
Drop forging manufacturer

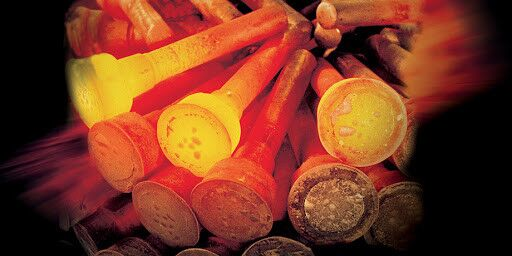
Drop Forging also grains the metal which makes it last longer and remain continuous for a lifetime. In most of the industries, a specific shape of metal is required for a specific application. Getting this shape is not possible without drop forging. So drop forging is also advantageous in giving metals different shapes and converting them into different final products. These well-shaped metals are then used for a wide range of applications.
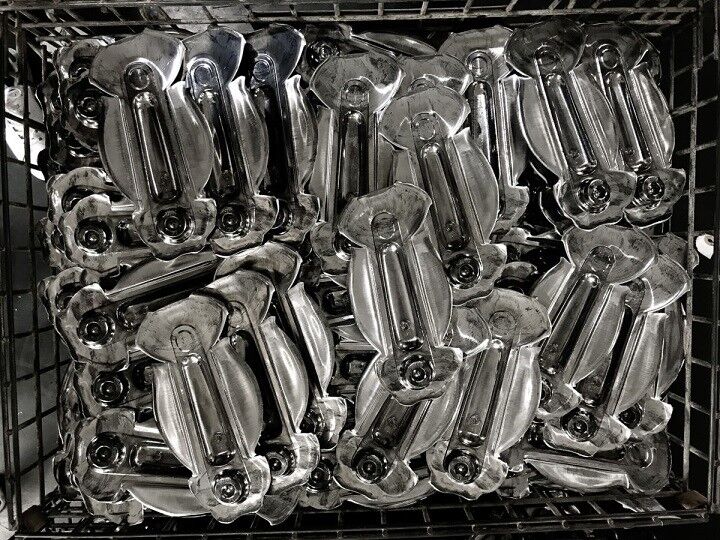
Althought the forging process of aluminum and brass alloys are almost the same, there still exsits great differences between forged aluminum and forged brass. As the professional drop forging company, we can produce both forged aluminum parts and forged brass parts.
Due to the high quality of drop forgings, the quality control system and process discipline in the drop forging factory are relatively strict, and the quality control means are also relatively complete. The quality control is mainly reflected in three links. Firstly, the raw materials are reinspected to check whether their chemical composition and physical properties meet the technical requirements. Secondly, strictly supervise the production process to meet the quality requirements. Thirdly, check and accept the finished drop forging according to the quality standard.
The production process discipline of drop forgings must be strict, especially for forged steel aumotive parts . Once the process rules are determined, they must be strictly implemented and cannot be modified without approval. This is another aspect of quality supervision in the workshop. In view of the above requirements, there are many inspectors in the drop forging plant. Depending on the composition and nature of the workshop, inspectors shall be approximately 5% of the total workshop workforce.
The production process discipline of drop forgings must be strict, especially for forged steel aumotive parts . Once the process rules are determined, they must be strictly implemented and cannot be modified without approval. This is another aspect of quality supervision in the workshop. In view of the above requirements, there are many inspectors in the drop forging plant. Depending on the composition and nature of the workshop, inspectors shall be approximately 5% of the total workshop workforce.
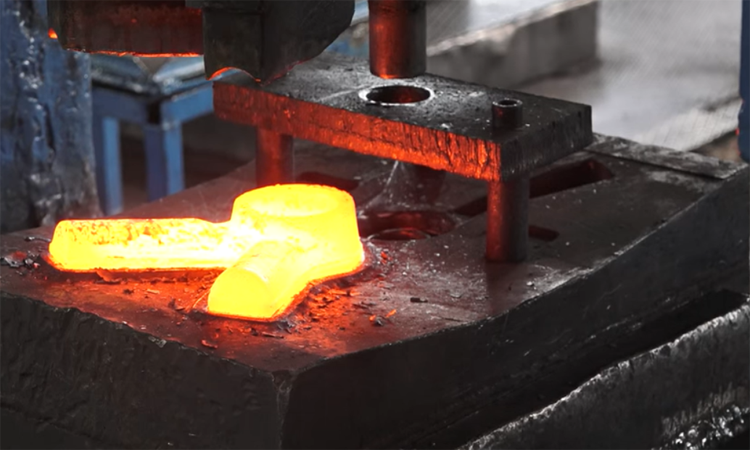
Forged steel is nothing but the forging process of giving steel billets to different shapes as per the drawings of the final products. There are several processes for forming a component by forging. The most commonly used metal for automotive components is steel. For all such products, steel billets are cut into the required lengths and weight, heated up in an intermediate frequency furnace, then forged into the desired shape with the workforce of dies on a forging press. The part is then forwarded to another press machine to remove the trimmings under trimming dies, finally, sent on to the machining line for finishing into the final product.
