Drop Forging Defects Caused by Improper Heating
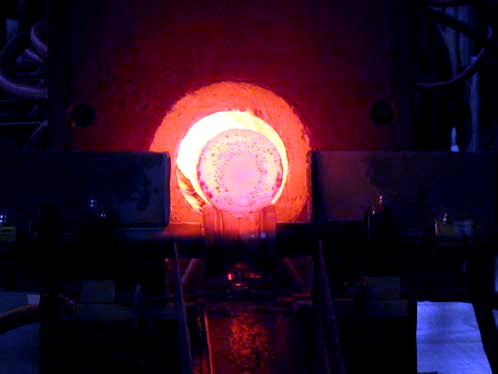
A number of drop forging defects may produce during drop forging process, such defects may be caused by forging dies, heating, forging, heat treatment,ect. Today our topic is focused on drop forging defects caused by improper heating. We can divide the defects into below inspects: 1) defects casued by outer organization chemical state change of billets due to medium affects, such as oxidation, decarburization, carburization, sulfurizing, permeability of copper, ect. 2) defects caused by change of internal organization structure, like overheating, burnt and not heat through,ect. 3) billet crack because of too big internal stress caused by uneven distribution of temperature.
1.Decarburization
Decarburization is refers that carbon of metal surface layer is oxidized at high temperature, makes surface carbon content lower than inside one. The depth of decarburization is associated with compositions of steel, furnace gas composition, temperature and heat preservation time. Easy happening by oxidizing gas heating decarburization, high carbon steel is easy to take off carbon, steel with high silicon content is also decarbonized. Decarburization will decrease the strength, fatigue performance of parts of performance degradation and wear resistance.
2.Recarburization
Forgings after oil furnace heating, often happen carburization phenomenon in the surface or part of surface. Sometimes thickness of carburization layer reaches 1.5-6mm, carburization layer carbon content is about 1% (quality score Number), carbon content of local point is even more than 2% (mass fraction), and appear ledeburite organization. This is mainly in the case of oil furnace heating, when the position of the billet is close to spray oil furnace mouth or in the area of two nozzle cross jet fuel, due to bad mix of the oil and air,therefore, incomplete combustion results in reducibility Carburizing atmosphere on billet surface, thus to produce the effect of surface carburization.Carburization will make forgings machining performance bad, easy to play knife when cutting.
3.Overheating
Overheating is referred that the the heating temperature of metal billet is too high, or stay too long in regulation of forging and heat treatment temperature range, or cause coarse grains phenomenon due to too high temperature.
Carbon steel (hypoeutectoid and hypereutectoid steel) often appears widmanstatten structure after overheating. Martensitic steel after superheating, often appear the intracrystalline texture, Titanium alloy overheating, appear widmanstatten structure. Fracture after alloy steel overheating will appear stone fracture or strip fracture. Overheating organization, due to the coarse grains, will cause decrease of mechanics performance, especially the impact toughness. Generally overheated steel after normal heat treatment (normalizing, quenching), the organization can be improved and performance can also be restored, such overheating is often referred to as unstable overheating; Serious overheating of alloy structural steel by general normalizing (including high temperature normalizing), annealing and quenching after processing, the overheating organization can not completely be eliminated, this overheating is often referred to as stable overheating.
4.Overburning
Overburning refers to metal billet heating temperature is too high or stay a long time in the high temperature heating area, furnace oxidation oxygen and other gas penetrated into the space between the metal grain, and oxidation with iron, sulfur, carbon, formed the fusible oxide eutectic, destroyed the relationship between grain, make the plasticity of material sharply lower. When burnt serious metal, crack at a blow gently,and will appear in the burnt transverse crack when drawing out. There is no strict temperature boundaries of overburning and overheating. Commonly characterized by grain oxidation and melt to determine burnt.
5.Heating crack
In the heating section size of large steel ingot and poor thermal conductivity of high alloy steel and high temperature alloy blank, if the heating speed is too fast in low temperature stage, the billet will produce large thermal stress due to internal and external temperature difference. Combined with blank at this time due to the low temperature and poor plasticity, if jorge stress value is more than the strength of the billet limit, will produce heating crack radiating from the center to around,then split the whole section.
6.Copper brittleness
Copper brittleness on forging surface is cracked. Observed at high magnification, there is pale yellow copper (or copper solid solution) along the grain boundary.