
Drop forging manufacturer

There are a lots of metal forming process for a metal designed part,such as casting,forging,stamping,welding fabrication,ect.Each process has its own characteristics.Sometimes we can use casting or forging either.But by comparison,purchasers will prefer steel forging as the metal forming process.Below we explain in detail why use steel forging as your metal forming process?What are the advantages?
Consistency
The consistency of steel material from one forging to the next,and between separate quantities of forgings is extremely high.Steel forged parts are made through a controlled sequence of production steps rather than random flow of material into the desired shape.Uniformity of composition and structure piece-to-piece,lot-to-lot,assure reproducible response to heat treatment,minimum variation in machinability,and consistent property levels of finished parts.
Consistency
The consistency of steel material from one forging to the next,and between separate quantities of forgings is extremely high.Steel forged parts are made through a controlled sequence of production steps rather than random flow of material into the desired shape.Uniformity of composition and structure piece-to-piece,lot-to-lot,assure reproducible response to heat treatment,minimum variation in machinability,and consistent property levels of finished parts.
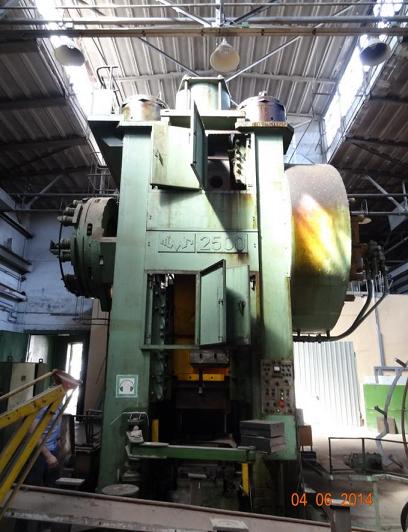
There are mainly three series of hot die forging presses,namely NSP,NMP and NKP.Of course,there are also some auxiliary forging equipments,such as roll forging machine,trimming machine,heating machine,ect.
Characteristics of hot die forging press
Hot die forging presses have advantages of high efficiency,simple operation,convenient maintenance,and suitable for automation forging assembly line.High blow speed,mould thermal contact time is short,and forging dies service life is long.Using upper and lower design will make draft angle decreasing and forging material saving.High resistance to tilt rate, lead to high precision guide rail and high quality steel forgings.PLC control,multiple safety operating circuit system,can ensure the operator safety.Left and right sides of the body is equipped with the work window,so that forgings delivery is convenient.Special card die liberation device,make release of dies rapidly,and the operation is simple.Reliable centralized lubrication system and manually add lubrication system,can effectively reduce the friction loss.Equipped with advanced international tonnage meter,can visual display forging force,and set the overload alarm.
Case:We are a UK based precision machining company for metal components with tight size tolerances for all industries,especially for automotive,construction,forestry,ect.We are now looking for a drop forging company to supply connecting rod blanks only,and we will do machining here locally.
Analysis:This customer contacted us via email and sent us the drawings both in pdf and 3d format.Our sales manager forwarded the drawings to our engineer and marked main information(material,quantity,weight).From the product information we can judge that it is within our production ability.But there is an hardness requirment(45-50HRC),which can only meet by heat treatment.So we are confused if we heat treat forged connecting rod,will it be machinable by our customer?We did talk about this issue with them,and the result is that heat treatment will be done in UK locally after machining.
Analysis:This customer contacted us via email and sent us the drawings both in pdf and 3d format.Our sales manager forwarded the drawings to our engineer and marked main information(material,quantity,weight).From the product information we can judge that it is within our production ability.But there is an hardness requirment(45-50HRC),which can only meet by heat treatment.So we are confused if we heat treat forged connecting rod,will it be machinable by our customer?We did talk about this issue with them,and the result is that heat treatment will be done in UK locally after machining.
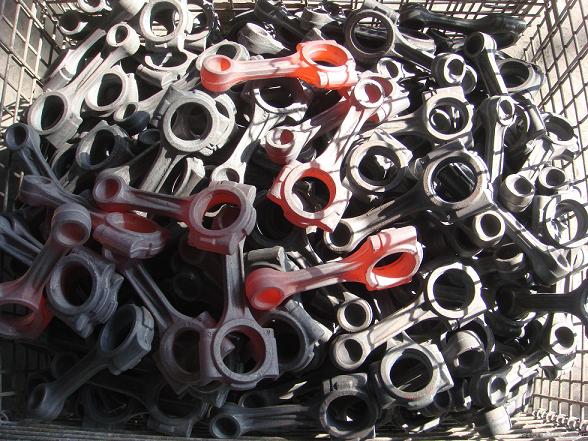
Over the past 50 years,auto parts manufacturing technology is in the continuous improvement.Today,what takes a leading role in the market is the low cost,high strength anf tight tolerance.In drop forging production process,the strict requirements for forgings are just as important as to the requirements of the finished product.Drop forging companies
around the word constantly look for a better production method to achieve the objectives and requirements of the auto parts buyers.
Forged connecting rods are regarded as the quality standards of internal combustion engine to use for decades.Over the years,production methods of connecting rods are constantly changed,includingforging hammer forging,press forging,metal powder forging and casting.In the early years of auto industry development,forging hammer forging is considered to be one of the best forging method.However,in the middle of the twentieth century,due to the higher requirements for quality and tolerance,the forging method must be changed,so manufacturers began to use mechanical press to replace forging hammer.The most effective way to reduce the manufacturing cost is to improve the material utilization.Increasingly stringent requirements for weight and size tolerance promotes the use of powder forging method.Another advantage in addtion to tolerance is that we could forge connecting rod cover toegther with connecting rod,and can open the cover from connecting rod,thus manufacturing cost can be saved.In the late twentieth century, forging method developed into "open" forged steel connecting rods(Why use steel for drop forged connecting rods in automotive cylinder engine?),it is also one of the strengths of the powder forging.The strength of forged steel connecting rod is higher than powder metallurgy rod.Increase as the engine compression ratio,compared with the powder forging connecting rod(wrought vs powder forged connecting rods),high strength of forged steel connecting rod becomes more satisfactory,this forging method can meet the both strict requirements of weight and size tolerance.
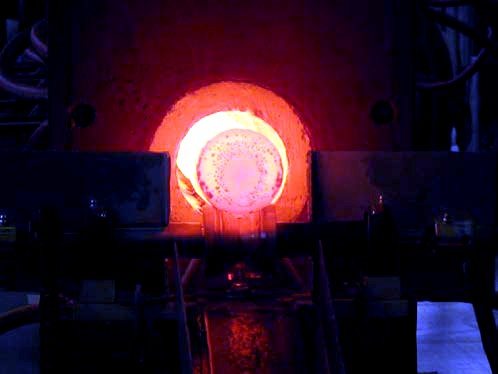
A number of drop forging defects may produce during drop forging process,such defects may be caused by forging dies,heating,forging,heat treatment,ect.Today our topic is focused on drop forging defects caused by improper heating.We can divide the defects into below inspects:1)defects casued by outer organization chemical state change of billets due to medium affects,such as oxidation,decarburization,carburization,sulfurizing,permeability of copper,ect.2)defects caused by change of internal organization structure,like overheating,burnt and not heat through,ect.3)billet crack because of too big internal stress caused by uneven distribution of temperature.

