
Drop forging manufacturer

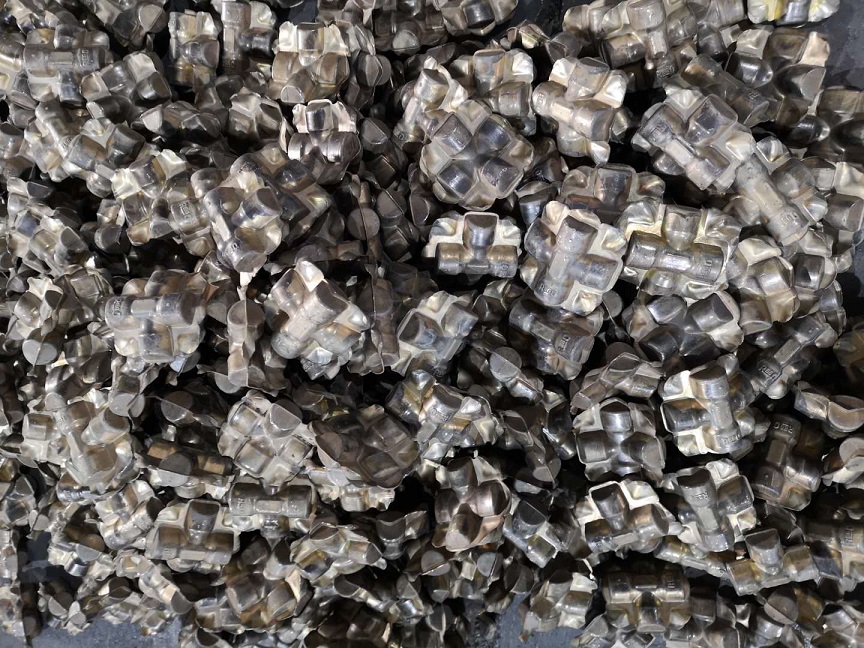
What is forged brass and where is it commonly used? In a nutshell, forged brass is an alloy of copper and zinc that is heated up to 900 degrees Fahrenheit before it is squeezed into shape in precision-machined closed die presses. This gives the resulting material more tensile strength as compared to its molded counterparts.
Depending on the amounts of copper and zinc used, the resulting alloy can provide varying degrees of electrical and thermal conductivity, corrosion resistance, ductility and machinability. The unique metal combination can also determine its joining and plating characteristics, non-magnetic and non-sparking properties and its polishing and finishing characteristics as well.
Why suspension parts? Several reasons. One is that suspension parts are generally dimensioned for dynamic fatigue loads. And any adverse surface quality will impact the fatigue lifetime of the suspension. Another reason is that suspension parts forged from aluminium are the lowest-weight suspension parts in industrial scale use, and weight is particularly important in a vehicle’s unsprung mass. Furthermore, they provide better vehicle response, since the inertia of the parts are reduced, and they lessen the noise from the chassis, which gives you a more comfortable ride. Lastly, by using aluminium, the reduced weight helps you save emissions.
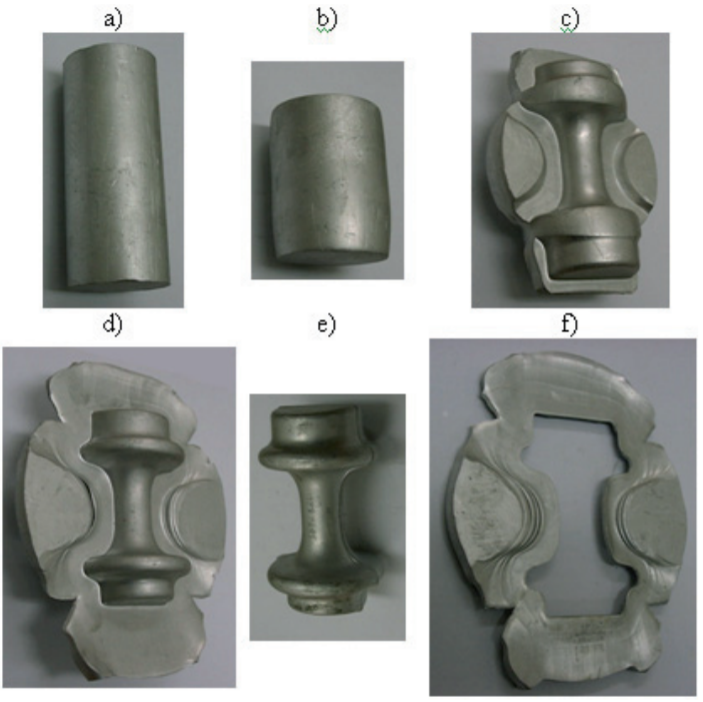
The forgings of wheel hub type are often made by means of drop forging processes realized on presses. Due to the necessity of lightweight structure, wheel hubs are often manufactured by aluminum forging. Forming of drop forged wheel hub is a specific hot forging process and it differs from steel forging process.
