
Drop forging manufacturer

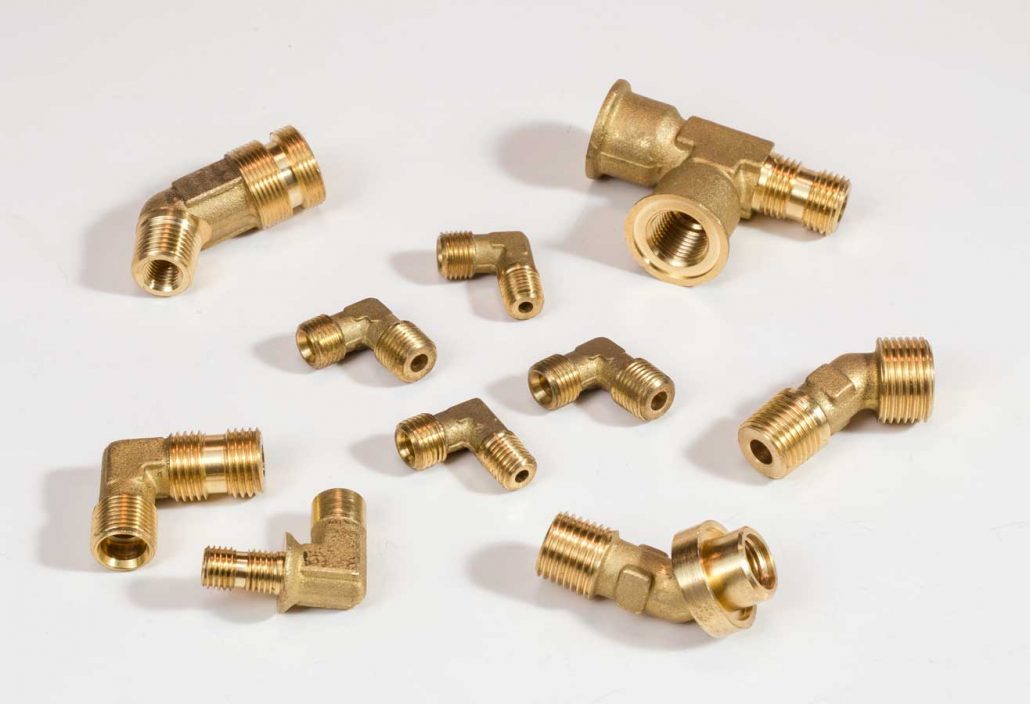
Among all the metalworking processes, forging is the most ideal method to produce Brass Valve, Pipe or Plumbing Fittings. Several advantages are given with forging, for example, by forging, the brass material will be pressed and the grain struction will be improved, which will make the strength of Valve, Pipe or Plumbing Fittings much better. Besides, due to the large demands of Valve, Pipe or Plumbing Fittings, the order quantity is large. The production efficiency of forging is much higher than casting, which will shorten the lead time under the basis of high quality. Next, precision forging can give a close tolerance, which can reduce further machining and save cost. Lastly, the forging cost is also lower than casting in the long term. So, forging is always preferred by our customers.
However, forging is not omnipotent, it has limitation on the shape of Brass Valve, Pipe or Plumbing Fittings. And for some areas with close tolerances or threaded holes, extra machining is required. Machining is a processing process that will remove the excess brass materia of Brass Valve, Pipe or Plumbing Fittings. When there is a high requirement on surface finish (such as Ra3.2 or Ra1.6), or closer tolerance that far from general forging tolerance, or thread holes, we can only meet by machining. CFS Forge has full set of machining equipments in house. With skilled machining capacility, our customers can enjoy shorter lead time and less production cost. Of course, besides forging & machining, we can also supply various surface treatment requirements, such as shot blasting, sand blasting, electroplating, polishing, ect.
