How to Select Materials for Forged Crankshafts?
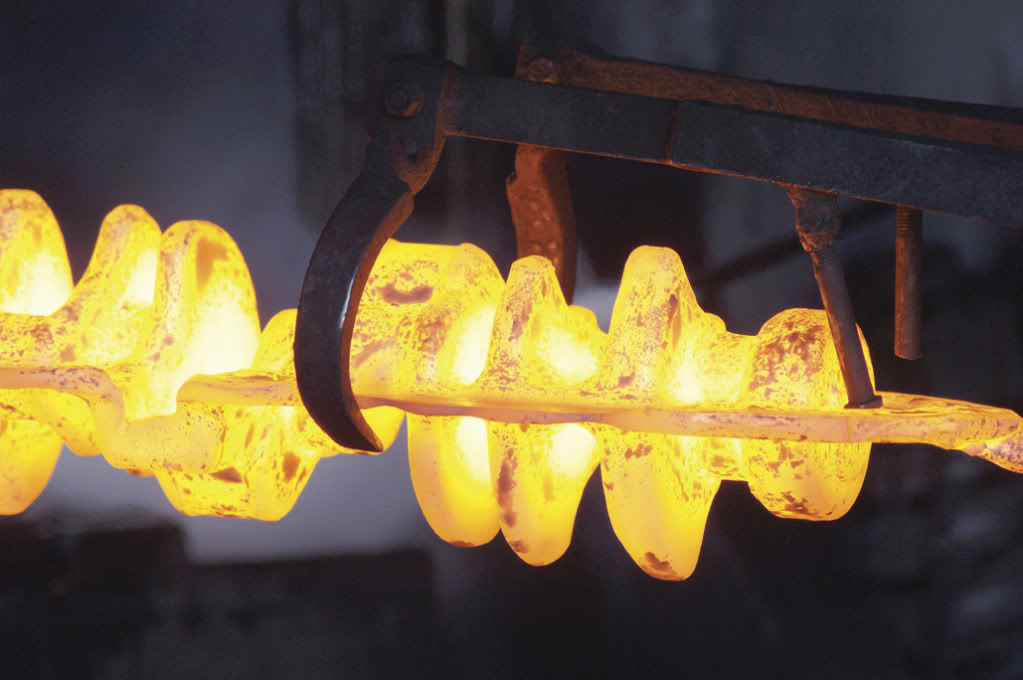
In the past, people think cast iron is used as the material of crankshaft for most engines for its high cost performance. Sometimes, some guys may say that a cast iron crankshaft is no good for engine application, but with the right preparation these crankshafts will endure a lot of abuse. For mild street use or stock rebuilds, all we do at the shop is magniflux and regrind them. If a racer wants to use it for bracket racing or limited oval track use, we will remove all of the casting imperfections on the rod throws to eliminate stress risers (a place for cracks to start). We will also cross drill the oil holes to provide better rod bearing lubrication. One of the most important things that we do to a cast iron crankshaft equipped engine is not done to the crankshaft. It is very important that we use rods and pistons that are as lightweight as possible, so they don’t tear the rod journal off of the crank when it tried to stop them and pull them back down the cylinder at top dead center. With the right prep work and a lightweight rod and piston combination, a cast iron crankshaft should handle 500+ HP with no trouble at all.
Next, on the crankshaft ladder is a forged steel crankshaft (cast vs forged crankshaft). If one was made for your engine, the most common steel used is 1038. This is pretty much just plain old clean steel with some carbon added for heat treating purposes. A forged steel crankshaft is usually a good choice for its low cost and high strength, especially when purchased used. These forged crankshafts will hold up in more demanding applications than cast crankshafts, but still need some prep work before being used in engine applications. Again, the first thing we do is magniflux it to make sure we don’t spend time and money on a cracked crankshaft. Also, we remove the stress risers from the rod throws and cross drill the oil holes. Another option, especially attractive to circle track racers, is to drill the rod throws parallel to the crank axis with a ¾ or 7/8 hole. This makes the rod journal hollow and much lighter, with only a minimal loss in strength and it can be done for under $100.
Finally, having forged crankshaft shot peened before having it reground. This also stress relieves the steel and makes a more stable crankshaft. A forged crankshaft prepared in this way will survive in all but the most demanding racing environments. A racer can choose what degree of crankshaft preparation best suits their application and budget.
At the top of the ladder are the aftermarket forged and billet steel crankshafts. There are many different manufacturers and price ranges. So how does the racer determine which way to go? First, I’ll cover the most common materials available. There’s 4130 and 4340–these numbers pop up all the time in crankshaft ads, but do we know what they mean? I’ll try to give a quick explanation. The last two numbers tell us how many 100ths of a percent of carbon is in the material. Carbon adds to the harden ability of the steel. 4130 will have 30% of carbon and 4340 will have 40% and so on. Both 4130 and 4340 start with a #4, this tells us that the steel is alloyed with molybdenum,or moly. This adds toughness to the steel. More moly means a tougher crankshaft. 4130 has 20% moly, while 4340 has 25%. In addition to more carbon and more moly, the 4340 is also alloyed with nickel, this is noted by the second number in the alloy. A “3” nickel assures deep and uniform hardness in the crankshaft.
Obviously, 4340 is the better selection, but by comparison, it will cost more. If you’ve reached the degree of performance that requires an aftermarket crankshaft, I can’t see buying one of mediocre quality. Save your money and buy the top quality stuff from drop forging manufacturer, you’ll be happier in the long run for technic support and lower cost. Another thing you should consider on a forged crankshaft purchase is how much it weighs. The lighter the crankshaft the more it will cost. Most company’s start with the same forging for their standard and lightweight crankshafts, so if you’re on a budget and can sacrifice the weight, the standard crankshaft is the way to go (as the strength and durability will be the same).
Well, I hope this will help you spend your crankshaft dollars more wisely. Until next time, keep your right foot down. Our design guide of forged crankshaft could also help you in understanding this theme. If you have still have any questions about the material of forged crankshafts, pls contact us.