
Drop forging manufacturer

Forging is a metal processing process that using forging pressure machines to put pressure on metal blank,which will produce plastic deformation in order to obtain certain mechanical properties,a certain shape and dimensions.Forging can eliminate the as-cast loose defects that produced on metal smelting process,optimizing the microstructure,and meanwhile can preserve intact metal flow.So mechanical properties of forgings generally are better than that of the same material castings.
As one of the main metal processing process,applications of forgings are so wide.Such forgings are mostly used by people when safety factor is considered and good mechanical properties are needed.So forgings can be used in mining machinery(mining drill bits),agricultural machinery(agricultural wear parts),forestry machinery(mulcher hammer/teeth),automotive industry,trailer parts,ect.Click our photo gallery page can help you to learn more about forging applications.
As one of the main metal processing process,applications of forgings are so wide.Such forgings are mostly used by people when safety factor is considered and good mechanical properties are needed.So forgings can be used in mining machinery(mining drill bits),agricultural machinery(agricultural wear parts),forestry machinery(mulcher hammer/teeth),automotive industry,trailer parts,ect.Click our photo gallery page can help you to learn more about forging applications.
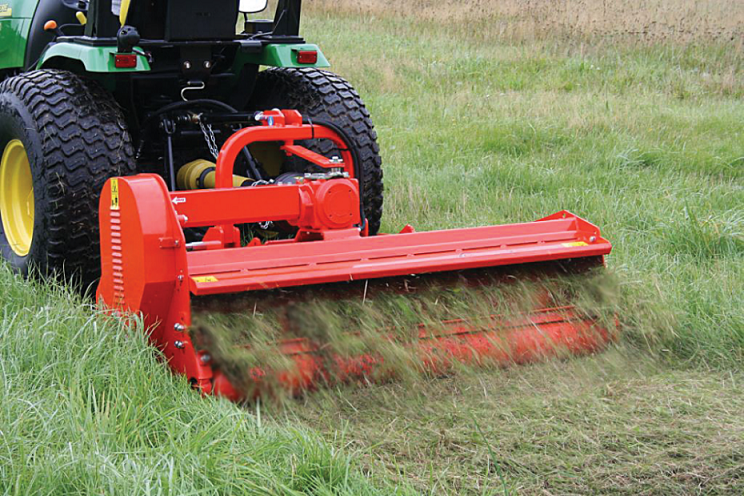
Flail mowers may also be used in a more or less upright position for trimming the sides of hedges. They are often called hedge cutters (or sometimes also hedge trimmers) then. Especially in forestry (agroforestry) some very robust variants of flail mowers – called flail mulchers, flail shredders, or flail choppers – are used.
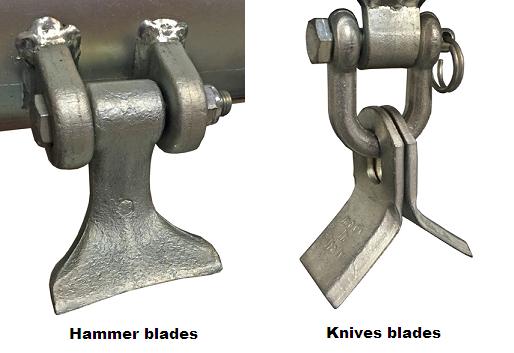
When you design o buy a new flail mower, you will have a choice of the Y Knife Blades or Hammer Blades. The Y-Blades are great when cutting tall weeds and overgrowth and can also offer a nice cut to your lawn. However,if you are need to cut tree saplings and dense overgrowth,the flail hammer blades are used,which are wider, heavier blades than the Y-blades. No matter Flail hammer blades or Y knife blades,either set of blades will make a perfect solution for cutting.
In forging industry, there are some professional terms which are defined to describe the forging process or operations.Below we picked out some common terms when used in closed die forging process.
1) Forging die: It may be referred to a complete tool consists of a pair of mating members for producing work by hammer or press.A pair of forging dies consists of upper and lower die halves with cavities.
2) Billet: A slug cut from rod ready to be heated and forged.
