
Drop forging manufacturer

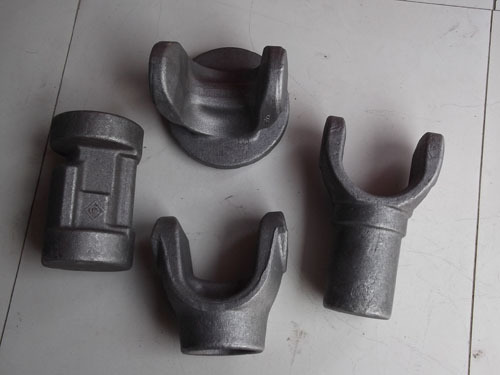
But to offer a quote completely,we still need to know if our customer could send us the detailed 2d drawing or sample.Since we could do cost estimation of the product correctly,and especially need to note if there is any machining requirements,as machining cost will be added for any machining job,although we have machining capability.
For the advantages of drop forging,it is always used to make metal parts.Drop forging design is the first step for starting a new part,and such design will follow the application and assembling of products.And drop forging products will be compressed in a closed die upper and lower dies to get desired shapes,after that we will see trimming around the products,which will be cut in punching machine,then forging blanks will be born.So before put into production,designer should consider in a whole way for following aspects:
Parting line
The forging dies will decide the postion of parting line around the edges of drop forgings.So it is a important thing to determine the position of parting line.The choice of parting line will directly affect waste material,machining allowance.Designer should indicate the position of parting line in the forging drawing clearly.It is better that the parting line lies in one plane perpendicular to the axis of the die motion. It can be located such that one die half will be completely flat, and the line will surround the largest projected area of the piece. The angle of the surface at the parting line from the primary parting plane should not exceed 75°, in general, the shallower the angles,the better it will be. It is crucial for designer to select the parting line such that no undercuts are in either die impression,since the forging must be ejected out of the die after it is made.The parting line location can be changed to control the grain direction given the above recommendations are fulfilled.
Parting line
The forging dies will decide the postion of parting line around the edges of drop forgings.So it is a important thing to determine the position of parting line.The choice of parting line will directly affect waste material,machining allowance.Designer should indicate the position of parting line in the forging drawing clearly.It is better that the parting line lies in one plane perpendicular to the axis of the die motion. It can be located such that one die half will be completely flat, and the line will surround the largest projected area of the piece. The angle of the surface at the parting line from the primary parting plane should not exceed 75°, in general, the shallower the angles,the better it will be. It is crucial for designer to select the parting line such that no undercuts are in either die impression,since the forging must be ejected out of the die after it is made.The parting line location can be changed to control the grain direction given the above recommendations are fulfilled.
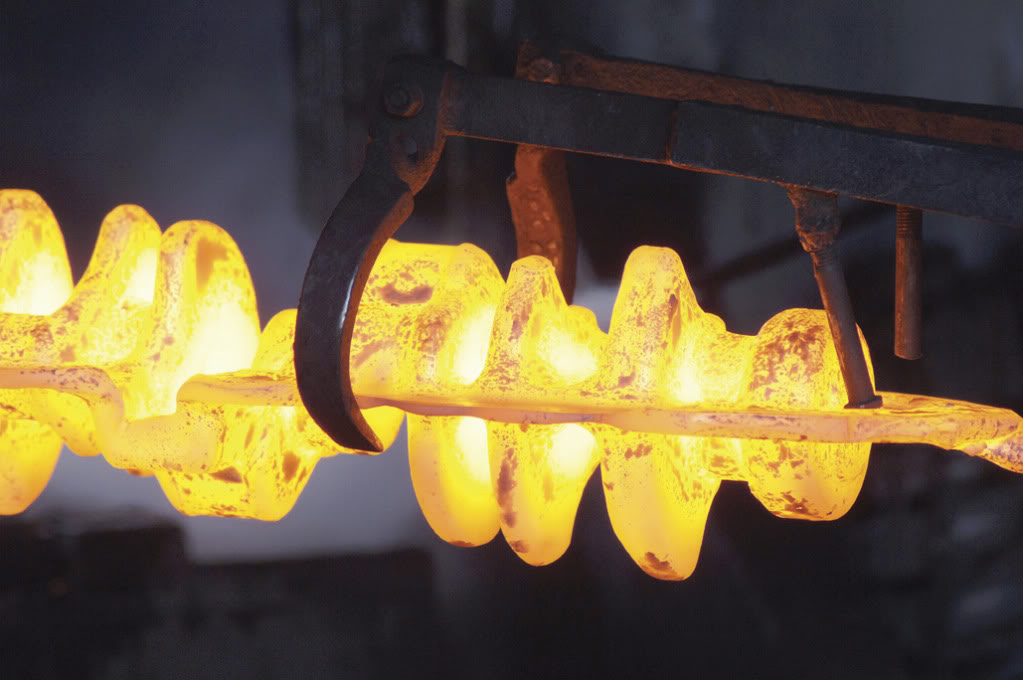
In the past,people think cast iron is used as the material of crankshaft for most engines for its high cost performance.Sometimes,some guys may say that a cast iron crankshaft is no good for engine application,but with the right preparation these crankshafts will endure a lot of abuse.For mild street use or stock rebuilds, all we do at the shop is magniflux and regrind them.If a racer wants to use it for bracket racing or limited oval track use, we will remove all of the casting imperfections on the rod throws to eliminate stress risers (a place for cracks to start). We will also cross drill the oil holes to provide better rod bearing lubrication.One of the most important things that we do to a cast iron crankshaft equipped engine is not done to the crankshaft. It is very important that we use rods and pistons that are as lightweight as possible, so they don’t tear the rod journal off of the crank when it tried to stop them and pull them back down the cylinder at top dead center. With the right prep work and a lightweight rod and piston combination, a cast iron crankshaft should handle 500+ HP with no trouble at all.
