Differences Between Forging and Rolling
Forging
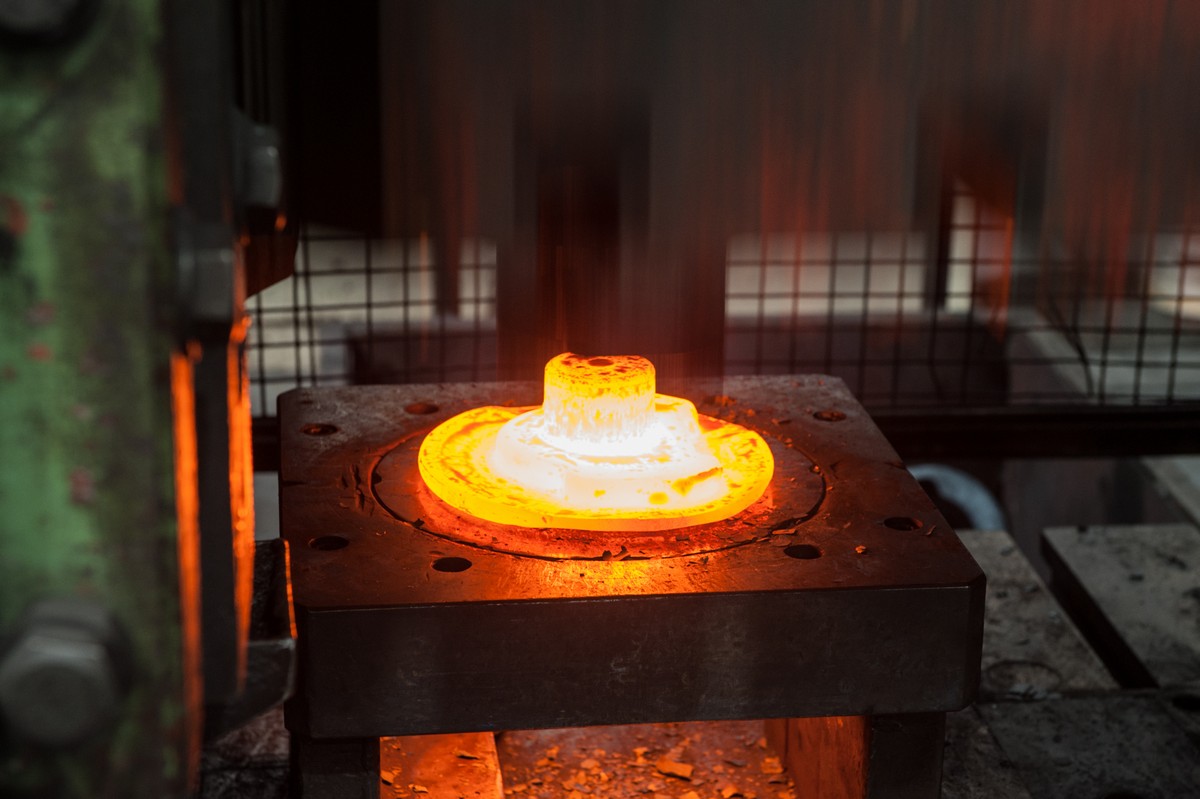
It refers to the processing method by using a forging machine to apply pressure to a metal blank and get the plastic deformation,which will achieve certain mechanical properties, a certain shape and size. With forging, it can eliminate defects such as as-cast looseness caused by metal in the smelting process and optimize the microstructure. At the same time, the mechanical properties of the forgings are generally better than those of the same materials due to the preservation of the complete metal flow lines. For important parts of the relevant machinery with high load and severe working conditions, forgings are often used except for the available rolled sheets, profiles or welded parts .
Forging can be divided into free forging, die forging and flashless die forging
- Free forging. The impact force or pressure is used to deform the metal between the upper and lower two irons (anvil) to obtain the required forgings. This type of forging is mainly divided into hand forging and mechanical forging.
- Die forging. Die forging is divided into open die forging and clsoed die forging. Forgings are obtained when metal blanks are pressed and deformed in a forged die with a certain shape and it can be divided into cold heading, roll forging, radial forging and extrusion. CFS Forge is good at forging process in closed dies. We are able to forge components in steel, aluminum and copper.
