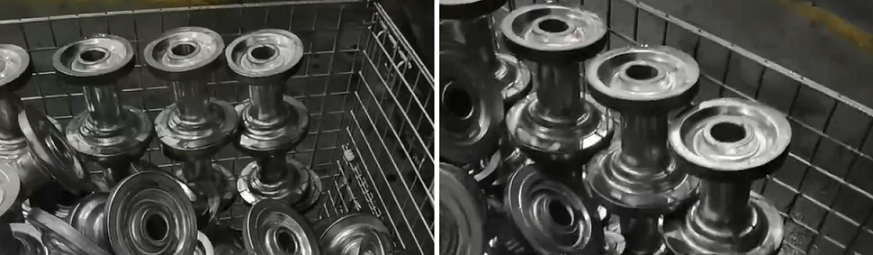
Motorcycles are the epitome of freedom on the open road, but they require specialized parts to keep them running at peak performance. One such component is the wheel hub, which connects the wheel to the axle and provides support for the motorcycle's weight.
A forged aluminum motorcycle wheel hub is a popular choice for riders looking for high strength and durability. It is made by taking a solid piece of aluminum and heating it until it becomes malleable. The aluminum is then shaped using a forging press, which applies intense pressure to the material, causing it to take on the desired shape. The result is a high-strength, lightweight wheel hub that is ideal for use in motorcycle applications.
Drop forged C-clamps are a type of clamp that is made by heating a metal bar and then shaping it into a C shape. The metal is then hammered into shape, creating a strong and durable clamp. The term "drop forged" refers to the process of forming the clamp by dropping the metal into a mold, which is then struck with a hammer to shape the metal.
These clamps are typically made from high-quality steel, which makes them extremely strong and durable. They are designed to hold materials firmly in place, even under extreme pressure. They come in a variety of sizes and shapes, making them suitable for a wide range of applications.
When it comes to towing heavy loads, it's essential to have the right equipment to ensure safety and stability on the road. One of the key components of any towing setup is the hitch ball mount, which connects the trailer to the towing vehicle. While there are many different types of hitch ball mounts available on the market, one option that stands out is a forged aluminum hitch ball mount. In this article, we'll explore the benefits of using a forged aluminum hitch ball mount for towing.
First, let's define what a forged aluminum hitch ball mount is. Forging is a manufacturing process that involves shaping metal using heat and pressure to create a strong and durable product. When it comes to hitch ball mounts, forged aluminum is an ideal material because it is lightweight, strong, and corrosion-resistant. By using a forged aluminum hitch ball mount, you can be sure that you have a high-quality product that will stand up to the demands of towing.
A forged aluminum hitch ball mount is a metal bar that attaches to the hitch receiver of your vehicle. It features a ball on the end that connects to the coupler of the trailer you're towing. The ball mount is available in various sizes and configurations to accommodate different types of hitches and trailers.
Forged aluminum hitch ball mounts are made using a process known as forging. Forging involves heating metal to a high temperature and then shaping it using a hammer or press. This process creates a denser, more durable metal than other manufacturing methods, making forged aluminum hitch ball mounts exceptionally strong and long-lasting.
Aluminum forging is a widely used manufacturing process that provides numerous benefits, including improved strength, durability, and flexibility. The choice between 6061 and 6082 aluminum forging depends on the specific application requirements. 6061 is a versatile and easy-to-work-with alloy that is well-suited for applications where machinability and elongation are important. On the other hand, 6082 is a higher strength alloy with better corrosion resistance and hardness, making it a better choice for applications where strength and durability are crucial.
By understanding the differences between 6061 and 6082 aluminum alloys, you can make an informed decision and select the right material for your project.However, it's important to note that there are other aluminum alloys available for forging, and each one has its own unique properties and benefits.
If you're unsure which aluminum alloy is right for your application, it's important to work with an experienced aluminum forging company like CFS Forge. We can help you select the right material based on your specific requirements and provide expert guidance throughout the entire manufacturing process.
