
Drop forging manufacturer

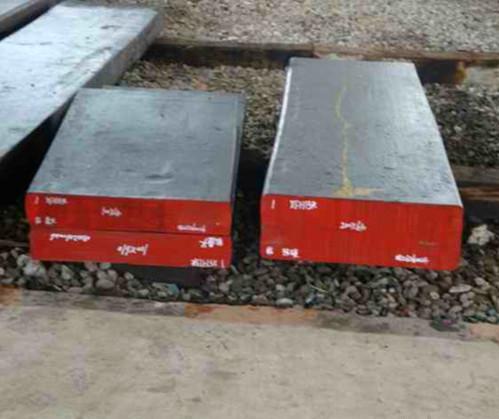
In drop forging production,we will need making forging dies first for closed die drop forgings.And we call the material of drop forging dies is die steel.So to start a new product,drop forging manufacturers have to buy die steel first.Selecting a die steel supplier is a key decision for all parties, including the die maker,the die user and the end user.Thanks to superior material properties,ourcustomers get reliable tools and components. Our products are always state-of-the-art. Consequently, we have built a reputation as the most innovative dies producer in the world.
We produce and deliver high quality drop forgings to more than 100,000 customers in over 100 countries.Together we secure our position as a world-leading supplier of dies and drop forgings.
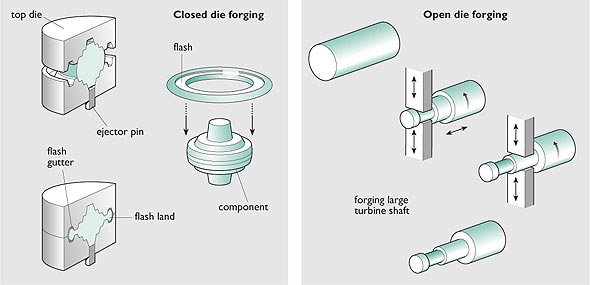
In modern society,forging industry is involved in various industries for construction machines,agricultural machinery,automotive,oilfield equipments,ect.Steel billets could be processed by various forging processes,among them the common used forging ways are closed die forging and open die forging.Although these two forging methods all belong to forging,it is not difficult to tell the difference between closed die forging and open die forging.The biggest difference of them is forging dies.Now let us have a deeper comparison on the differences between them.
Definition
Open die forging is also named free forging,means metal billets compressed under external compressive force and deformed to desired demensions or shapes in a free way without forging dies.Closed die forging,also referred to impression die forging,is a process that heated by medium frenquency induction heating furnace to high temperature and forged between upper and lower dies to get expected shapes like the drawing.
Although there are a variety of advantages of drop forging technology compared to other metal forming processes,there may still exsit some defects in hot forging process. Such drop forging defects can be split into two broad types:geometrical defects and non geometrical defects.
Geometrical defects of drop forging
*Laps and folds: Laps and folds are produced due to improper design of drop forging dies, making the laps created onto the final component which is rather undesirable as make irregular surface finish and also may weaken the product for internal or external cracks.
*Unfilled defects: There may exsit some sections of die cavity not completely filled by the flowing steel. This defects happen due to the improper design of drop forging dies or not using the right forging process.
Geometrical defects of drop forging
*Laps and folds: Laps and folds are produced due to improper design of drop forging dies, making the laps created onto the final component which is rather undesirable as make irregular surface finish and also may weaken the product for internal or external cracks.
*Unfilled defects: There may exsit some sections of die cavity not completely filled by the flowing steel. This defects happen due to the improper design of drop forging dies or not using the right forging process.
There are different types of forgings, drop forging (closed die forging and open die forging), cold forging, samless rolled ring forging. So forging can generally divided into hot forging and cold forging. Cold forging is a forging process mufacturing in room temperature, however hot forging is a forging process in high temperature, so it is also referred to as drop forging. We can use hot forging to produce a wide range of parts in most metals. So we may be wondering why drop forging is hot forging, not cold forging?