Forged steel can creat automotive parts stronger than equivalent types that are cast or machined. Steel forging is commonly used in automotive applications due to its strength, availability, and high quality. Forging in steel offers unsurpassed resilience for manufacturing automotive parts that simply do not fail. There are several benefits of automotive parts in forged steel:
- By drop forging process, it can creat forged steel automotive parts with close tolerances, and less or no machining is required, which can help to save cost.
- Compared with casting or machining, automotive parts in forged steel are free from defects such as gas voids, pockets, or cooling defects which can lead to load failure.
- Under the high pressure of forging dies, the internal crystal structure is improved, which will grearly improve the strength of automotive parts, thus to make the serving life longer.
- Normally, a pair of forging dies can forge out 20,000pcs~30,000pcs automotive parts, this capacity can support large volume order. What's more, the dies cost is charged only once in CFS Forge, will not be charged again for furture orders.
Type 6061 aluminum is of the 6xxx aluminum alloys, in which magnesium and silicon are the primary alloying elements. The second digit indicates the degree of impurity control for the base aluminum. When this second digit is a “0”, it indicates that the bulk of the alloy is commercial aluminum containing its existing impurity levels, and no special care is needed to tighten controls. The third and fourth digits are simply designators for individual alloys (note that this is not the case with 1xxx aluminum alloys). The nominal composition of type 6061 aluminum is 97.9% Al, 0.6% Si, 1.0%Mg, 0.2%Cr, and 0.28% Cu. The density of 6061 aluminum alloy is 2.7 g/cm3 (0.0975 lb/in3). 6061 aluminum alloy is heat treatable, easily forfged and machined, and is good at resisting corrosion.
6061 Aluminum alloy are generally forged by drop forging manufacturer on hydraulic presses because of their high strain-rate sensitivity. The use of hammers and mechanical presses are the exception rather than the rule. Ram speeds are generally on the slow side, with 1 inch/second or less being typical. Hot dies, including isothermal, are common. In most cases, the tooling temperature is within 250°F of the workpiece temperature. For net-shape/precision forgings, isothermal tooling and low strain rates are the norm.
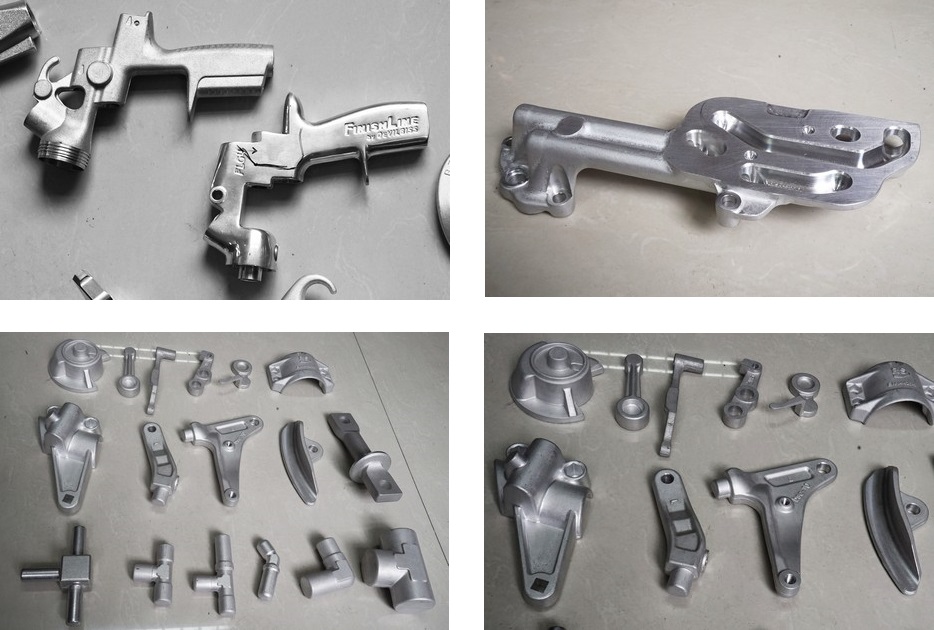
Aluminum alloys, for its low density, can always be used to make metal parts with light weight. Generally, aluminum alloys are divided into casting alloys and forged alloys, and are best suited for different applications. Forged aluminum alloys, such as the 6061 alloy, are widely used in drop forging process to creat specified shapes and dimensions. During the process, the billet is heated through an induction furnace and forged using a closed die drop forging process.