Connecting rod is one of the largest volume production component in automotive cylinder engine.It works as the connection of the piston and the crankshaft and takes charge of transferring power from the piston to the crankshaft and sending it in to transmission.There are different types of materials and production methods used in creating a connecting rod.The major stresses induced in the connecting rod are a combination of axial and bending stresses in operation.Cylinder gas pressure and inertia force will produce axial stress.A whole connecting rod is made up of a long shank,a small end and a big end.When cutting the shank,we can see the cross-section of the shank may be rectangular, circular,tubular,I-section or H-section.Generally circular section is used for low speed engines while I-section is preferred for high speed engines.The most common type of production methods is casting,forging,and powdered metallurgy.Connecting rod must withstand a complex state of loading.It need to undergo high cyclic loads of the order of 10^8 to 10^9 cycles,which range from high compressive loads due to combustion,to high tensile loads due to inertia.Therefore,durability of this component is vital.Due to these factors,automotive connecting rods have been the topic of research for different aspects such as production technology,materials,performance,simulation,fatigue,etc.In modern automotive cylinder engines,the connecting rods are most usually made of forged steel for production engines,but can be made of aluminum (for lightness and the ability to absorb high impact at the expense of durability) or titanium for high performance engines,or of cast iron for motor scooters applications.They are not rigidly fixed at eitherend,so that the angle between the connecting rod and the piston can change as the rod moves up and down and rotates around the crankshaft. The small end attaches to the piston pin, gudgeon pin or wrist pin,which is currently most often press fit into the con rod but can swivel in the piston,a "floating wrist pin" design.The big end of connecting rods will be connected to the bearing journal on the crank throw,running on replaceable bearing shells accessible via the con rod bolts which hold the bearing "cap" onto the big end.
There is no accurate date to source the production time of the first wrought forged connecting rod,but there is a long history of the wrought forged connecting rod to be the “standard” for the automotive industry.Plain carbon steel forgings were the initial material for drop forging design.Since a finished forged connecting rod cannot be formed in one blow,the forging dies for connecting rods have several impressions,each step moves progressively toward the final shape.The metal billet is transferred from one impression to another by successive blows.Figure 1 shows a set of forging dies and the main steps in forging a connecting rod.In general,we can forge the cap part and lower rod part separately,or forged slightly oblong and sawed in two pieces.