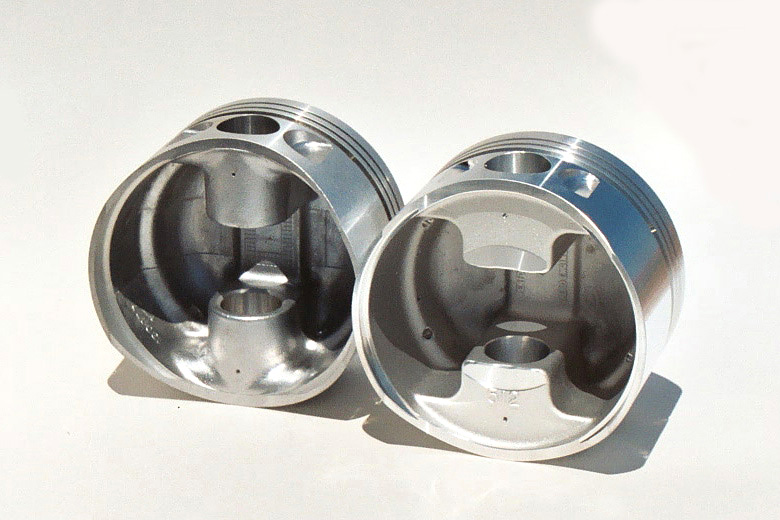
Aluminum casting is a simple, inexpensive and versatile way of forming aluminum into a wide array of products. There are several methods of aluminum castings, including die casting, gravity casting and sand casting. Common aluminum casting alloys include: A356, A380, ect.
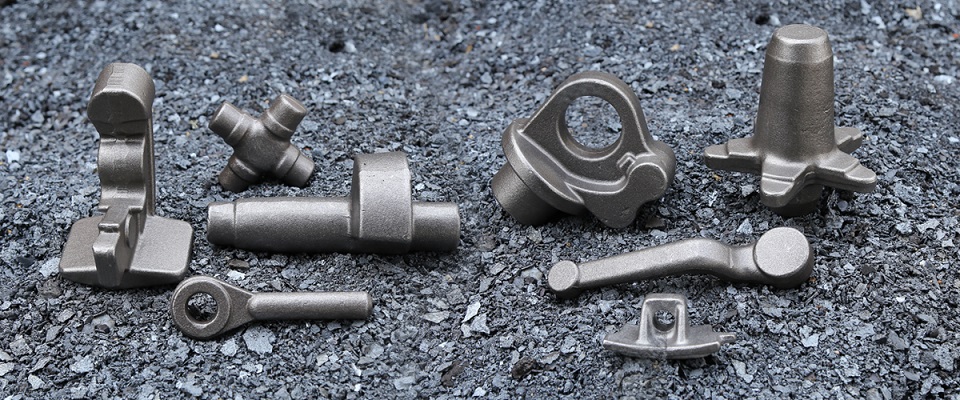
Production costs for drop forgings are changable due to varify on many factors. Currently in China, the prices for producing drop forgings are keeping increasing. Such inceasing can be caused by several factors, such as raw material costs, labour costs, etc. Below are the factors that cause the prices of drop forgings increasing briefly.
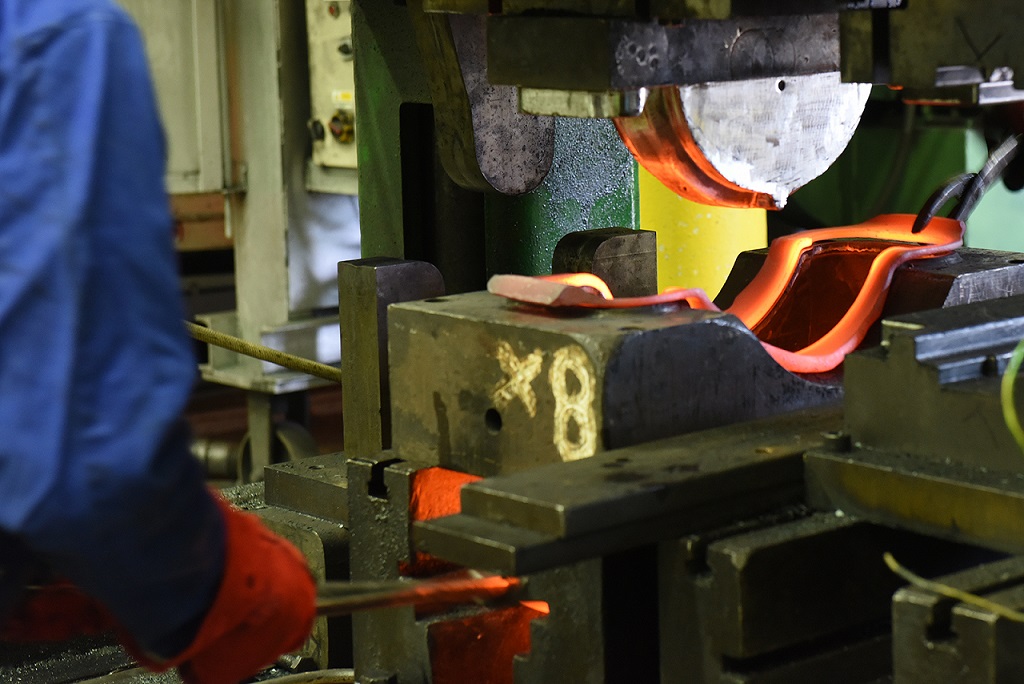
The technique of drop forging has evolved over the ages and what began as an art form, where decorative objects were produced from precious metals, developed into a technically advanced manufacturing process, with an equally complex supply chain. Drop forging is now a major global industry, supplying high strength components for many of the world’s most innovative products and industries: automotive, truck & bus, defense, aerospace, and energy, which makes it imperative for buyers sourcing drop forged components to understand the process types, value stream map, technical advantages, and early supply partner involvement to effectively execute strategic procurement.
