
Drop forging manufacturer

Price is the major factor that most American and Eourpean compaines source precision forgings in China. Especially for those precision forging distributors, they has a district control on the cost of finished precision forging parts. As a leading precision forging company in China, we would like to talk about how to source precision forgings in China. This article will guide our customers to source more prefessional precision forging manufacturers, and avoid any loss during the whole purchasing process.
In conclusion, cooperating with a good precision forging supplier is very important for your project. Any wrong decision will cause both time and money time. We, CFS Forge, are the specialized precision forging manufacturer for more than 30 years. Thanks to our high quality, competitive prices and good service, we always win good reputation from our customers. If you are now in the status of sourcing precision forgings from China, pls feel free to contact us.
In conclusion, cooperating with a good precision forging supplier is very important for your project. Any wrong decision will cause both time and money time. We, CFS Forge, are the specialized precision forging manufacturer for more than 30 years. Thanks to our high quality, competitive prices and good service, we always win good reputation from our customers. If you are now in the status of sourcing precision forgings from China, pls feel free to contact us.
Precision Forging is a process where metal is preheated and pressed into desires shapes with forging equipments in different tons. Precision Casting is the metal forming process by puring metal liquid into shell mold, cut the products from the tree assembling after cooling, and remove excess material for final product by polishing.
After forging, the inner grain structure is refined. So precision forging process creates products with better strength than those manufactured by any other metalworking process. Forging takes advantage of the metal’s natural grain flow, shaping the grain flow to conform to the contours of each part’s unique geometry. This grain flow contouring is called flash, and it will be removed by trimming dies. So normally, precision forged parts will require at least two pairs of moulds. Precision Forging can provide net shape products, which reduces further machining job and thus, machining cost can be saved.
After forging, the inner grain structure is refined. So precision forging process creates products with better strength than those manufactured by any other metalworking process. Forging takes advantage of the metal’s natural grain flow, shaping the grain flow to conform to the contours of each part’s unique geometry. This grain flow contouring is called flash, and it will be removed by trimming dies. So normally, precision forged parts will require at least two pairs of moulds. Precision Forging can provide net shape products, which reduces further machining job and thus, machining cost can be saved.
In order to achieve high surface hardness and surface roughness, improve fatigue strength, and meet working performance of drop forgings, Mechanical processing will be operated after carburizing treatment. The mechanical processing after carburizing treatment is generally as follows:
1) Machining
The surface carbon content after carburizing is high, and after heat treatment, the surface of drop forged blanks will exsit a large amount of residual austenite, easy to form grinding cracks, such as burns and crack, in the process of grinding. Besides, grinding crack can also produce if there is thick carbide, carbide network or carbide film. So in the process of Mechanical Processing, we should refer to the technical requirements of carburizing forgings, choose the correct process parameters according to the specific characteristics. This will help improve the quality of the drop forgings, and can guide the actual machining.
1) Machining
The surface carbon content after carburizing is high, and after heat treatment, the surface of drop forged blanks will exsit a large amount of residual austenite, easy to form grinding cracks, such as burns and crack, in the process of grinding. Besides, grinding crack can also produce if there is thick carbide, carbide network or carbide film. So in the process of Mechanical Processing, we should refer to the technical requirements of carburizing forgings, choose the correct process parameters according to the specific characteristics. This will help improve the quality of the drop forgings, and can guide the actual machining.
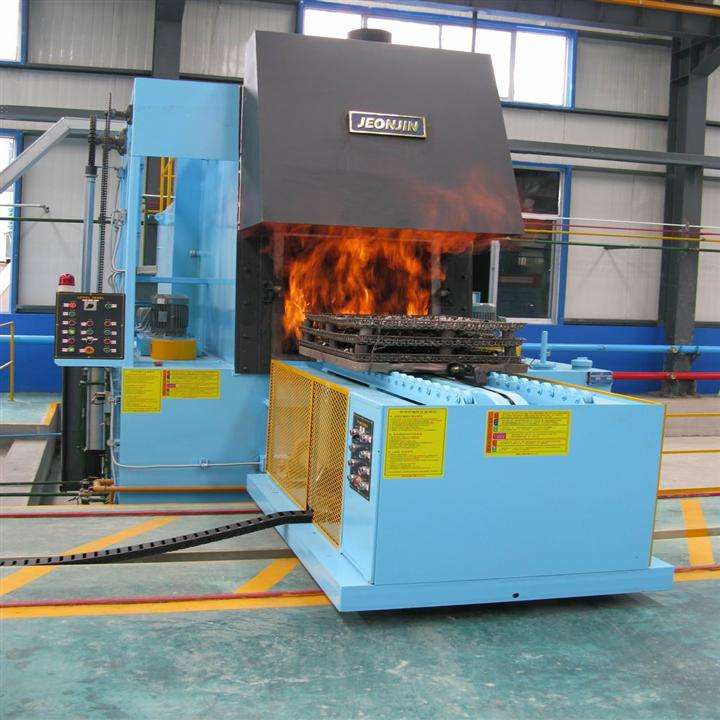
Materials of drop forgings that require carbuzing treatment are commonly selected as low carbon steel or low alloy steel (carbon content less than 0.25%). To maximum the working performance of carburizing treatment, drop forgings need to be quenched after carburizing treatment. Normally, the depth of carburizing treatment is 0.8-2mm. After carburizing, the surface hardness of drop forgings can reach HRC58-63, and the inner hardness can be HRC30~42. In addition, After carburizing, the surface of drop forgings will compress the internal stress, which will be beneficial to improve the fatigue strength of products. Therefore, carburizing is widely used in drop forging to impreve the strength, impact toughness and wear resistance, thus to longer the working life of forgings.