3) Blocker: Preform die or impression, used when part cannot be made in a single operation.
1) Forging die: It may be referred to a complete tool consists of a pair of mating members for producing work by hammer or press.A pair of forging dies consists of upper and lower die halves with cavities.
2) Billet: A slug cut from rod ready to be heated and forged.
3) Blocker: Preform die or impression, used when part cannot be made in a single operation.
When purchasers need a metal forming process for their precision design or products,they may have lots of considerations,such as quality,economy,ect.With the development of modern industry,there are all kinds of metalworking processes for choosing,such as casting,forging,powder metallurgy,stamping,machining,ect.Each metalworking process offers a unique set of costs,advantages and capabilities.When safty and strength factors are required,closed die forging process will be your best choice.In fact,closed die forging is often the optimum process,in terms of both part quality and cost-efficiency-especially for applications that require maximum part strength,special sizes or critical performance specifications.
In fact,in terms of forging,there are also several kinds of forging processes available,such as open die forging,closed die forging,cold forging,and extrusion.However,here we will discuss the methods,application and bennefits of closed die forging process.We suggest you to consider this process when selecting the optimum process for your metal parts production.
In fact,in terms of forging,there are also several kinds of forging processes available,such as open die forging,closed die forging,cold forging,and extrusion.However,here we will discuss the methods,application and bennefits of closed die forging process.We suggest you to consider this process when selecting the optimum process for your metal parts production.
Closed die forging is commonly used in nowadays for many improtant metal components. On one hand, is that it can product metal products with good properties. On the other hand, the price of closed die forging is also competitive than casting. In other words, closed die forging also has economic advantages.
Material
Before forging, we will first need to cut the equal billet according to the size of products. Normally, the waste of material after forging is the flash. So comparing with casting or machining, closed die forging requires less material, thus material cost will be saved. Take a round ring for example, we can make it by forging or machining. If machining, the all corner and the center material will be wasted. But with forging,we can forged to the sizes with minimum waste.
Material
Before forging, we will first need to cut the equal billet according to the size of products. Normally, the waste of material after forging is the flash. So comparing with casting or machining, closed die forging requires less material, thus material cost will be saved. Take a round ring for example, we can make it by forging or machining. If machining, the all corner and the center material will be wasted. But with forging,we can forged to the sizes with minimum waste.
To remove the stress and improve mechanical properties of drop forging, heat treatment will be done after forging. Such heat treatment can be normalization, tempering, quenching, temperting&hardening,ect.To test the heat treatment result,we may test the tensile strength,yield stength,enlongation,hardness,among these mechanical properties,hardness test is usually used for drop forging.Today,we will introduce common hardness testing methods for closed die drop forging.
Both briness hardness and rockwell hardness are all the testing standard for drop forging hardness.Although the testing methods of them are not the same.But either of them can be adapted to see the hardness result of drop forging products.To ensure correct testing result,for one drop forging product,we should testing the hardness in different sections and check if heat treatment of drop forging is done in a good way.
Both briness hardness and rockwell hardness are all the testing standard for drop forging hardness.Although the testing methods of them are not the same.But either of them can be adapted to see the hardness result of drop forging products.To ensure correct testing result,for one drop forging product,we should testing the hardness in different sections and check if heat treatment of drop forging is done in a good way.
Although the cost of drop forging dies may be relatively high,for piece price, it is very cost-effective. With drop forging process, the metal products can not only be in a low cost, but also win tough and durable characteristics. So that is why people say drop forging has low recurring cost and is the most beneficial production method for long runs. Of course, small quantities can be also offered, but more economocal with increased volume. Compared to cast or machined process, drop forging can produce metal products with a high strength-to-weight ratio. Also, it has less chance of flaws and low injection rate.
So,when you are interested in sourcing for drop forging supplier. CFS Forge can be your one stop shop. Our quick turnaround times and impressed services are the best in drop forging industry.
So,when you are interested in sourcing for drop forging supplier. CFS Forge can be your one stop shop. Our quick turnaround times and impressed services are the best in drop forging industry.