Buyers should be well-versed within above key considerations before sourcing a forging to ensure sourcing success. There must be cross-functional team awareness on the true cost and not just the short-term piece price cost to ensure long-term drop forging supply success. Drop forgings are unique and every case must be analyzed and clearly understood prior to starting the procurement process. Keep in mind these key considerations and you will be well positioned to offer your company the best supply options while driving down your drop forging true cost, which will create a win-win value and relationship across organization and supply partners.
Drop forging is one of the common ways to manufacture a metal component. But what creats this method and why drop forgings so remarkably strong and tough? There are mainly two key aspects explaining why drop forging creates stronger products than other metal working processes and is an ideal manufacturing process for many critical metal components: predictable grain structure and uniformity.
The traditional process of drop forging involves heating a billet and placing it into a die, where it then is put under extreme pressure by a “hammer” and forced into the die's shape. During this process, the grain flow of the metal is actually altered, conforming to the shape of the part. This process makes the metal component stronger, tougher and much more reliable. The importance of grain structure cannot be underestimated. The process of bar stock and plate machining, for example, creates unidirectional grain flow. This means that any changes to the contour will ultimately cut flow lines, exposing the grain ends and making the metal more vulnerable to fatigue and corrosion.
The grain structure and flow created during the drop forging process is directional and has been placed in a way as to increase the strength and toughness of the part, thus creating overall directional strength. Since no grain ends are exposed, a drop forged metal component is less susceptible to wear and tear.
The traditional process of drop forging involves heating a billet and placing it into a die, where it then is put under extreme pressure by a “hammer” and forced into the die's shape. During this process, the grain flow of the metal is actually altered, conforming to the shape of the part. This process makes the metal component stronger, tougher and much more reliable. The importance of grain structure cannot be underestimated. The process of bar stock and plate machining, for example, creates unidirectional grain flow. This means that any changes to the contour will ultimately cut flow lines, exposing the grain ends and making the metal more vulnerable to fatigue and corrosion.
The grain structure and flow created during the drop forging process is directional and has been placed in a way as to increase the strength and toughness of the part, thus creating overall directional strength. Since no grain ends are exposed, a drop forged metal component is less susceptible to wear and tear.
