Forged Aluminum Alloy On Motorcycle Industry
With the characteristics of low density, moderate strength, corrosion resistance, easy shaping, easy welding, beautiful appearance, durability and easy recycling, aluminum forging should attract more and more attention in motorcycle industry and its applied range should be expanded in the motorcycle industry. In the 21st century, aluminum forged motorcycle parts should be vigorously developed based on the above advantages.
Almost all steel parts on motorcycles can be replaced by aluminum alloy materials under the continuous efforts of the related professional and technical personnel in motorcycle industry. In recent years, with the increasing demands of international environmental protection and national and regional government energy conservation regulations, motorcycles are moving toward a tendency of “green motorcycle” that is lightweight, high-speed, safe, comfortable and environmentally friendly. Undoubtedly, it will promote the application of aluminum alloy materials on motorcycles. Forged aluminum alloy is particularly important in its material application.
Why Forged Aluminum for Motorcycle Industry?
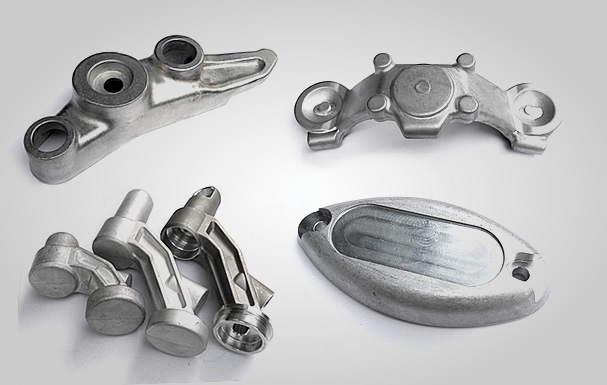
Hot-rolled aluminum alloy has the advantages of improved metal process performance, high yield and high productivity, but it cannot produce parts with accurate profile and smooth surface, and product performance can not be controlled well. In addition, the uniformity of the hot-rolled aluminum alloy structure can not be guaranteed and the performance difference is big. The extrusion process has the advantages of accurate production profile, high surface quality and no need for processing. However, there are problems such as large loss of geometric waste, low productivity, low yield, and high production cost. What is more, the unevenness degree of the extruded product is higher than that of hot rolling. The essence of forged aluminum alloy is plastic shaping of metal. It is a process of making the blank into a certain shape under the impact or pressure of tool. The purpose of forging processing is not only to obtain accurate parts of the profile, but also to improve the structure as well as the mechanical properties compared to other processing methods. Obviously, it is necessary to develop and expand the application of forged aluminum alloy motorcycle parts, such as motorcycle brake caliper.
With good plasticity of soft aluminum alloys and medium-strength aluminum alloys, they can be forged under various stress-strain conditions. High-strength aluminum alloys are poorly plastic, so they should be forged under the most favorable stress-strain condition. Generally, the aluminum alloy ingot should be subjected to extrusion deformation in advance, and its deformation amount is generally in the range of 50% to 60% or more. When designing a motorcycle part with forged aluminum alloy, it is important to know how to select a suitable alloy for aluminum forging.
The selection principle is:
- To ensure that the material has the best forgeability in the forging temperature range, and has the widest temperature range to reduce the heating times;
- No damage to the material caused by heating is required;
- To ensure that the best internal structure and highest mechanical properties can be obtained after forging.
Additionally, the appropriate deformation degree should be selected. The deformation degree allowed for the aluminum alloy is reduced depending on the alloying degree of the alloy and the increase in the deformation speed. The deformation speed refers to the amount of change in deformation per unit time. The deformation speed is not only related to the working speed of the equipment, but also depends on the size of the blank itself and the type of process performed. The deformation speed not only affects the plasticity of the alloy, but also the deformed structure. It is more scientific to use a forged aluminum alloy on a press in order to improve the degree of deformation and productivity allowed during processing, reduce the deformation resistance and improve the internal structure of the metal.
Rather than steel, to produce motorcycle parts by using forged aluminum alloy can not only lower the material cost, but also can reduce the motorcycle weight as well as energy consumption, and improve transportation capacity. Absolutely, the wide application of forged aluminum motorcycle parts will promote the survival and development of the aluminum metal industry. CFS Drop Forging Company is the professional aluminum forging company in China, we can produce various custom forged aluminum parts for motorcycle industry. Contact us if you have any demands!