Drop Forging Basics
Drop Forging: To apply external force to metal blanks (excluding sheet metal) and make them plastically deformed, change their dimensions, shapes as well as improve their performance. Drop Forging is used as the forming processing methods for mechanical parts, workpieces or blanks.
The deformation resistance will decrease sharply and the deformation level will be greatly reduced when the temperature exceeds 300-400 ℃ (blue brittle zone of steel) and reaches 700-800 ℃. Drop forging can be divided into three forming temperature regions, namely: cold forging, warm forging, and hot forging. Originally, there was no severe boundary in the temperature range. Generally, drop forging in a temperature region with recrystallization is called hot forging, and drop forging without heating at room temperature is called cold forging.
The dimensions of drop forgings change little when they were in low temperature forging. It has less oxide skin structure and no decarburization on the surface when the drop forging temperature is below 700°C. Therefore, high dimensional accuracy and surface smoothness will be easily obtained in cold forging as long as the deformation energy is within the range of the forming energy. High accuracy can also be achieved in warm forging below 700 ° C when the drop forging temperature and smooth cooling are well controlled. In hot forging, large forgings with chaotic shapes can be forged since the deformation energy and deformation resistance are very small. In order to obtain high-precision forgings, hot forging can be used in the temperature range of 900-1000°C. Additionally, the working environment of hot forging should be improved. Compared to drop forging in other temperature ranges, the life of forging die (2 to 5000 for hot forging, 10,000 for warm forging, 20,000 for cold forging) is shorter, but it has greater degree of freedom and lower cost .
During cold forging, the blanks will experience deformation and work hardening , which makes the forging die receives high loads. Therefore, it is necessary to use a high-strength forging die and choose a hard smooth film treatment method to avoid wear and adhesion. In addition, in order to avoid cracks in the blank, intermediate annealing is employed to ensure the required deformation. To obtain perfect smoothness, the blank can be phosphated. In the connect processing of bars and wire rods, the cross section cannot be smoothed at present, and the possibile method of using a phosphating smoothing is being studied.
Drop forgings can be divided into open die forging, closed die forging and roll forging according to the blank moving method. With open die drop forging, the utilization rate of the material is high because they do not have flash. The finishing of the open die forgings may be completed in one process or several processes. Both the force bearing area of the forging and the required load are reduced because they have no flash. However, it should be noted that the blank cannot be completely restrained. For this reason, the volume of the blank must be strictly controlled. The relative
orientation of the forging die and the measurement of the forging must be controlled and every effort must be made to reduce the wear of the forging die.
Compared with Castings, What are the Advantages of Drop Forgings?
By employing drop forging process, metals (steel, aluminum or copper) can improve its structure and mechanical performance. The drop forgings are deformed by hot processing. Owing to the deformation and recrystallization of the metal, the original coarse dendrites and columnar grains become equiaxed recrystallization with finer grains and uniform size, then the original segregation, looseness, pores and slag inclusions in the ingot are compacted and welded and their structure will become tighter. The plasticity and mechanical performance of the metal are further improved.
In general, the mechanical performance of castings is lower than that of forgings with the same raw material. In addition, the forging process can ensure the succession of the metal fibers and keep the forged fibers consistent with the shape of the forged pieces. What’s more, the metal streamlines are intact, which can ensure the parts have outstanding mechanical performance and long working life. With the process of precision die forging, cold kneading and warm kneading, forgings are more superior than castings in performance.
Drop Forging Types and Characteristics
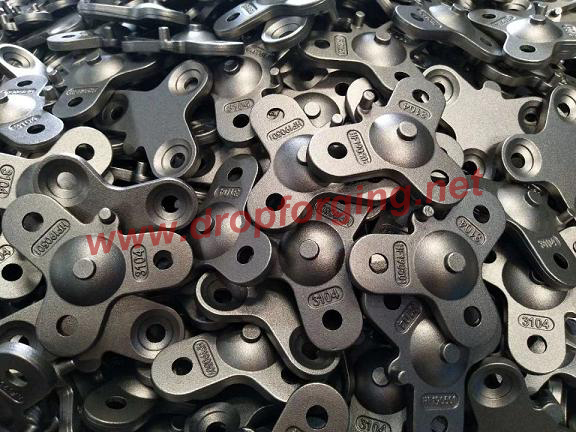
The dimensions of drop forgings change little when they were in low temperature forging. It has less oxide skin structure and no decarburization on the surface when the drop forging temperature is below 700°C. Therefore, high dimensional accuracy and surface smoothness will be easily obtained in cold forging as long as the deformation energy is within the range of the forming energy. High accuracy can also be achieved in warm forging below 700 ° C when the drop forging temperature and smooth cooling are well controlled. In hot forging, large forgings with chaotic shapes can be forged since the deformation energy and deformation resistance are very small. In order to obtain high-precision forgings, hot forging can be used in the temperature range of 900-1000°C. Additionally, the working environment of hot forging should be improved. Compared to drop forging in other temperature ranges, the life of forging die (2 to 5000 for hot forging, 10,000 for warm forging, 20,000 for cold forging) is shorter, but it has greater degree of freedom and lower cost .
During cold forging, the blanks will experience deformation and work hardening , which makes the forging die receives high loads. Therefore, it is necessary to use a high-strength forging die and choose a hard smooth film treatment method to avoid wear and adhesion. In addition, in order to avoid cracks in the blank, intermediate annealing is employed to ensure the required deformation. To obtain perfect smoothness, the blank can be phosphated. In the connect processing of bars and wire rods, the cross section cannot be smoothed at present, and the possibile method of using a phosphating smoothing is being studied.
Drop forgings can be divided into open die forging, closed die forging and roll forging according to the blank moving method. With open die drop forging, the utilization rate of the material is high because they do not have flash. The finishing of the open die forgings may be completed in one process or several processes. Both the force bearing area of the forging and the required load are reduced because they have no flash. However, it should be noted that the blank cannot be completely restrained. For this reason, the volume of the blank must be strictly controlled. The relative
orientation of the forging die and the measurement of the forging must be controlled and every effort must be made to reduce the wear of the forging die.
Compared with Castings, What are the Advantages of Drop Forgings?
By employing drop forging process, metals (steel, aluminum or copper) can improve its structure and mechanical performance. The drop forgings are deformed by hot processing. Owing to the deformation and recrystallization of the metal, the original coarse dendrites and columnar grains become equiaxed recrystallization with finer grains and uniform size, then the original segregation, looseness, pores and slag inclusions in the ingot are compacted and welded and their structure will become tighter. The plasticity and mechanical performance of the metal are further improved.
In general, the mechanical performance of castings is lower than that of forgings with the same raw material. In addition, the forging process can ensure the succession of the metal fibers and keep the forged fibers consistent with the shape of the forged pieces. What’s more, the metal streamlines are intact, which can ensure the parts have outstanding mechanical performance and long working life. With the process of precision die forging, cold kneading and warm kneading, forgings are more superior than castings in performance.