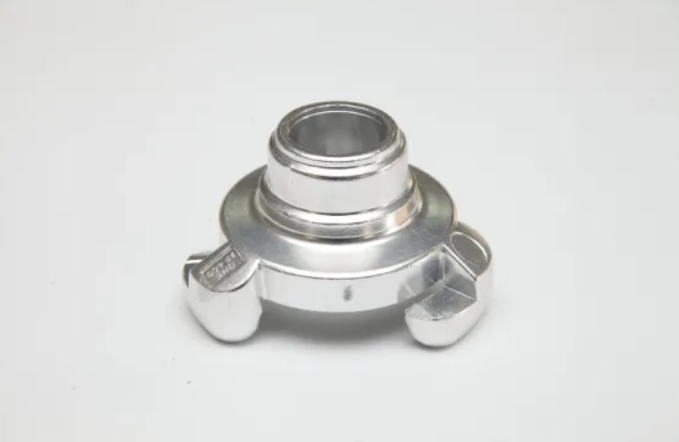
Abstract: It has been proved that forged aluminum alloy is a perfect option compared to steel forgings and cast aluminum parts in the competition for reducing vehicle weight. Additionally, this choice leads to a decisive productivity improvement in the high-volume production under competitive price levels.
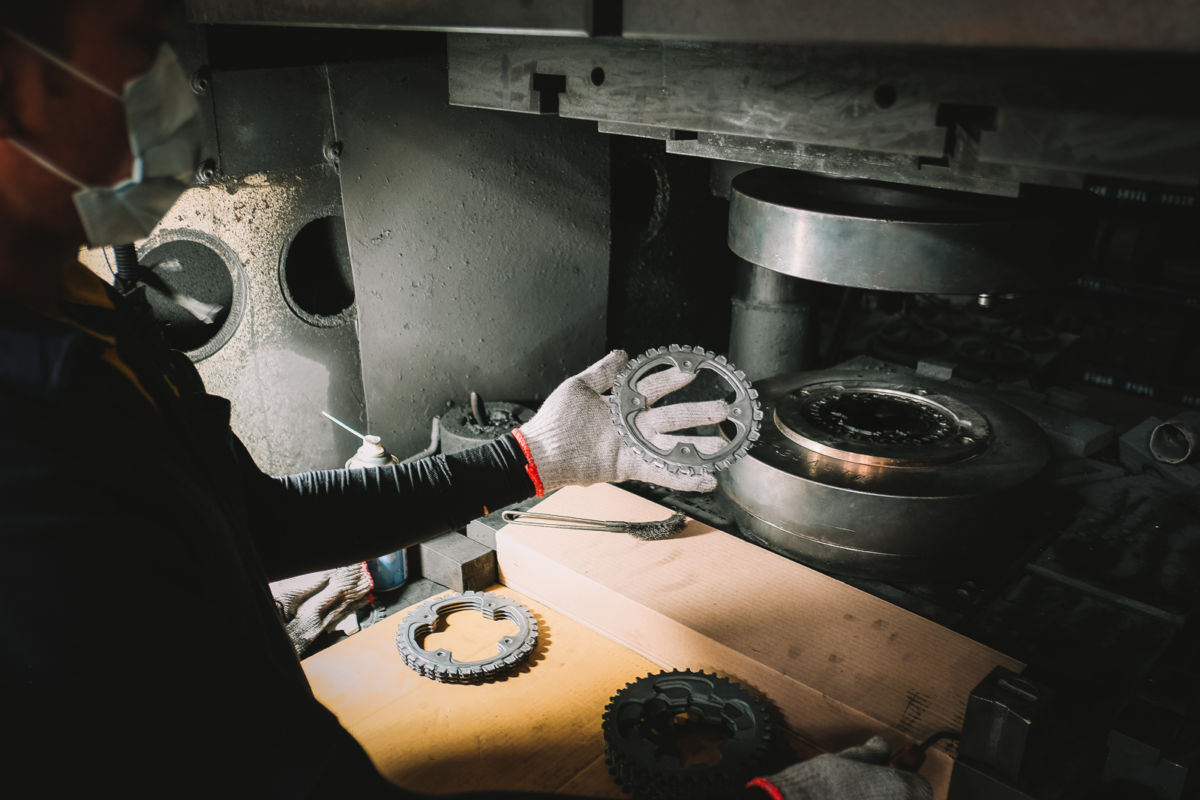
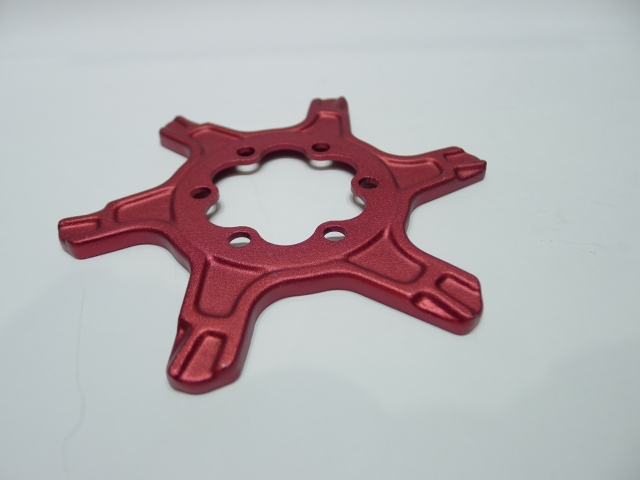
Forging is one of the main manufacturing ways to provide metal blanks for mechanical parts to various industries. The advantage of forging production lies in: it can not only obtain the desired shape, but also improve the internal organization of materials and mechanical properties. For the important mechanical parts with large force and high mechanical performance requirements, most of them are made by forging. Forging parts account for 80% of aircraft parts, 70% of tank parts, 60% of automobile parts. Hydraulic turbine spindle, impeller, rotor, ring guard, etc. in the power industry are all forged.It can be seen that forging production occupies an extremely important position in the industrial applications.