- Since there is no flash in flashless die forging and flashless upsetting , so the material utilization rate is high. It is possible to finish the complex forgings with one or several processes. Because there is no flash, the area of the force applied to the forging is reduced and the required load is also reduced. However, it should be noticed that the blank material should not be completely limited . To this end, the volume of the blank is strictly controlled, the relative position of the forging die should be controlled and the forging is measured to reduce the abrasion of the forging die.
Compared with castings, metals’ microstructure and mechanical properties can be improved after forging. After the hot-working deformation of the cast structure by the forging method, the original coarse dendritic crystal and columnar grains become the equiaxed recrystallized structure with fine grains and uniform size due to the deformation and recrystallization of the metal, so that the original segregation in the steel ingot, loosen, stomata and slag inclusions can be compacted and welded, the plasticity and mechanical properties of the metal can be improved by the compacted structure.The mechanical properties of castings are lower than those of forgings of the same material. What is more, the forging can ensure the continuity of the metal fiber structure, so that the fiber structure of the forging piece is consistent with the shape of the forging piece and the metal streamline is complete, which can ensure the good mechanical properties and long service life of the forging pieces produced by precision die forging,cold extrusion and warm extrusion. These features are superior to the castings.
Rolling
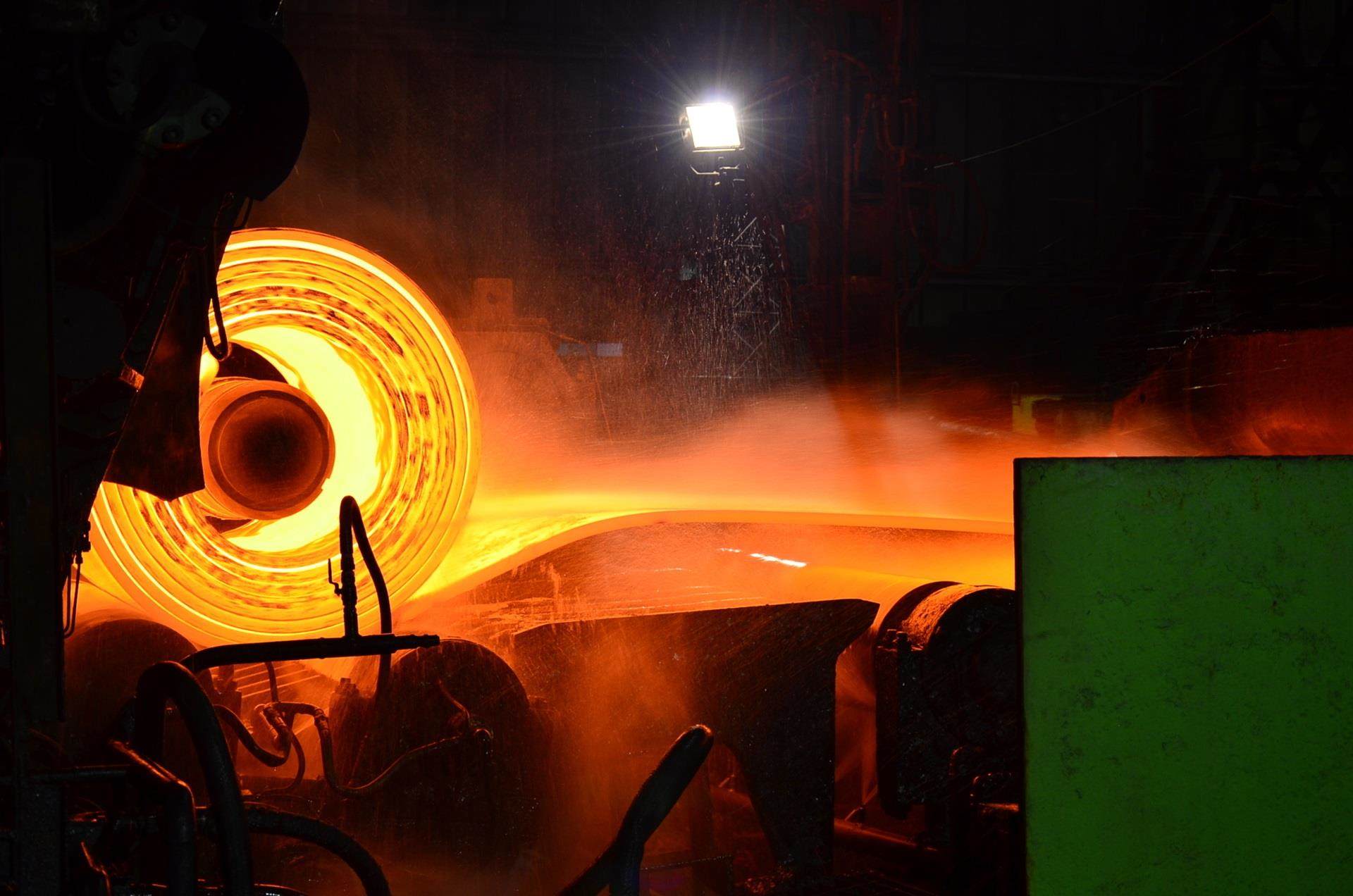
With the gap (various shapes) of a pair of rotating rolls in metal blank,the material’s section is reduced owing to the rolls compression, and the length is increased, this is the most common production method for steel, such as profiles, plates and pipes.
According to the rolled piece motion, the rolling method can be divided into three parts: longitudinal rolling, cross rolling and skew rolling.
- Longitudinal rolling:It refers to the process of plastic deformation in which metal passes through the two rolls of opposite directions of rotation.
- Cross rolling: The motion direction of the rolled piece after deformation is consistent with the direction of the roll axis.
- Skew rolling: The rolling piece is spirally moved, the rolling piece and the roll axis are not angled.