Among all the forged aluminum alloys, 6061 is one of the most commonly used aluminum grades in the world. Whether hot or cold forging, 6061 is the choice for a wide range of applications, including automotive, motorcycle, aerospace, and so on. So, what makes 6061 so versatile? Like with any grade, it starts with the makeup of the metal. Its major alloying elements are magnesium (1.0%) and silicon (0.6%). This makes it highly resistant to corrosion, stress, and cracking. This also means the grade features good formability and weldability. Pls note 6061 is not an alloy that is traditionally cast due to its low silicon content affecting the fluidity in casting.
Drop forging is the metal forming process that shaping metal and increasing its strength. In drop forging, an upper die is forced against a heated workpiece placed on a stationary lower die, and the billets will fastly filled the cavity of dies under the workforce of high pressure. Then, the billets become a forged blank that has the desired shape as designed. Finally, remove the flash under trimming dies to achieve a net shape drop forged part.
CFS Company is the largest drop forging company in China. We have an extensive amount of drop forging experiences for copper and brass alloys. Here at CFS Forge, we put the customer first and our mission is to exceed your expectations. We offer uncompromising drop forgings and our teams go out of their way to ensure all of your needs are met. If you have any special requests please let us know today! We are ready to answer all of your questions!
CFS Company is the largest drop forging company in China. We have an extensive amount of drop forging experiences for copper and brass alloys. Here at CFS Forge, we put the customer first and our mission is to exceed your expectations. We offer uncompromising drop forgings and our teams go out of their way to ensure all of your needs are met. If you have any special requests please let us know today! We are ready to answer all of your questions!
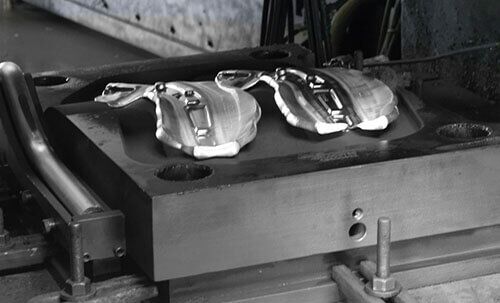
First of all, you should understand the charteristics of aluminum alloys. Aluminum is a metal similar to steel, brass, copper, zinc, lead or titanium. It can be melted, cast, forged and machined in a similar way to these metals and conducts electric currents. Aluminum is a very light metal with a specific weight of 2.7 g/cm3, about a third of that of steel. This cuts the costs of manufacturing with aluminum forgings. Again, its use in vehicles reduces dead-weight and energy consumption while increasing load capacity. This also reduces noise and improves comfort levels.
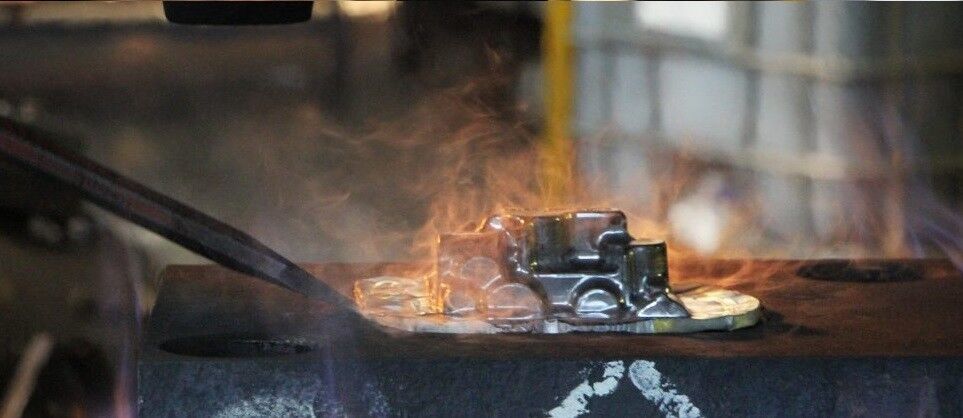
On the internet, you will find many numbers of companies that can provide drop forging service. For your RFQs, you may contact several potential drop forging suppliers for comparision. Besides comparing prices from these different drop forging companies, it is also a process for you to understand and choose a best drop forging company.
Drop Forging is a manufacturing process that squeezes heated round bars between upper and lower dies until filling the cavity of dies completely. Parts produced by this method are of precise sizes, little or no machining allowance and complex structure with high productivity. Drop forging process has high production efficiency and low labor intensity, which will be able to make complex components with higher strength than casting process. This production method is suitable for mass production. However, the cost of forging dies is relatively high, not suitable for single piece or small batch production.