Forged aluminum has the advantages of low density and high strength, so it has been widely used in various industries. Aluminum forging is becoming the main production process of various mechanical parts. Generally, any part forged with low carbon steel can be forged with aluminum alloy in aluminum forging companies. Forged Aluminum parts in various forging equipments such as forging hammer, mechanical press, hydraulic press, die forging, rolling forging and die forging. Generally speaking, aluminum forgings with small size, simple shape and wide tolerance requirements can be easily forged on the forging hammer, but for aluminum forgings with large specifications and severe deformation requirements, hydraulic press is used for forging. Aluminum forgings with large and complex integral structures must be produced by large hydraulic die forging press. For large precision ring parts, precision ring rolling machine should be used for rolling forging.
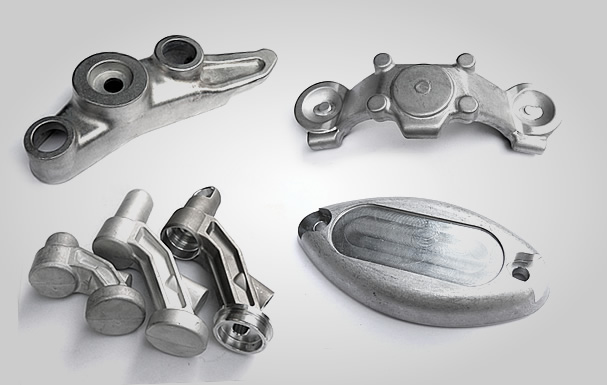
With the characteristics of low density, moderate strength, corrosion resistance, easy shaping, easy welding, beautiful appearance, durability and easy recycling, aluminum alloy should attract more and more attention in motorcycle industry and its applied range should be expanded in the motorcycle industry. In the 21st century, aluminum alloy motorcycle parts should be vigorously developed based on the above advantages.