Steel forging is a metal forming process of shaping metals using the compressive force.The steel forging process is a bifurcated depending on the temperature at which it is preformed.Steel forging helps in shaping of the molten metal onto desired shape and size.It is one of the essiontial techniques in industry that are majorly reliant on machineries.Steel forging has gone simpler with the time.Main classifications of steel forging are carbon steel forging,alloy steel forging,stainless steel forging.
The traditional ways of steel forging lacks in various aspects.From being low on durability to prone to corrosion,there are numerous drawbacks.Metal enforced with steel can go a long way in terms of durability and evading corrsion.Closed die forgings for precison components are high on tensile strength.The imposed metals are used in the forging process of disc and sleeves that make cost conscious and quality product.
The traditional ways of steel forging lacks in various aspects.From being low on durability to prone to corrosion,there are numerous drawbacks.Metal enforced with steel can go a long way in terms of durability and evading corrsion.Closed die forgings for precison components are high on tensile strength.The imposed metals are used in the forging process of disc and sleeves that make cost conscious and quality product.
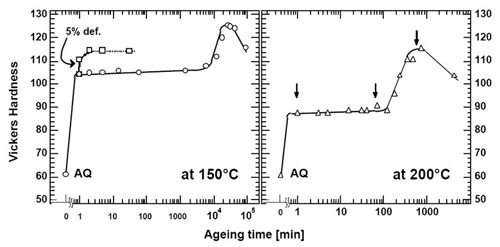
Age hardening,also called precipitation hardening,is a type of heat treatment commonly used for steel forging.Its name comes from the point in the hardening process in which the steel forging is aged,can be heated for an extended of time or keep it stored at a lower temperature for an extended period before use to form precipitates.This treatment is used on malleable alloys,such as steel for closed die forging.
Age hardening process will prevent the plastic deformation of steel forging parts.Thus,to increase the strength and other properties of products,but plastic deformation and toughness is low.Alloys created by the age hardening process have many uses,especially in applications where high strength and good performance at high temperatures are needed.If you need to make your parts in steel forged with age hardening treatment,also pls contact us.
One of the most popular forms of forged metal is steel forged. Forged steel is an often used metal for forging because it is a very sturdy steel that can withstand the high heat that is required by the forging machine to make the metal malleable enough to shape. The metal is warmed to a high degree of heat because when you drop forge metals the metal is placed in the machine and a hammer press slams down onto the metal, forcing it against the die. The heated malleability of the metal combined with the force of the hammer shoving the metal against the die usually makes shaping forged steel relatively easy. Because of this ease of shaping the sheets of metal can be processed into their required shapes pretty quickly.
Thus,we can see steel forged products will no matter give you a price advantage,but also the properties are also quite reliable. As a steel forged manufacturer in China, we can make all kinds of different steel forgings as you need. Just contact us right now for your steel forged parts, we will advise in a most cost-effective way for your products.
Thus,we can see steel forged products will no matter give you a price advantage,but also the properties are also quite reliable. As a steel forged manufacturer in China, we can make all kinds of different steel forgings as you need. Just contact us right now for your steel forged parts, we will advise in a most cost-effective way for your products.
Now there are 7 production lines of closed die drop forging in our factory with forging presses ranging from 300t to 2500t.All these forging presses can be used to forge products in different dimensions.From the point of most people's view,the tooling cost of drop forging is higher than casting tooling.It is without doubt that forging cost more due to its nature and advantages.But in spite of this,you get what you pay,it is rewarding.Our production capabilities are not limited to drop forging,but also machining is also one of our advantages.To serve our customers better,we are also equiped with some machining equipments from drilling machine to CNC,so that machining can be done in our company.
Besides,our in-house heat treatment will also help us to offer you our competitive prices.So comparing with other forging factories and trading compaines,we are always your top and wide choice for drop forging products.Any interest in such process,just pls contact us!
Besides,our in-house heat treatment will also help us to offer you our competitive prices.So comparing with other forging factories and trading compaines,we are always your top and wide choice for drop forging products.Any interest in such process,just pls contact us!