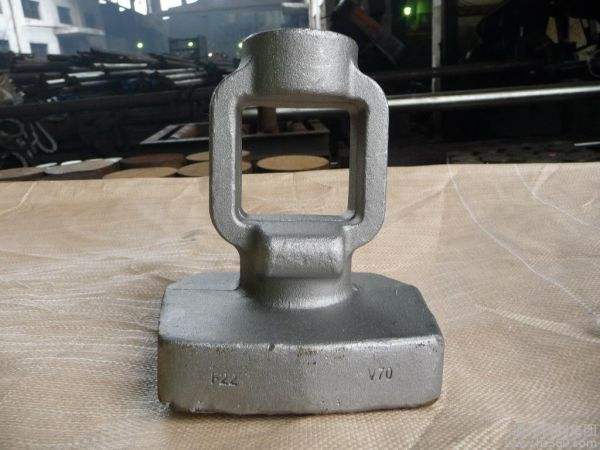
Another benefit of forgings is the directional flow lines structure. Due to quality concerns brought about by low cost country valve manufacturing we now often see customers first specify a forging rather than a casting, then specify it must be a European forging and an approved brand, yet they then still ask for 100% MPI and UT on common A105 valves increasing the cost exponentially. Using good quality forging can reduce the need for NDT. Of course UT and MPI is a good idea to provide reassurance of the quality, especially for castings in larger sizes and higher classes.
As a global supplier for forged steel components,our customers have long benefited from the high performance value of forged rubber track metal cores.We are alway striving for excellece in delivering innovation,value and quality.Below is the a complete manufacturing process showing how our forged rubber track metal core is made:
Step 1-Like other drop forged products,rubber track metal core is also produced by closed die forging process.So developping forging dies is the first step for manufacturing.Normally afte designing the forging dies according to the dimensions of products,it will be precision machined by CNC,which consists of upper and lower dies.
Step 1-Like other drop forged products,rubber track metal core is also produced by closed die forging process.So developping forging dies is the first step for manufacturing.Normally afte designing the forging dies according to the dimensions of products,it will be precision machined by CNC,which consists of upper and lower dies.
In the past 15 years,due to our continuous hard working and improvement of our drop forging process, we are now supplying our customers custom forgings in below two forging methods:
1) Closed die forging: Closed die forging is the most conventional custom forging process for metal parts. It is more suitable for parts with simple shape, less budget, wide tolerance requirement.
2)Precision forging: Precision forging is an improved forging solution for small parts after closed die forging process. Compared with traditional forging process,precision forging can forge parts with more complex shapes, also it is flashless, which can save materials. But in total, the cost of precision forging is higher for its high tooling cost and operation cost.
1) Closed die forging: Closed die forging is the most conventional custom forging process for metal parts. It is more suitable for parts with simple shape, less budget, wide tolerance requirement.
2)Precision forging: Precision forging is an improved forging solution for small parts after closed die forging process. Compared with traditional forging process,precision forging can forge parts with more complex shapes, also it is flashless, which can save materials. But in total, the cost of precision forging is higher for its high tooling cost and operation cost.
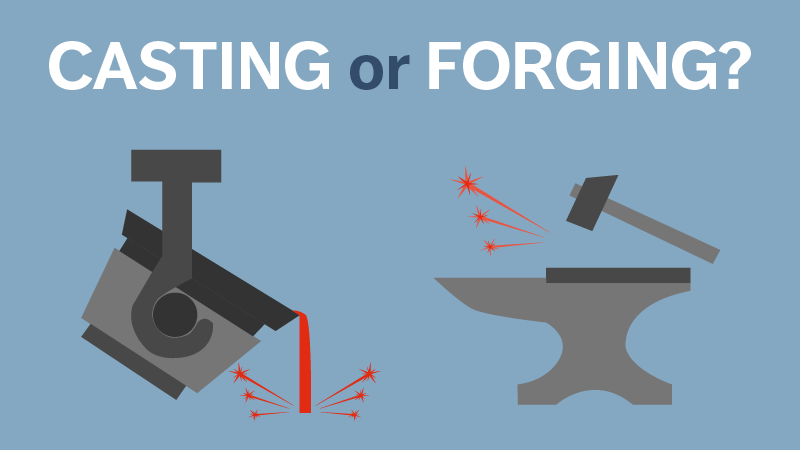
Today steel forging and steel casting have been the two main production processes for steel parts.Compare to steel casting,there are a lot of advantages to use steel forging as the metal forming process.