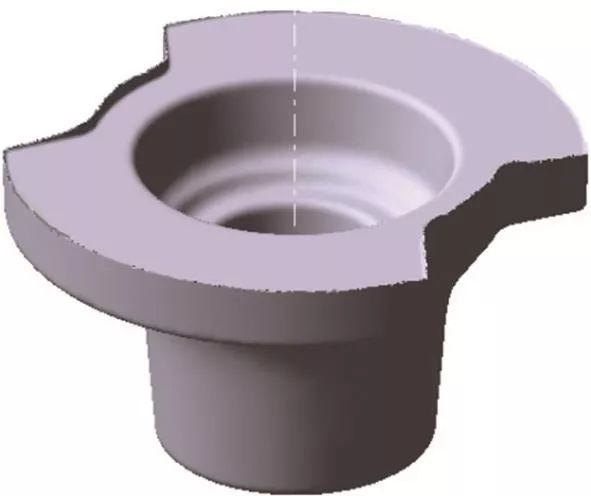
Closed die forging is generally only applied in automotive application, such as automotive gearboxes, housings, flanges, etc. Closed die forging process can greatly improve the material utilization rate and lengthen the life of automotive parts for its good strength. At the same time, it reduces the production cost, thus, it is an ideal target for automotive parts production.
Above introduces the closed die forging process of automotive parts and comes up with new ideas in many designs and it was applied in many fields. This forging process can be widely used in other applications as well. CFS Forge can make closed die forgings in various metals, including steel, aluminum and brass. Any inquiry on closed die forging, pls contact us for a free quote right now!
Vehicle weight reduction is essentially the lightweight of automobile parts. With the forged aluminum alloy wheel hubs, it can greatly reduce the weight of the auto body. For instance, a 40-ton heavy-duty truck and semi-trailer transport system has a total of 22 wheel hubs. It will has 24 wheel hubs if the front and rare spare tires are considered. The vehicle weight will be reduced by nearly 600kg if we replace the frequent used steel hubs with aluminum forged ones. What is more, aluminum alloy materials have good heat dissipation, which can slow down the aging speed of tire rubber to a certain extent. Trucks, buses and trailers equipped with forged aluminum alloy wheels can save 26% of tire consumption.
A plenty of commercial vehicles are equipped with aluminum forged wheels in America and Canada. This also occurs in Europe, South Africa and Australia. Along with the development of China's automobile lightweight technology and the rising fuel prices in recent years, the replacement of traditional automobile wheels with aluminum alloy wheels has become a trend. As a professional drop forging manufacturer, we would like to describe a practical closed die forging process of aluminum alloy wheel hub, by using UG three-dimensional modeling, the forgings are designed and then the wheel hub closed tooling formwork is designed. Then the 3D model is imported into the Deform simulation analysis software to conduct the forging simulation. Based on the analysis of the simulation process, the blank displacement, the filling degree of the material as well as the temperature distribution, the forging general process is preliminarily obtained.
1. Large-grained
Due to too high initial aluminum forging temperature and insufficient deformation degree, or too high final forging temperature, or deformation degree fell into the critical deformation zone. Aluminum alloy deformation degree is too large, forming texture; Superalloy deformation temperature is too low, the formation of mixed deformation microstructure may also cause coarse grains.
The ductility and toughness of aluminum forgings will be reduced and the fatigue performance will be obviously decreased. Uneven grain size: refers to the fact that the grain size in some parts of the forging is particularly large and smaller in some parts. The main reason for the unevenness of grains is that the unevenness of deformation in different parts of the blank results in different degree of grain breakage, or the degree of deformation in local areas falls into the critical deformation zone, or the local processing hardening of superalloy, or the local coarse grains in quenching.Heat resistant steels and superalloys are particularly sensitive to uneven grain size. The unevenness of grain will obviously decrease the endurance and fatigue performance of aluminum forgings.