Case Study: Change Castings into Drop Forged Components
Question: “We currently have a Marine Deck chair manufactured for us, but with alloy castings. Need to change the castings into drop forged components so we can anodize. Can your forging company help me?” Mitchell said.
Analysis:
Mitchell is the deck chair seller in New Zealand, who ever had his chair fittings casted in aluminum alloy. But now due to the fact that both the surface finish and strength of casted chair fittings are not good, so he wants to convert these aluminum chair fittings into drop forging process.
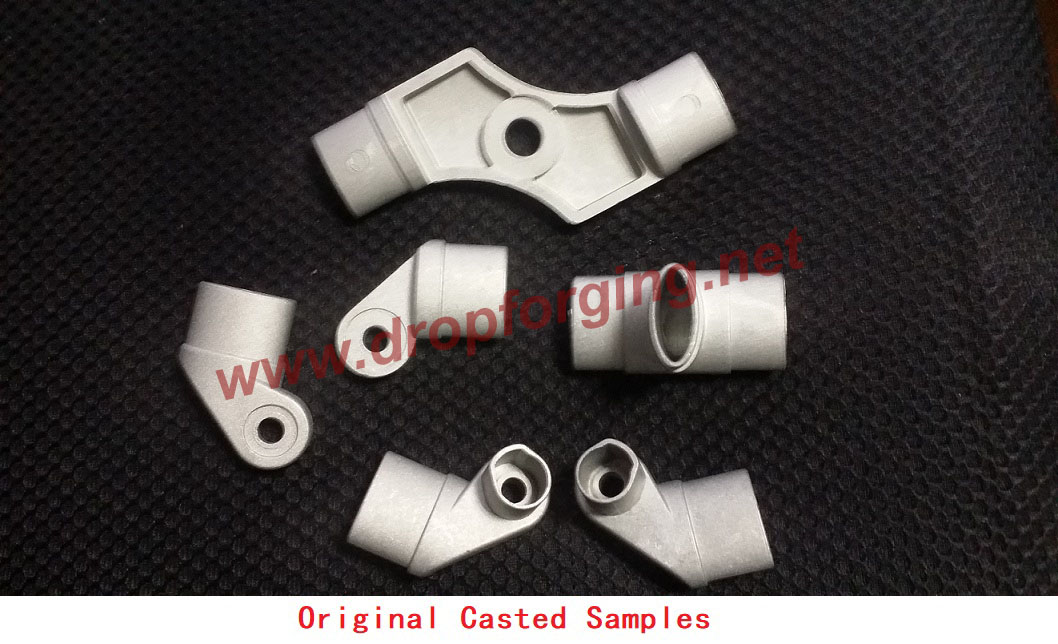
He did not have the technical drawings, but sent us the actual samples, see above picture, which were originally casted. Once the samples were received, we found that there are totally six components, which are all not large. According to the shapes of these samples, our engineer judged that we had the ability to change these castings into drop forged components. But due to the differences between casting and forging, some post machining operations would be added after forging. In terms of casting, the effect of anodization treatment is not good, so this kind of surface finish is only suitable for aluminum forgings, whose surface will look shining and smooth.
Based on the material aluminum 6061-T6 for drop forged chair components, we sent the quotation to Mitchell for approval. Due to our reasonable prices, the sample order was placed to our forging company soon. Pls note, for such convertion from casting to drop forging, all the molds of these six components would have to be remade. Before making molds/dies, our engineer redesigned the drawings according to the original casted samples.
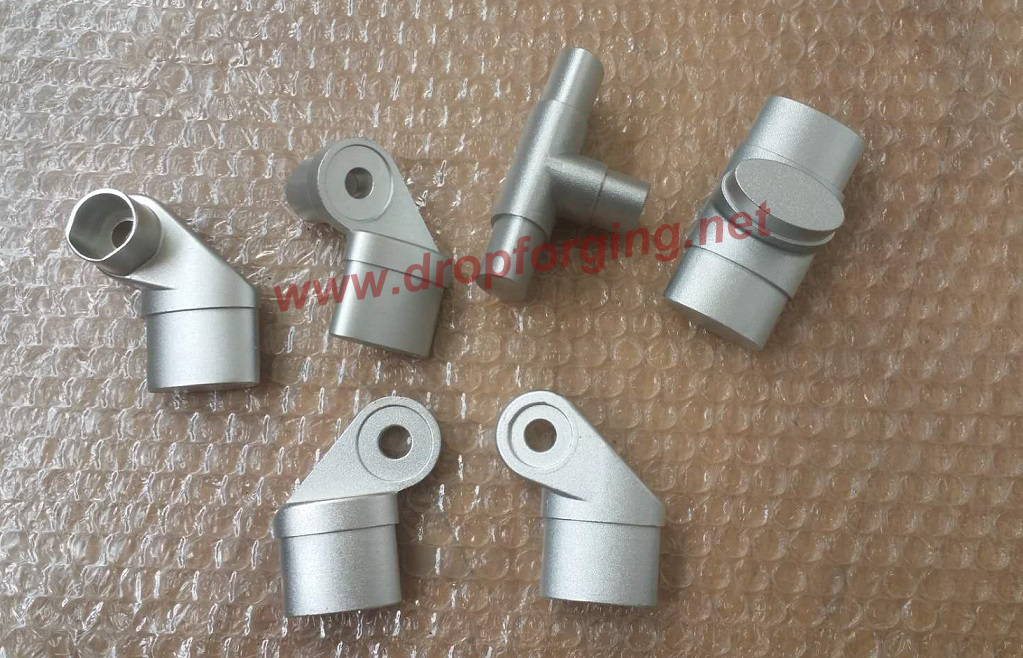
As there are totally 6 components, so the whole production cycle was slightly longer than a single one. We have to finish each process (mould making, forging, machining, anodization and testing) step by step. After testing, the drop forged samples were posted to our customer, below is the assembly picture from our customer.
