Understanding the Uses and Importance of Forged Brass
What is forged brass and where is it commonly used? In a nutshell, forged brass is an alloy of copper and zinc that is heated up to 900 degrees Fahrenheit before it is squeezed into shape in precision-machined closed die presses. This gives the resulting material more tensile strength as compared to its molded counterparts.
Depending on the amounts of copper and zinc used, the resulting alloy can provide varying degrees of electrical and thermal conductivity, corrosion resistance, ductility and machinability. The unique metal combination can also determine its joining and plating characteristics, non-magnetic and non-sparking properties and its polishing and finishing characteristics as well.
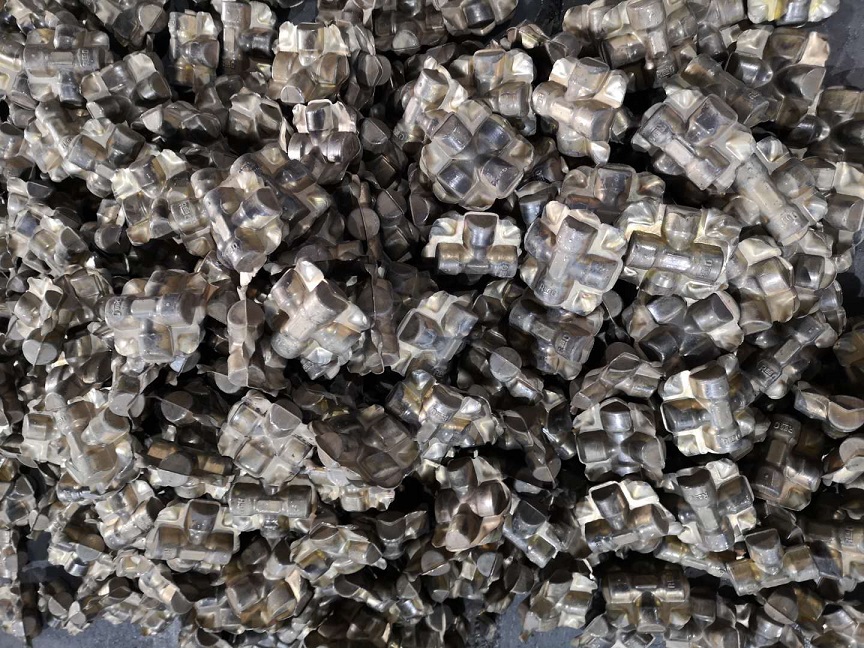
This metal alloy can be used in a wide variety of applications. It can be used in the manufacture of:
There are a number of advantages that comes with forging metal alloys such as brass. These include the following:
Depending on the amounts of copper and zinc used, the resulting alloy can provide varying degrees of electrical and thermal conductivity, corrosion resistance, ductility and machinability. The unique metal combination can also determine its joining and plating characteristics, non-magnetic and non-sparking properties and its polishing and finishing characteristics as well.
What are the Uses and Applications of Forged Brass?
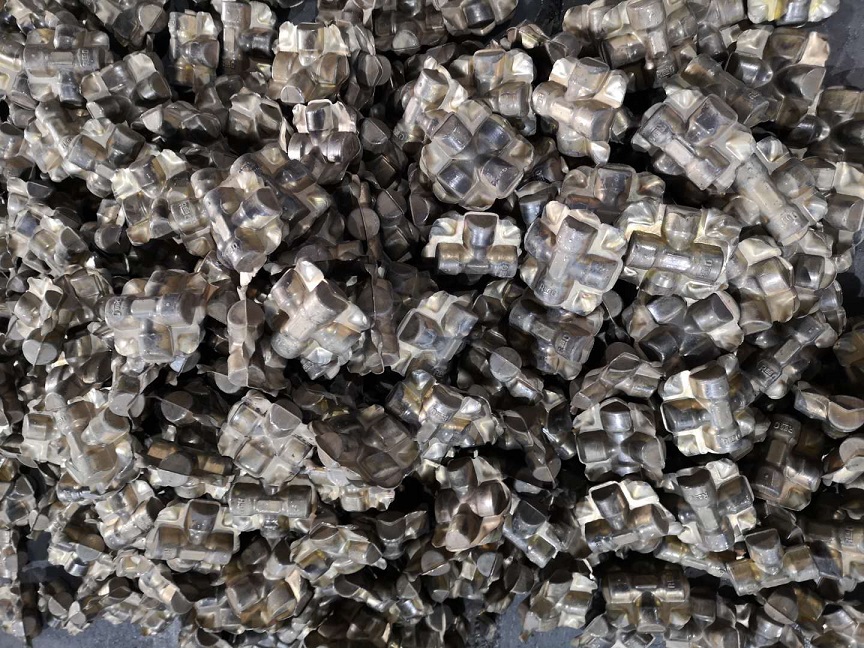
This metal alloy can be used in a wide variety of applications. It can be used in the manufacture of:
- Bathroom accessories such as doorknobs and locks, faucets, piping and gears
- Musical instruments such as bells, cymbals, harmonicas, horns and saxophones
- Automotive, electrical and electronic parts
- Plumbing
- Solenoid, valves and hydraulic fittings
- Building hardware
- Heating, ventilation and air conditioning
- Medical appliances
- Marine hardware, pump shafts and condenser plates
- Seawater piping
What are the Advantages of Using Forged Brass?
There are a number of advantages that comes with forging metal alloys such as brass. These include the following:
- Greater material strength. Forged materials have closer grains and are virtually free from porosity. Subjecting the alloy under extreme pressure and temperature produces an extremely tensile material with a very dense grain structure.
- Leak resistance. Due to its extremely dense grain structure, forged brass is virtually leak-free, no matter how thin it may be.
- Higher production rate. As compared to casting, forging provides higher production rates.
- Less amount of scrap. The absence of porosity reduces waste and generates significant material savings.
- Easier to shape. Brass can be extremely ductile at forging temperatures. This makes it easier to form into complex components. By using forging techniques, incorporating intricate details into the design can also be quite easy.
- Superior surface finish. Forged brass components do not require grinding or sanding. As such, it can easily be applied a variety of finishes.
- Lower tool cost. Forging tools are relatively cheaper and have longer machine tool life as compared to casting tools.