When pressing the heated steel billet between forging dies, steel will fill the die cavity and the redundant steel will be around the shape of product, which is called flash. So the waste of whole forging process is the flash. That is why steel forging is a net or near net shape process compare to steel casting. Also, although the cost of forging dies are higher than that of casting molds, but the unit cost of steel forging is much lower than steel casting. So in terms of cost, when the quantity is large, steel forging is more cost-effective.
When you finish the design for a metal part,you can choose both casting and forging for it(see differences between forging and casting).But if you would like to customize it in a large quantity,low cost,close tolerance,high strength and short lead time,closed die forging technology is the best choice for you.
Closed die forging can be made in different metals,such as forged steel,aluminum,brass,ect.The select of material will mainy depond on the application of its industry.At Fly Forge,we can take any design and metal into production with our advanced closed die forging process.And forged steel is the most common used material by our customer for its special characristics.
Closed die forging can be made in different metals,such as forged steel,aluminum,brass,ect.The select of material will mainy depond on the application of its industry.At Fly Forge,we can take any design and metal into production with our advanced closed die forging process.And forged steel is the most common used material by our customer for its special characristics.
Forging dies manufacturing is the first step to start a forging part. We all know that forging can be generally classified into two types, open die forging and closed die forging. Open die forging is operated between flat dies or dies in a simple shape. This process is mainly used for large parts. In closed die forging, metal billet is deformed in upper and lower dies for desired shape and dimensions. Deformation occurs in the closed cavity under high pressures, which will achieve precision forgings with tight tolerances. So this process is widely used for the manufacture of simple as well as complex high strength precision parts,especially when safety factor is considered. As a closed die drop forging manufacturer, we would like to introduce the forging dies manufacturing for closed die forging parts in detail.
Before manufacturing of forging dies, we can not start the production process directly. Firstly, engineer need to know how to design the forging dies following the drawing of a new forging part. Design of forgings dies depends on the processing steps, nature of workpiece material, flow stress, working temperature, etc. All these factors need to be considered. Generally speaking, we need to calculate the volume of billet accurately to aviod under filling or excess filling. And selection of parting line(referring the lind where two dies meet) is also important. Sometimes for a forging part, there are several options to choose a parting line. And the best one is that the parting line can ensure the flow of material will be uniformly divided. In other words, forging is not feasible if there is no way to decide parting line, in this case, casting can be considered.
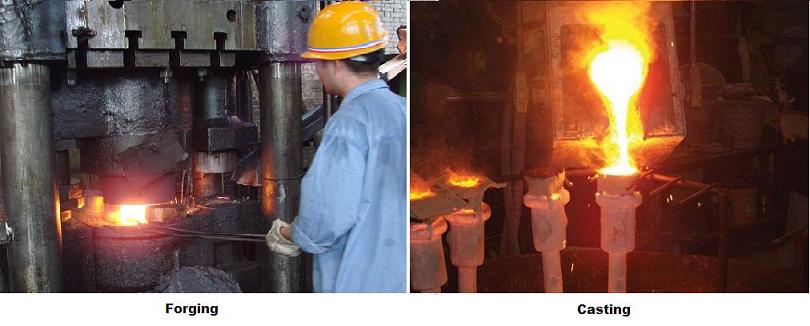
Forging is processing way that putting pressure on metal blank by forging machinery, making it produce plastic deformation, in order to obtain certain mechanical properties, a certain shape and size of forgings. Forging can eliminate the as-cast osteoporosis of the metal, welded holes, and generally mechanical properties of forging is better than that of the same material of the casting.So for those important components that require to undertake high mechanical load, or working in serious conditions, in addition to simple shape rolling plate, or welding parts are available, all will consider forging process.
Casting is a metal forming process that melting the metal into certain requirements of the liquid and then pouring it into the mold,after cooling solidification,we can get desired shape and sizes.Production cost of blanks produced by casting is low.For complex shape, especially the parts with complex inner cavity, casting can show its economical efficiency more; At the same time, it has a wide adaptability,and has better comprehensive mechanical properties. But materials that needed in casting production and equipments (such as metallurgical furnace,sand mixing machine,molding machine, core making machine, shakeout machine, shot blasting machine, etc.) will produce dust, harmful gas and noise.Thus it will do harm to environmental.
Casting is the oldest metal processing process that first melting metals into liquid status, then pouring metal liquid in injection moulds, and cooling a while to obtain the required shape or dimensions. When products are not suitable for forging, casting is the economic method for blank shape. Especially for complex shape parts, casting can show its efficiency more.
Size and weight range of casting parts is very wide, almost unlimited metal species; Parts that have general mechanical properties, but also has comprehensive performance like wear-resisting, corrosion resistance, shock absorption, which is better than other metal forming methods, such as forging, rolling, welding, punching, etc. So metal blanks produced by the method of casting process are still the most on the quantity and tonnage so far.
Size and weight range of casting parts is very wide, almost unlimited metal species; Parts that have general mechanical properties, but also has comprehensive performance like wear-resisting, corrosion resistance, shock absorption, which is better than other metal forming methods, such as forging, rolling, welding, punching, etc. So metal blanks produced by the method of casting process are still the most on the quantity and tonnage so far.