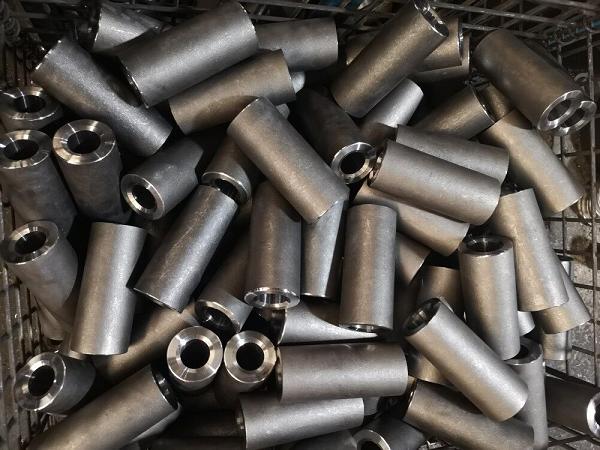
Over the years, the forging technique in CFS Company has been always updated. Our steel forging, aluminum forging and copper forging services gave rise to various applications in construction, agriculture, automotive, machinery, and so much more. As a leading forging company in China, it’s our duty to ensure the products we produce are of the highest quality at a price our customers can afford. Our customers cover many different industries and we have the experience and track record to provide the level of detail each industry requires.
There is a stigma that forging parts produced in China are low-quality and made from sub-par materials. While some dubious, fly-by-night companies may cut corners, here at CFS Forge, we do not. We use only high-quality materials to produce all the forgings for our customers. In fact, all the forgings produced in our facilities are 100% quality guaranteed. As long as the design is suitable for forging process, we have the confidence to ensure high quality products by working closely with our customers.
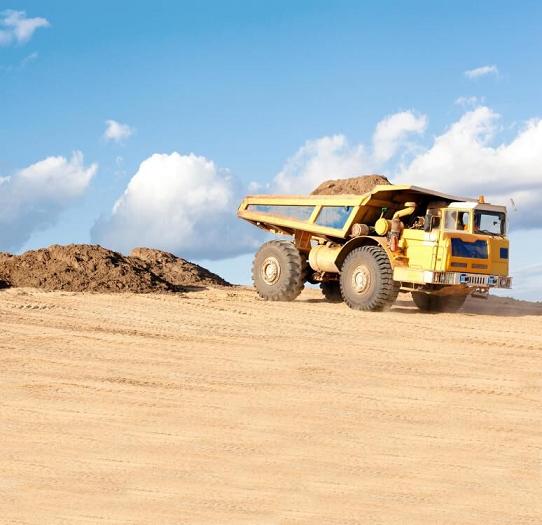
At CFS Forge, we are a qualified drop forging company in China with over 30 years' forging experience. According to our client's requirements, we can produce and export net, near-net, and finished drop forged products for a wide range of industries, including off-highway. By working closely with our customers in the off-highway industry, we always produce strong and durable drop forgings that meet and even beyond the industry’s standards.
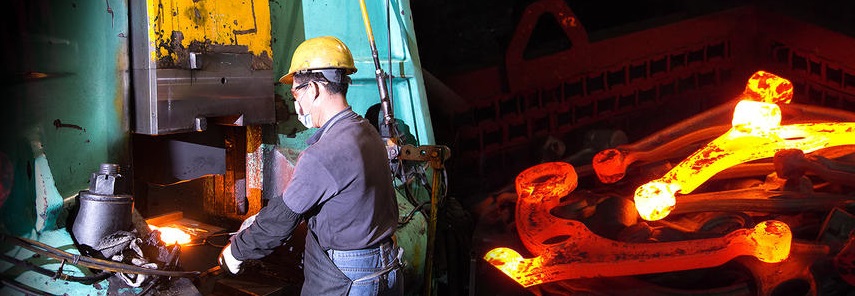
When it comes to drop forging metals, anyone working in the metals industry knows that use of aluminum is growing, that is because forged aluminum is strong while maintaining its light weight. Even if the price of aluminum is fluctuating, the demand of aluminum forging is still increasing compared to steel forging and copper forging.
Due to the fast growth in transportation and construction industries, aluminum’s upward trend is expected to continue over the next several years. According to one market report, the worldwide market for aluminum alloys is expected to grow at a compound annual growth rate (CAGR) of 4.8 percent through 2020, with market revenue rising in the U.S. from $91.2 billion in 2013 to $126.5 billon in 2020. Another report states that in the global automotive industry alone, aluminum use is expected to grow at a CAGR of 7.4 percent over 2015-2020.