Above is just one case showing the convertion from casting to drop forging. As a top closed die forging company, we can also change other casted components into drop forged components, so that the strength will be better, and the serving life can be longer, which is a cost effective solution in the long term. If you have such demands, also pls do not hesitate to contact us. I believe you will be satisfied with our quality and pricing.
Analysis:
Mitchell is the deck chair seller in New Zealand, who ever had his chair fittings casted in aluminum alloy. But now due to the fact that both the surface finish and strength of casted chair fittings are not good, so he wants to convert these aluminum chair fittings into drop forging process.
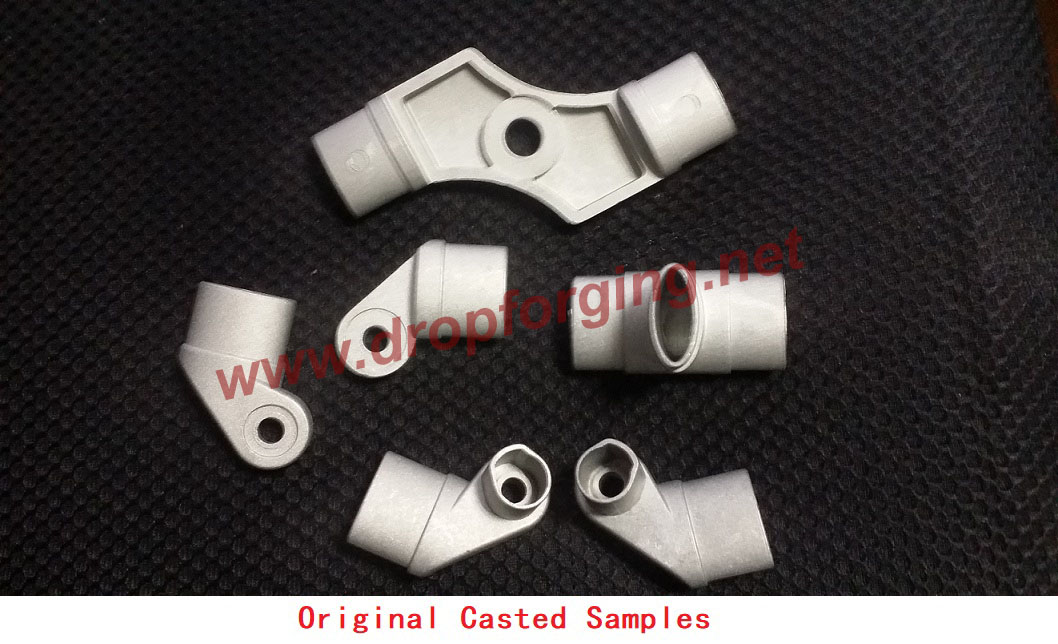
He did not have the technical drawings, but sent us the actual samples, see above picture, which were originally casted. Once the samples were received, we found that there are totally six components, which are all not large. According to the shapes of these samples, our engineer judged that we had the ability to change these castings into drop forged components. But due to the differences between casting and forging, some post machining operations would be added after forging. In terms of casting, the effect of anodization treatment is not good, so this kind of surface finish is only suitable for aluminum forgings, whose surface will look shining and smooth.
Based on the material aluminum 6061-T6 for drop forged chair components, we sent the quotation to Mitchell for approval. Due to our reasonable prices, the sample order was placed to our forging company soon. Pls note, for such convertion from casting to drop forging, all the molds of these six components would have to be remade. Before making molds/dies, our engineer redesigned the drawings according to the original casted samples.