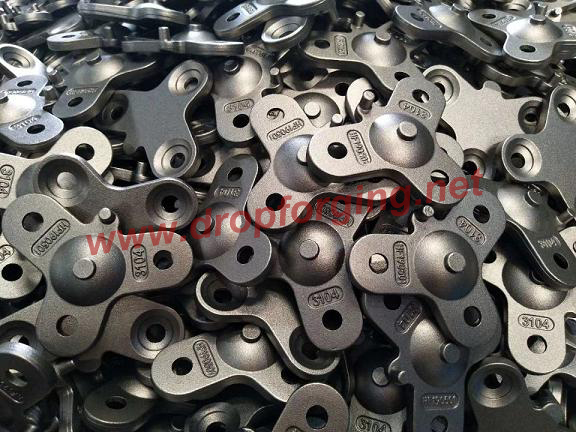
In general, the mechanical performance of castings is lower than that of forgings with the same raw material. In addition, the forging process can ensure the succession of the metal fibers and keep the forged fibers consistent with the shape of the forged pieces. What’s more, the metal streamlines are intact, which can ensure the parts have outstanding mechanical performance and long working life. With the process of precision die forging, cold kneading and warm kneading, forgings are more superior than castings in performance.
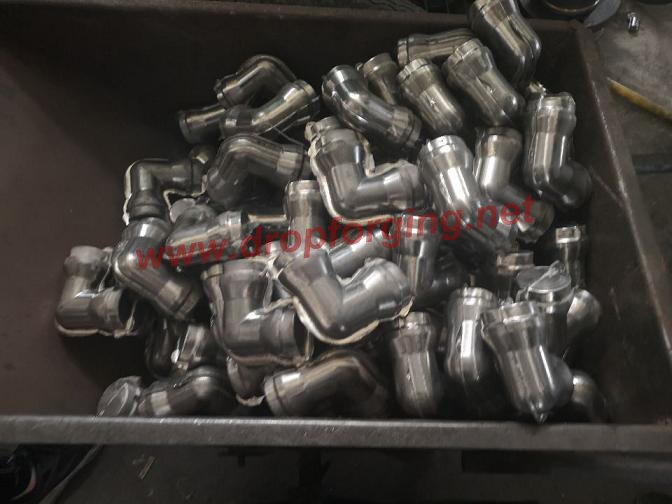
Aluminum forgings have been widely used in various fields such as machinery, aviation, automobiles, railway vehicles, ships ,marine vessles, buildings, bridges, chemicals, and power owing to their excellent properties. By replacing steel forgings with aluminum forgings, it can greatly reduce the weight of mechanical products and increase the structural stability. Therefore, aluminum forgings are essential components in the fields of aviation, aerospace and many defense industry sectors. For example, there are many aluminum forgings used in aircrafts ,which accounts for 15% -50%.
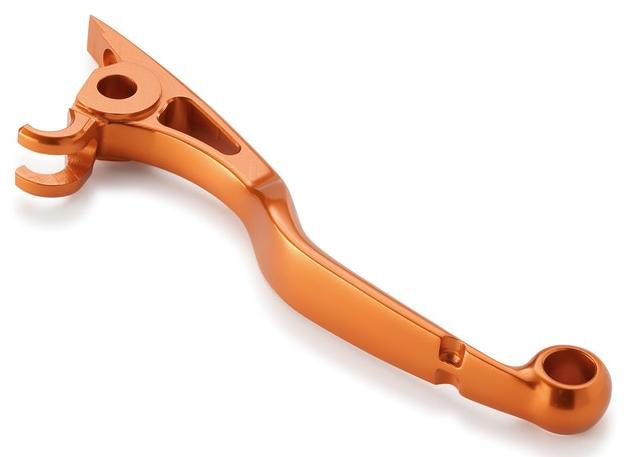
There are several color options for anodized aluminum forgings, taking forged aluminum brake lever for example, one of our customer needs 5 colors: silver natural, black, red light, blue and light grey. This multi-colored anodized aluminum forgings are available from CFS Forge. After coloring, anodized aluminum forgings have a characteristic “metallic” look. This is caused by two factors. One, because of the uniform electro-chemical etching, a rough surface is left behind. The deeper the pores, the rougher the surface will be but the colors will also be that much more durable. Secondly, light striking the surface partly interacts with the colorant and partly with the uncolored metal at the top. So the light that bounces back to strike your eye will in fact be a combination of two distinct wavelengths interacting as they reflect from slightly different surfaces. This causes the distinctive shine of anodized aluminum forgings.