Although there is a long history of steel drop forgings in China,closed cooperation between steel forging manufacturer and purchaser is still quite important for delivering high quality steel forgings.Otherwise,it may well produce defects for lack of comminucation.Our suggestions on how to buy steel forgings are as following:
Can the steel forging manufacturer offer design assistance?
Before buyers invest a steel forging into production,it must be designed first based on its application.Of couse,such design must follow steel forging process,otherwise it will be unworkable.When searching a potential from internet,before quoting,buyer should first send original drawing to the engineer of steel forging company.As an experienced and capable forging engineer can give you perfect suggestions on improve components for better application,such suggestions can be how to simplify processing and required machining,thus to help save cost.Of course,the prints should be detailed enough for manufacturing,including material specification(alternative chinese material),toleraneces of main dimensions that may affect assembling,heat treatment requirement,hardness requirement,ect.If the parts are machined,then both forging drawings for forging blanks and machining drawings for finish parts should be offered.Forging blank drawing can be ignored as the engineer will help you to leave machining allowance before laying off billets.If there is any doubt about material,buyer could also ask confirmation of steel forging engineer,so that the finished parts could win great woking performance.
Can the steel forging manufacturer offer design assistance?
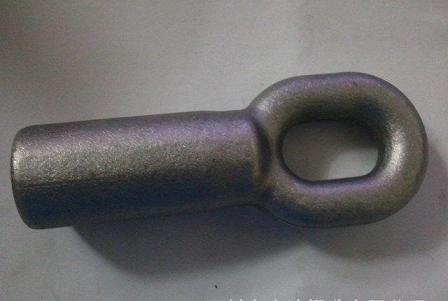
Forging is defined as a metal working process that shape workpiece into desired dimensions by compressive forces applied through the use of dies and tools.Forging process is operated by hammering or pressing the metal.It is one of the oldest known metalworking processes with its origin about some thousands of years ago.At first,forging was complicated by a smith using hammer and anvil.Using hammer and anvil is a crude form of forging.The smithy or forge has been improved to become a facility with engineered processes,production equipment,tooling,raw materials and products to meet the demands of modern industry.
In nowadays,industrial forging is done either with presses or hammers powered by compressed air,electricity,hydraulics or steam.Some examples of products obtained by forging process are-crane hook,connecting rod of an IC engine,spanner,gear blanks,crown wheel,pinion etc.
In nowadays,industrial forging is done either with presses or hammers powered by compressed air,electricity,hydraulics or steam.Some examples of products obtained by forging process are-crane hook,connecting rod of an IC engine,spanner,gear blanks,crown wheel,pinion etc.
In terms of materials,all the forgings are manufactured in steel,aluminum,cooper.From these materials,steel is most common used for its price advantage,easy purchasing and good performance.Following the large demands of steel forgings,more and more steel forgings plants are built,some concentrate on large steel forgings,while some prefer small steel forgings.Even if in China,we could see lots of steel forgings factories.So to compete with other competitors,it is quite important to be a good steel forging manufacturer.As we are professional drop forging company for small steel forging,so today the discussing target is precison steel forgings with closed die forging process.
1)Equipments:Production capabilities will directly decide the development of an enterprise.To produce steel forgings,there are several production lines consists of various forging equipments.It will require lots of money to invest for these equipments,so the investment for equipments is rather important as it will directly show the production capcbilities.Some small steel forging manufacturers choose to buy forging equipments from domestic market for lack of money.But it is not a wise choice in the long term as these equiments will have to be obsoleted after three years' working.However,some large steel forging manufacturers will prefer imported forging equipments from Japan,Korea,German,ect for their superior quality.Such imported forging equipments could be lasting for at least 10 years.