Figure 1: Set of forging dies and successive steps for forging a connecting rod roughstock from a metal billet

Figure 1: Set of forging dies and successive steps for forging a connecting rod roughstock from a metal billet

There are different types of forging processes,today our discussing topic is drop forging design.Before drop forging production,the engineering design team will first finalise the geometry,dimension,tolerance and material requirement(normally used material is drop forged steel) for the desired component.This is based on future application of the products,including the intended performance of the part.The typical output is a machine drawing of the final required part;which include post drop forging processings such as machining,tolerance and surface finish requirements.The drop forging drawing of the considered component is shown in Fig.1.1. And a 3D model displaying different views is shown in Fig.1.2.
The first step for a production engineer is to convert the machine drawing into drop forging part drawing.Understanding of the function of actual part in service should be considered as a prerequisite to efficiently deal with this conversion phase.This understanding also helps to improve the decision making ability for the subsequent design stages.The selected component is a part of the universal joint used in propeller shaft for heavy commercial vehicle application.The component is known as “Flanged Yoke” in automotive terminology. It is mostly subjected to torsional loadings;as the whole propeller shaft is designed to efficiently transmit the engine torque to the rear axle.
Closed die forging dies are usually made from low-alloy,pre-hardened steels containing 0.35-0.50% carbon,1.50-5.00% chromium,and additions of nickel,molybdenum,tungsten,and vanadium.It is difficult to heat treat die blocks safely after machining because thermal distortion could destroy or reduce the dimensional accuracy of the cavity.Therefore,die blocks are machined after the desired hardness has been achieved through heat treatment.Die blocks containing shallow or simple cavities can be hardened to Rc 50.However,die blocks with deep cavities,nbs,or com plex design require relatively softer,tougher materials to minimize cracking and die breakage.
When the volume of parts is high and the size of the forging is limited,die inserts can be incorporated in the die block to minimize wear Inserts are generally installed in locations that are prone to excessive wear due to complexity of design and material flow
When the volume of parts is high and the size of the forging is limited,die inserts can be incorporated in the die block to minimize wear Inserts are generally installed in locations that are prone to excessive wear due to complexity of design and material flow
Automotive parts take up a great proportion in closed die forging parts.Application of closed die forging parts,include most of the engineering sectors including automotive.Primary aims of automotive manufacturers is to produce reliable vehicles that can bear load carring at a high speed.At the same time,closed die forgings should be lighter as possible in manufacturing to support fuel economy.Advantages of closed die forging that given by auto manufacturers are below:
- Correct designed closed die forging parts for automotive application,can undertake higher loads and greater stresses than same manufacturing in other methods
- Because close tolerances achieved in basic closed die forging process,further machining processing can be reduced or avoided.Thus,productivity is improved with a overall cost reduction.
- We can achieve weight saving due to less wastage of drop forged steel and the inherent characteristic of higher strength to weight ratio.
- Less machining time will improve lead time for overall manufacturing process.
- Any outer deformation caused by compressive load will ensure good performance in internal structure.
- As billtes are impressed by dies,inside grain flow will improve properties such as strength,ductility,impact resistance,fatigue resistance,ect.
Closed die forging is one of the drop forging processes(another is open die forging),which is mainly for precion small parts using forging technology to achieve better surface finish and performance.In fact,the original name of closed die drop forging is impression die forging,closed die forging is just compared to open die forging.We call this process impression die forging because billets are impressed on the dies to get deformed to create a new part.
In closed die drop forging,two halves of dies are pressed together at a high pressure to shape a metal bar into desired dimensions.This is also a closed process as the dies completely closed together in times to form a part.Most commonly,this form of die forging is used to create 3D metal shapes, such as solid metal parts and other metal pieces that have a solid design and 3D shape. The metals most commonly used with this form of die forging include steel,aluminum,and titanium.
In closed die drop forging,two halves of dies are pressed together at a high pressure to shape a metal bar into desired dimensions.This is also a closed process as the dies completely closed together in times to form a part.Most commonly,this form of die forging is used to create 3D metal shapes, such as solid metal parts and other metal pieces that have a solid design and 3D shape. The metals most commonly used with this form of die forging include steel,aluminum,and titanium.
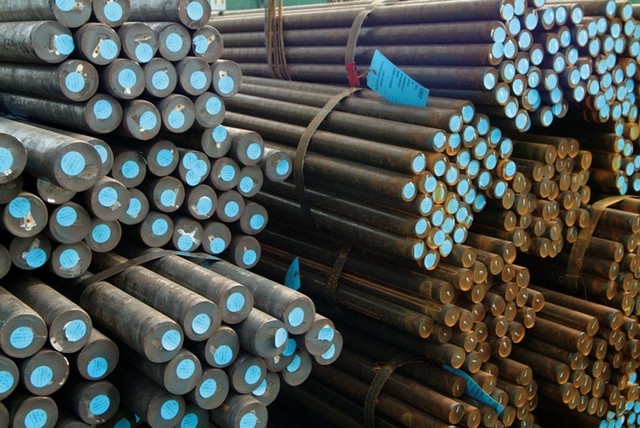