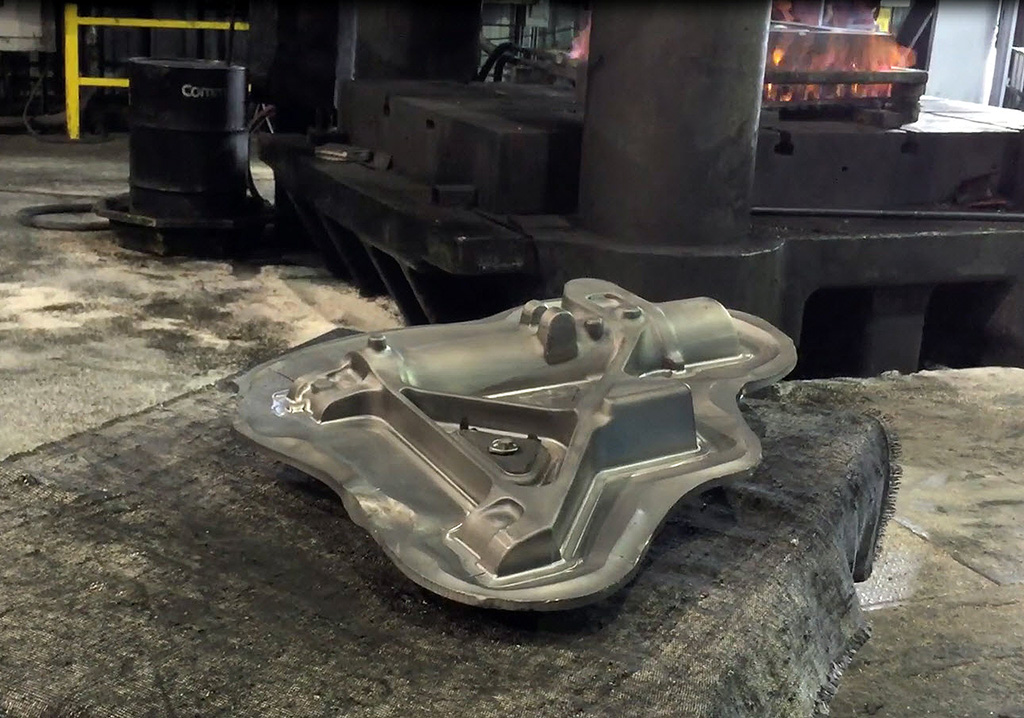
The demand of aluminum forging is getting larger than before. Here are some main advantages of aluminum forgings:
- Low density, only 34% of steel forgings and 30% of copper forgings. Aluminum alloys are ideal lightweight materials.
- High strength, high stiffness, high elastic modulus and high fatigue strength, it is suitable for the key stressed parts with high requirement of lightening. Its comprehensive performance is much higher than that of other materials.
- The internal structure is compact, uniform and free of defects, and its reliability is much higher than that of aluminum alloy castings and other metal castings.
- Aluminum alloy has good plasticity, which can be processed into high-precision forging pieces with complex shapes. The machining allowance is small, only about 20% of the machining allowance of aluminum alloy tensile thick plate, which greatly saves time and cost.
- Aluminum forgings have good corrosion resistance, thermal conductivity and non - magnetic properties, which cannot be compared with steel forgings.
- The surface is bright and clean, beautiful. Besides, the surface treatment performance is good, beautiful and durable.
- It can be seen that aluminum forgings have a series of excellent features, providing good conditions for aluminum forgings to replace steel, copper, magnesium, wood and plastics.
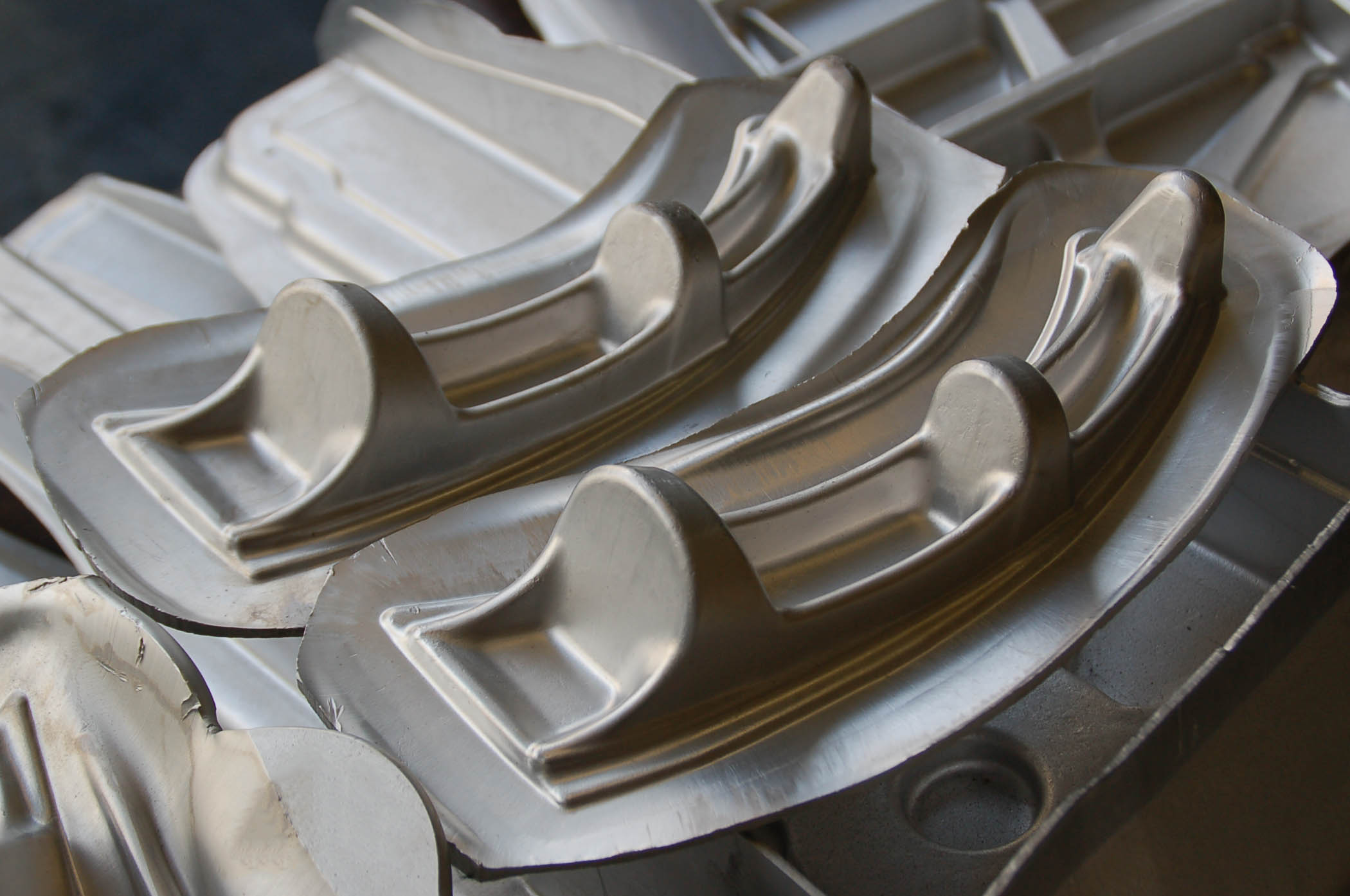
Forging process is the common metal working process in production. It mainly takes advantage of the plasticity of materials and causes plastic deformation of materials with the help of external forces, so as to obtain required shapes, sizes and certain performances. As far as the forging process itself is concerned, the