1)Equipments:Production capabilities will directly decide the development of an enterprise.To produce steel forgings,there are several production lines consists of various forging equipments.It will require lots of money to invest for these equipments,so the investment for equipments is rather important as it will directly show the production capcbilities.Some small steel forging manufacturers choose to buy forging equipments from domestic market for lack of money.But it is not a wise choice in the long term as these equiments will have to be obsoleted after three years' working.However,some large steel forging manufacturers will prefer imported forging equipments from Japan,Korea,German,ect for their superior quality.Such imported forging equipments could be lasting for at least 10 years.
Differences between drop forging and press forging
Drop forging is when half of the die is dropped from a height onto the other half of the die,which will contain the hot metal workpiece to be formed. Drop forging is more suitable for mass production.Press forming is instead of dropping half the die onto the other half the two halves are put together and pushed together under a large pressure (up to about 10000 tons) forming the object.the difference is that drop forming leaves the centre of the metal not so hard as the outside,but press forming gives more uniform hardness for larger components.Of course,drop forging and press forging are defined in term of two kinds of forging methods.We could also differ forgings from its temperature,such forgings are named into cold forging,warm forging and hot forging.(See cold forging vs warm forging vs hot forging).
Drop forging is when half of the die is dropped from a height onto the other half of the die,which will contain the hot metal workpiece to be formed. Drop forging is more suitable for mass production.Press forming is instead of dropping half the die onto the other half the two halves are put together and pushed together under a large pressure (up to about 10000 tons) forming the object.the difference is that drop forming leaves the centre of the metal not so hard as the outside,but press forming gives more uniform hardness for larger components.Of course,drop forging and press forging are defined in term of two kinds of forging methods.We could also differ forgings from its temperature,such forgings are named into cold forging,warm forging and hot forging.(See cold forging vs warm forging vs hot forging).
Forging formings of metals according to temperature can be divided into cold deformation (cold forging),warm deformation (warm forging) and thermal deformation (hot forging).The microstructure and mechanical properties influences on forgings of these different forging processes are also different.
1)Cold forging:refers to blanks processed below the recrystallization temperature.
Characteristics of cold forging:high dimensional accuracy,good surface roughness,good working conditions and high production efficiency.So cold forging can replace machining sometimes.Cold forging can make metal reinforcement,improve the strength of parts.So it is applicable to aluminium and plastic parts alloy, copper and alloys,low carbon steel,medium carbon steel,low alloy steel which the deformation resistance is small under room temperature.But when cold plasticity,metal deformation resistance is big,with poor plasticity,and contains accumulation of residual internal stress,needs to continue deformation after intermediate annealing.Nevertheless,the advantages of cold deformation technology makes it is more and more widely used.
1)Cold forging:refers to blanks processed below the recrystallization temperature.
Characteristics of cold forging:high dimensional accuracy,good surface roughness,good working conditions and high production efficiency.So cold forging can replace machining sometimes.Cold forging can make metal reinforcement,improve the strength of parts.So it is applicable to aluminium and plastic parts alloy, copper and alloys,low carbon steel,medium carbon steel,low alloy steel which the deformation resistance is small under room temperature.But when cold plasticity,metal deformation resistance is big,with poor plasticity,and contains accumulation of residual internal stress,needs to continue deformation after intermediate annealing.Nevertheless,the advantages of cold deformation technology makes it is more and more widely used.
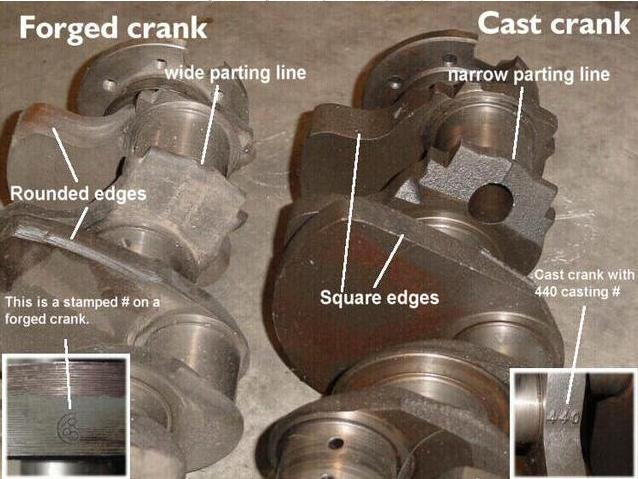
Crank shaft is main rotating parts of engine, is installed on the connecting rod,can undertake the (reciprocating) up and down movement into circulation movement (rotation) of connecting rod. Is an important part on the engine, and its material is made of carbon steel or nodular cast iron, there are two important parts of crankshaft:main journal, connecting rod journal,(and other). Main journal is installed on the cylinder block, connecting rod connected with the big hole, neck connecting rod small hole is connected to the cylinder piston, is a typical slider-crank mechanism. Lubrication of the crankshaft is mainly refers to the lubrication of bearing between the rocker arms and the lubrication of two fixed point.The rotation of the crankshaft is the power source of the engine. Is also the driving force of the whole mechanical system.