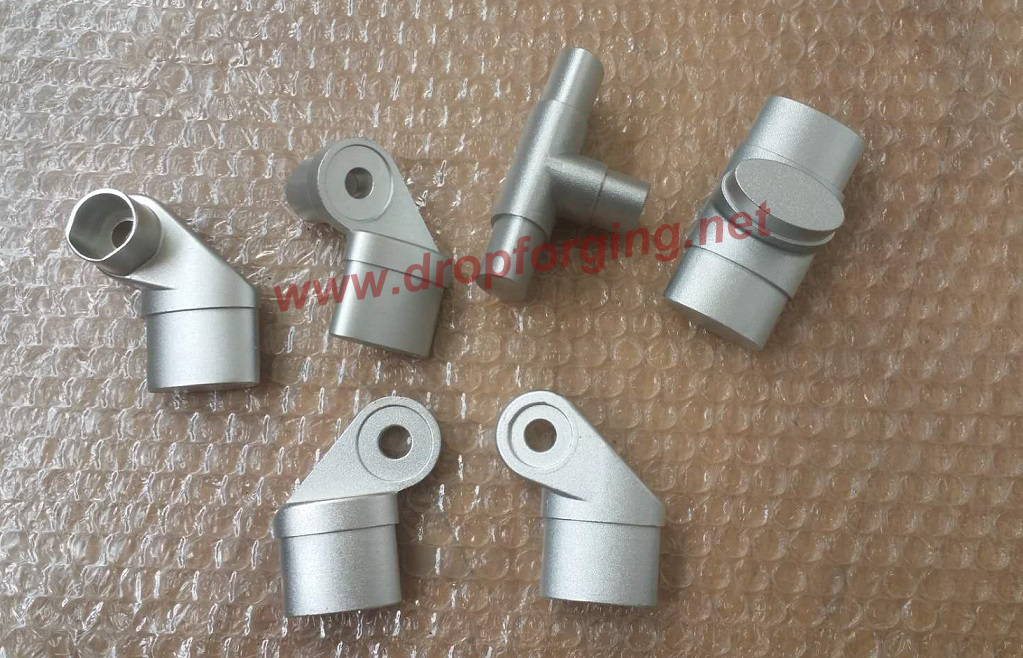
As there are totally 6 components, so the whole production cycle was slightly longer than a single one. We have to finish each process (mould making, forging, machining, anodization and testing) step by step. After testing, the drop forged samples were posted to our customer, below is the assembly picture from our customer.
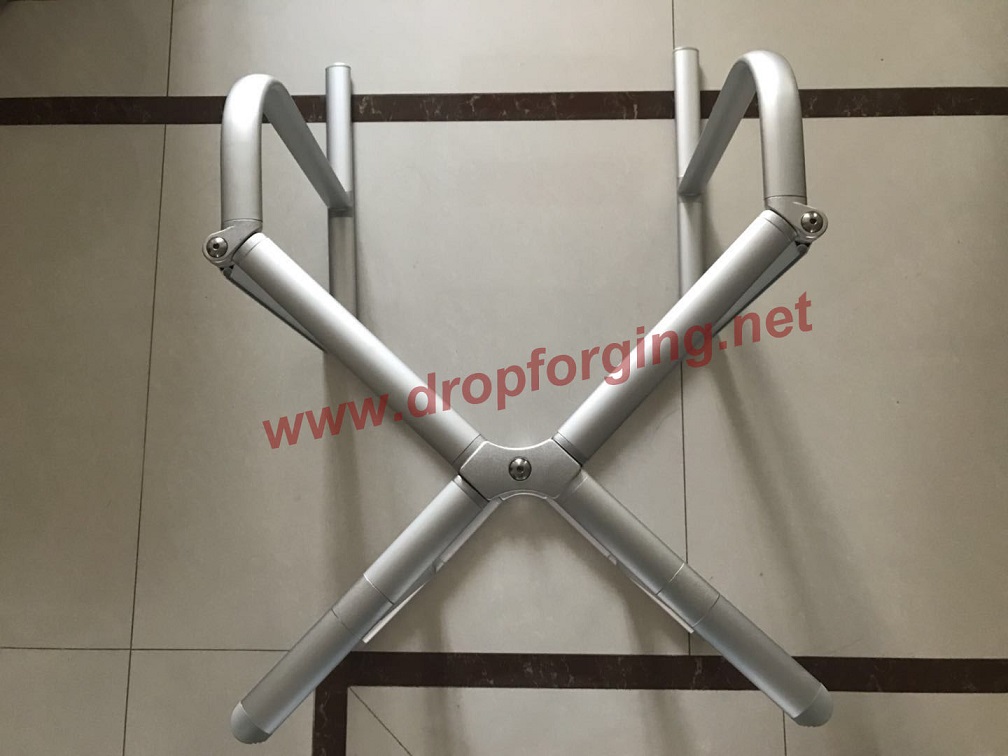