It destroyed the cast structure of the steel ingot, the crystalline grain of the steel can be refined, and the microstructure can be eliminated, so that the steel structure is compacted and the mechanical properties are improved, which is mainly reflected in the rolling direction. To a certain extent, the steel is no longer isotropic, bubbles, cracks and looseness formed during casting can also be welded under high temperature and pressure.
Defects
- The non-metallic inclusions (mainly sulfides , oxides and silicates) inside the steel are pressed into thin sheets after rolling,and delamination (sandwich) occurs. The delamination greatly deteriorates the tensile properties of the steel in the thickness direction, and it is possible that interlaminar tearing occurs when the welding line is shrunk. The local strain induced by welding line shrinkage is often several times the yield point strain and is much larger than the strain caused by the load.
- Residual stress caused by uneven cooling. The residual stress refers to the internal self-phase balanced stress without external force. The hot-rolled steel of various sections has such residual stress. The larger is the section size of the general steel, the larger is the residual stress. Although the residual stress is self-phase-balanced, it still has some influences on the performance of steel members under external force,such as deformation, stability, fatigue and others.
- It is not well controlled for thickness and side width as for hot rolled steel products. We are familiar with the rule of thermal expansion and cold shrinkage. At the beginning,the length and thickness of hot rolling are up to standard,but there will be a certain minus tolerance after cooling. The wider side width and the thicker thickness caused by the minus tolerance are becoming obvious. Therefore,as for large steel, the side width, thickness, length, angle, and edge of the steel cannot be too precise.
Differences Between Forging & Rolling
- The difference of the axial and radial mechanical properties of the forging piece is smaller than that of the rolling piece. That is to say, the isotropy of the forgings is much higher than that of the rolling pieces, so the life of the forgings is much longer than the rolled pieces.
- From the perspective of deformation degree, the deformation degree of the forging is much greater than that of the rolled piece, that is, the effect of breaking the eutectic carbide by forging is better than that of rolling.
- In terms of processing cost, the cost of forging is much higher than rolling. For some key pieces, workpieces subjected to large loads or impacts as well as some workpieces with complex shapes or very strict requirements, it is necessary to use forging process .
- The forging piece has a complete metal streamline. The machinist destroy the integrity of the metal streamline after rolling , which greatly shortens the life of the workpiece.