Crankshaft fracture is the serious fault of the engine,and fracture usually occurred in the postions of connecting round corners between crank pin,main journal and the crank arm or other stress concentrated sections,like journal oil hole position.
The crankshaft is an important part in automobile engine, it will cooperate with connecting rod and change gas pressure roled in the piston into the rotation of the power,to the transmission mechanism of underpan,drive distribution agencies and other auxiliary devices.
When crankshaft is working,it will be forced under gas pressure,inertia force and inertia moment.Meanwhile,the crankshaft is high speed rotating parts,therefore,requires the crankshaft has enough stiffness and strength, has a good ability to withstand the shock load, good wear resistance and lubrication.
Crankshaft has mainly following two kinds of damage forms in working process:One is fatigue fracture.Will first produce fatigue crack at the position of shaft neck and round corner,then extend to the depths of crankshaft and causing final fracture.Second way is causing serious wear and tear on the surface of the journal(especially in the connecting rod journal).So the crankshaft should have a higher fatigue strength and good wear resistance.
When crankshaft is working,it will be forced under gas pressure,inertia force and inertia moment.Meanwhile,the crankshaft is high speed rotating parts,therefore,requires the crankshaft has enough stiffness and strength, has a good ability to withstand the shock load, good wear resistance and lubrication.
Crankshaft has mainly following two kinds of damage forms in working process:One is fatigue fracture.Will first produce fatigue crack at the position of shaft neck and round corner,then extend to the depths of crankshaft and causing final fracture.Second way is causing serious wear and tear on the surface of the journal(especially in the connecting rod journal).So the crankshaft should have a higher fatigue strength and good wear resistance.
Chinese output of closed die drop forgings is always in the first place in the world.These closed die forgings are manufactured mostly using hot die forging method.And the output of automotive forgings accounts for about 67% of all the closed die drop forgings,so in the production of automotive forgings, closed die drop forging still accounts for absolute proportion.With the rapid increasing of closed die drop forging,the energy consumption is also growing in a fast speed.In recent years,the comprehensive energy consumption of closed die drop forgings has reached more than several million tons coal,and there is large amount of waste gas and dust produced also.So to project environment,we must push on green manufacturing.Below are the solutions available for drop forging manufacturers:
1.Choose green material
Give preference to continuous casting of steel rolling,non quenched and tempered steel.The yield of continuous casting is higher than that of die cast steel,saving 10-15% energy consumption,and save the intermediate reheating energy consumption and reduce the cost.Closed die drop forgings using non quenched and tempered steel saves energy consumption of second heating and high temperature tempering,saving 0.7 KW power per kilogram.
1.Choose green material
Give preference to continuous casting of steel rolling,non quenched and tempered steel.The yield of continuous casting is higher than that of die cast steel,saving 10-15% energy consumption,and save the intermediate reheating energy consumption and reduce the cost.Closed die drop forgings using non quenched and tempered steel saves energy consumption of second heating and high temperature tempering,saving 0.7 KW power per kilogram.
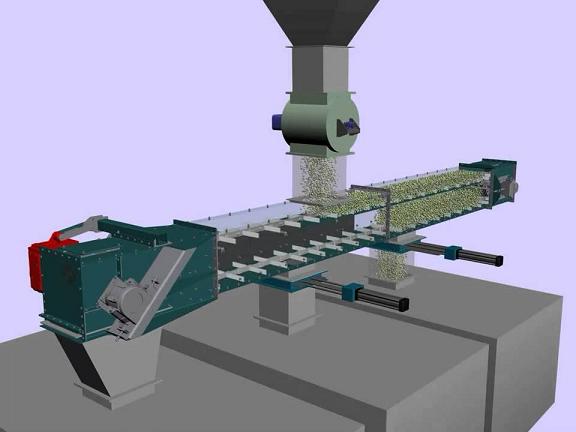
Drop forged conveyor chains are widely used in bulk material handling of products such as grain, coal and ash. Also known as drop forged scraper chains they are typically fitted with flights or special attachments. The chain links themselves are forged from specially selected alloy steel and then precision machined to close tolerances.
When you require continuous flow (en-masse or drag conveying) and the material is being moved slowly within the casing, then a drop forged conveyor chain with attachments matched to the materials being moved will be a good option.