advantage is that the inside of the forging is compact, the structure is relatively uniform, and there are no pores in the interior. The drawback is that larger deformation forces are required. According to the placement of tools and molds, forging can be divided into open die forging, closed die forging and roll forging. Open die forging is formed by a fixed flat anvil, the forging die of roll forging is mobile, and the forging die of closed die forging is fixed. According to the forging temperature, forging can be divided into hot forging, cold forging and warm forging. Aluminum and aluminum alloy are the most widely used nonferrous metals, with the yield second only to that of steel. Some key processes in aluminum alloy forging are introduced below.
Aluminum alloy can be used in the manufacturing of mechanical parts or components which bear large loads and become widely used non-ferrous metal materials in the industry. Due to its high specific strength and light weight, aluminum alloy becomes the main structural material of aerospace forgings. As a common metal material in daily forging production, the application of aluminum alloy is far more than that. More applications and improvements of aluminum forgings need to be found.
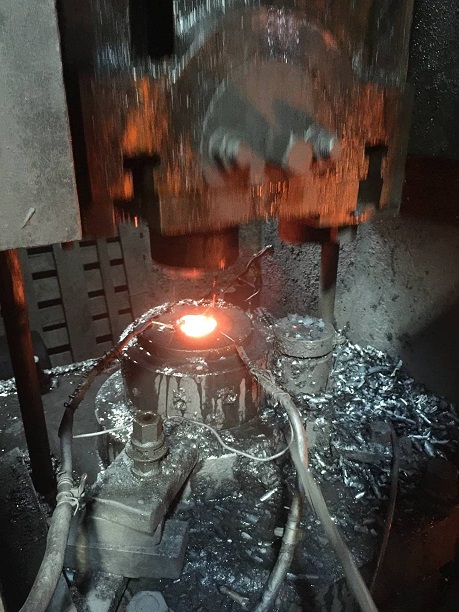
CFS Closed Die Forging Company sets the industry standard for quality, performance, craftsmanship, and customer service. Our closed die drop forgings help the leading brands in the mining, gear, aerospace, energy, and defense industries run. That’s because we use the highest-quality materials expertly engineered to fit each customer’s individual needs from standard to custom die forgings. Any inquiry on closed die forging, pls get in touch with us.