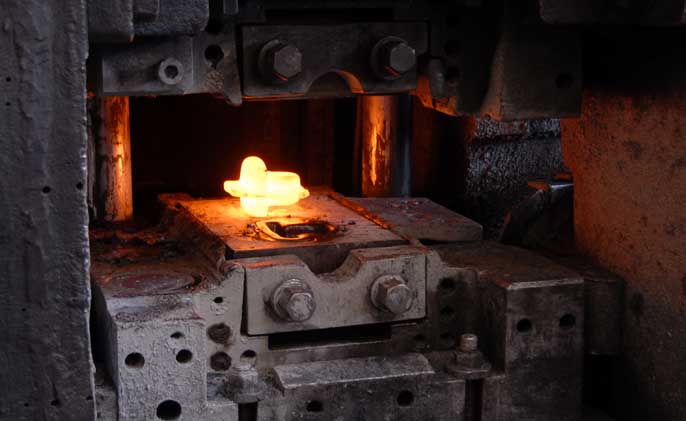
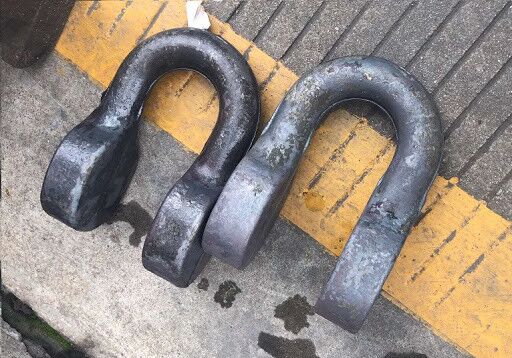
Benefits of forged steel
- Forged steel require an initial cost for the design and making of dies. But it has low recurring cost for each parts,so drop forging gradually become more economical with large volume.
- During drop forging process, metals are shaped to follow the designed shape of part while its internal grain deforms. Then, the grain is continuous throughout the part and make forged steel parts with improved strength. Therefore, forged steel has higher strength to weight ratio compared to cast steel,at least 20% higher.
- Forged steel is the right alternation of aluminum for its low cost in many applications. And forged steel has three times as strongth as aluminium although it is much heavier.
Background
For the advantages of drop forging, such as it can bear high power,this process is widely used for all industrial manufacturing. In all the metal forming process, we can say drop forging is the best solution for your steel parts. So today more and more buyers use drop forging as the production process,especially for those components in large production runs. Most drop forging manufacturers supply OEM service for their customers, so buyers can forge any shapes they like, of course, such shapes must comply with drop forging technology and the dimensions can not exceed the range of the largest forging press allows. There are many drop forging companies all over the world, and buyer can choose to custom drop forgings in any countries (USA, UK, Australia, China,etc) they like. In comparison, they prefer to buying in China for the low price. But due to the lack of understanding of Chinese drop forging industry, buyers do not know how to make the parts in China.
For the advantages of drop forging, such as it can bear high power,this process is widely used for all industrial manufacturing. In all the metal forming process, we can say drop forging is the best solution for your steel parts. So today more and more buyers use drop forging as the production process,especially for those components in large production runs. Most drop forging manufacturers supply OEM service for their customers, so buyers can forge any shapes they like, of course, such shapes must comply with drop forging technology and the dimensions can not exceed the range of the largest forging press allows. There are many drop forging companies all over the world, and buyer can choose to custom drop forgings in any countries (USA, UK, Australia, China,etc) they like. In comparison, they prefer to buying in China for the low price. But due to the lack of understanding of Chinese drop forging industry, buyers do not know how to make the parts in China.
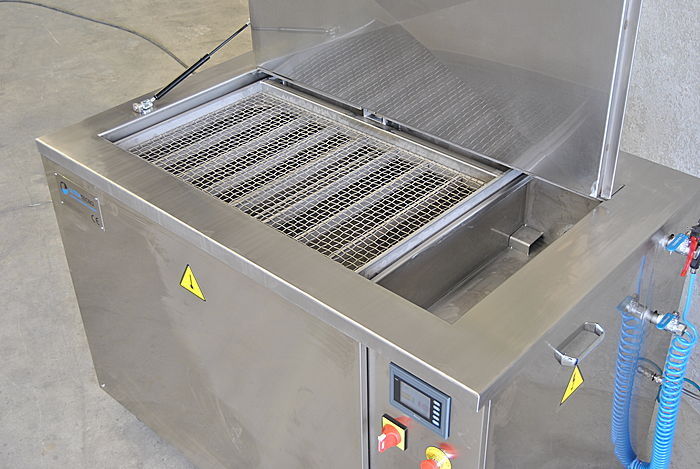
The process is brought about by high frequency electrical energy that is converted by a transducer into high frequency sound waves – ultrasonic energy. Its ability to clean drop forgings even the most tenacious substances from items derives from the core of the unit: the transducer. The cleaning power of a unit stems from the transducers performance.

Main forged fittings include: elbow, flange, tee, union, coupling, cap, etc.