CFS Forge, as a key drop forging supplier to automotive and other aluminum forging-consuming industries, the skills of our workers and forging equipments are always improved. The unique properties of aluminum forging require us to be equipped with the right forging tools and techniques.
Aluminum forging has the advantage of the addition of deformation energy to further refine and improve the metallurgy of the shape being created. Through mechanical and thermomechanical deformation energy applied, originally cast ingots of aluminum are shaped and reshaped, changing the internal microstructure. Any inclusions or alloy concentrations are dispersed, and any voids are crushed and eliminated. Forging energy drives the recrystallization of the microstructure, creating enhanced durability and toughness. Forged aluminum is not usually able to produce shapes as complex as cast aluminum. This often requires additional machining operations which adds to the cost of using aluminum forging. The improved properties of forged aluminum product outweigh cost issues, however, when safety, reliability and the cost of component failure are the greatest challenges.
In summary, forged aluminum is strong, which is the ideal choice when aluminum components must exhibit maximum strength and performance in service, where weight is minimized.
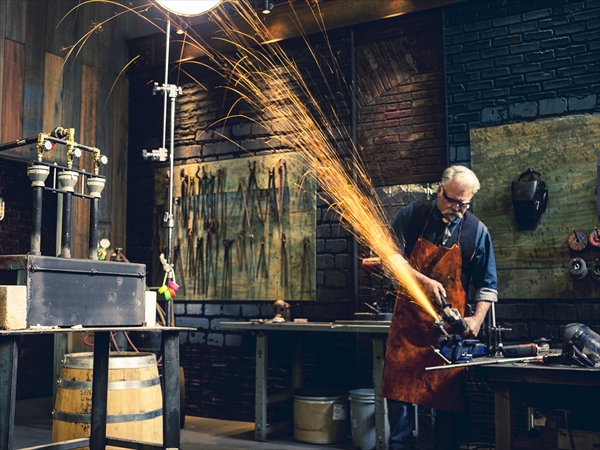
Drop forging is one of the oldest metal-forming processes that is still used as of this date. Did you know drop forging process is already 6,000 years old! Fascinating, right?
The art of the drop forging techniques dates to at least 4000 BC and earlier. The hot forging of metals all began in the land of Mesopotamia, between the Tigris and the Euphrates.
Bronze and iron went through the drop forging process by the early man to produce hand tools, weapons of war, and jewelry. However, the very first recorded metal, forged by fire and employed by humans was Gold. To shape the metal, rock was used as a drop forging hammer. Until the end of the 19th century, the precision drop forging of iron and steel continued.
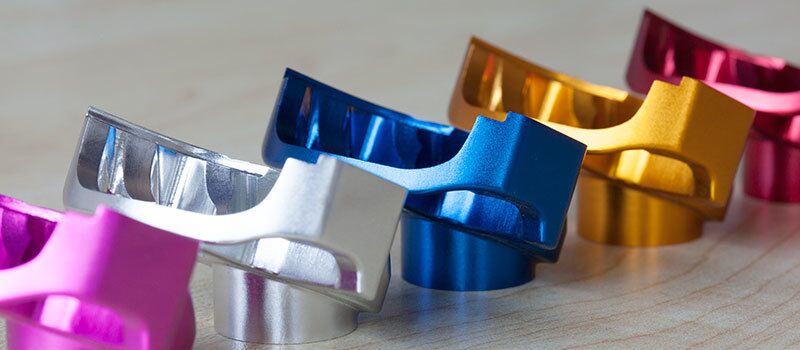
In order to properly anodize forged or machined aluminum parts, the surface must first be cleaned and rinsed before getting placed into a bath of an electrolytic solution, primarily either sulfuric or chromic acid. This provides a electrically conductive coating that contains a number of positive and negative ions.
So how does this process really work? Well, once the anodizing process is underway, a positive electric charge is sent through the aluminum, while a negative charge is applied to plates in the electrolyte. Basically, the electric current forces the positive ions to attract to the negatively charged plates while the negative ions are attracted to the forged or machined aluminum part, which the positive anode.
From here, the electrochemical reaction forces pores to open up on the surface of the aluminum so that the positive ions can escape. In a uniformly geometric pattern, these pores dig down into the substrate of the part. The combination of the aluminum surface and negatively charged ions create a barrier layer, which is known in the anodizing aluminum process as the surface layer the makes parts resistant to corrosion.