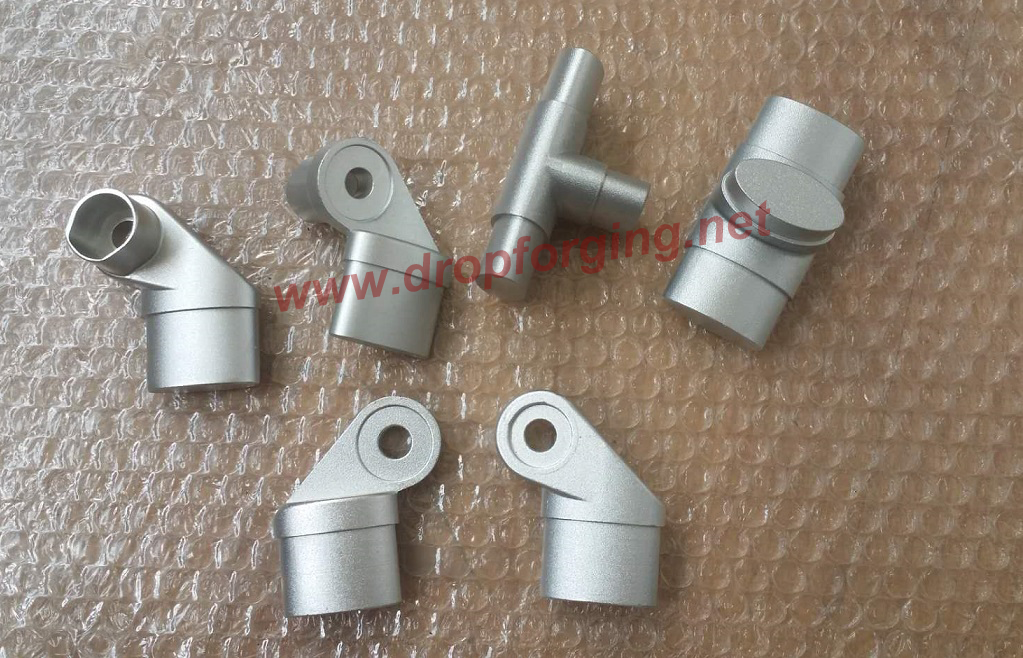
Question: “We currently have a Marine Deck chair manufactured for us, but with alloy castings. Need to change the castings into drop forged components so we can anodize. Can your forging company help me?” Mitchell said.
Mitchell is the deck chair seller in New Zealand, who ever had his chair fittings casted in aluminum alloy. But now due to the fact that both the surface finish and strength of casted chair fittings are not good, so he wants to convert these aluminum chair fittings into drop forging process.
He did not have the technical drawings, but sent us the actual samples, which were originally casted. Once the samples were received, we found that there are totally six components, which are all not large. According to the shapes of these samples, our engineer judged that we had the ability to change these castings into drop forged components. But due to the differences between casting and forging, some post machining operations would be added after forging. In terms of casting, the effect of anodization treatment is not good, so this kind of surface finish is only suitable for aluminum forgings, whose surface will look shining and smooth.

In copper forging process, a metal part is heated and formed into a predetermined shape between a set of dies. The process involves heating a metal slug and then pressing it into shape within a die cavity. Not only is the metal shaped, but the forging process also improves the mechanical and physical properties of the part. Forging today is performed on high-speed automatic equipment.
CFS Drop Forge is one of the top copper forging companies in China. We are registered with ISO 9001:2000, ISO/TS 16949 with 150 employees.Our team manufactures with drop forgings out of copper, brass and bronze for all industrial application. With the electro- hydraulic forging press, forgings up to a weight of 50 kg can be manufactured. Therefore these purpose necessary parameters which are steered precisely such as the temperature of the tool and the rough stamping, the velocity of transforming and the shaping energy are basic requirements for a high quality deformation.