Main standard: American standard ANSI, German standard DIN, Janpanese standard JIS and Chinese GB/T, etc.
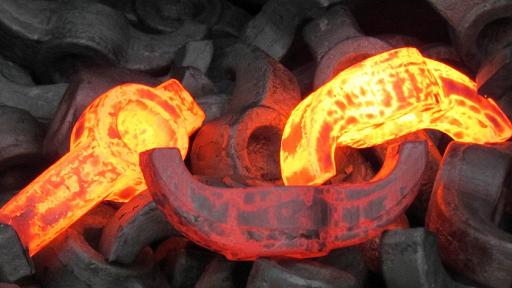
When we have such doubt or similar, just pls analyze the processes we may choose. Why use drop forging? Forging and casting are two very different manufacturing methods. When something is cast,the material is heated above its melting temperature and poured into a mold where it solidifies. When something is drop forged it is physically forced into shape while remaining in a solid state – although it is frequently heated.Below is our testing result on if drop forging is the best solution for steel parts production:
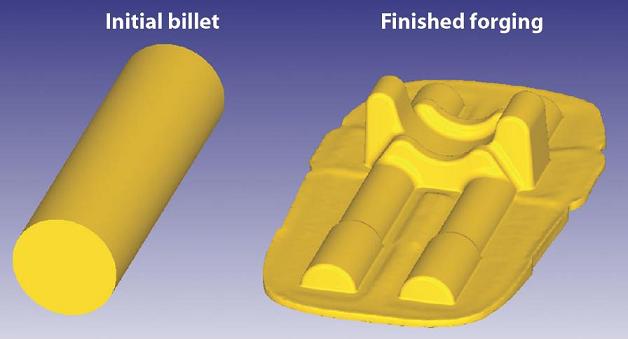
Drop forged components make possible designs that accommodate the highest loads and stresses. Recent advances in drop forging technology have greatly increased the range of properties available in steel forgings. To the designer,the structural integrity of forgings means safety factors based on material that will respond predictably to its environment without costly special processing to correct for internal defects.
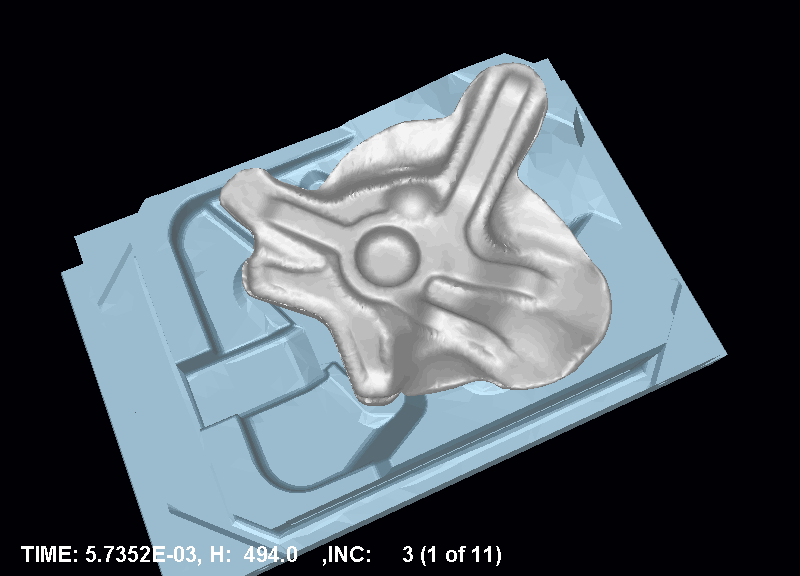
Closed die forging is distinct from open die forging, in which the die only comes into contact with part of the workpiece at a time.Initial costs for developing the processes and tooling for closed die forging can be quite high,but it is the most cost-effective forging method for high volume production,since recurring costs for each part are very low.In addition,closed die forging is capable of producing both symmetrical and non-symmetrical parts. Materials that frequently undergo closed die forging processes include high alloy steel, naval brass,carbon steel,aluminum,alloy metals,stainless steel,copper, nickel,tool steel and titanium.Closed die forgings are used particularly often by industries such as electronics,aerospace,automotive,commercial,manufacturing,semiconductor,construction,hardware and food processing.

Drawing number
Drawing number is used to name a drop forging part so that we could check the part accordingly. In most cases,the drawing number(such as FLY151006) is made up of letter and numbers (letters could be the abbreviation of company namer, numbers could be the date or product serial number). When communicate with our customers, both of us will know which one we are talking about. And for next order, purchaser will just advise the drawing number in the PO.