Which Metals Work Best for Drop Forging?
Drop forging is becoming one of the most relied upon manufacturing methods due to its reliable quality and strength. Drop forging is used in the production of a wide range of products that can be found in just about any industry or vertical you can think of.
Of course, like with casting processes, drop forged products will only be as good as the metals being used in their production. There are serveral types of metals available in drop forging process. As such, this blog will explore the various metals involved in the drop forging process.
Before getting into the most ideal metals for drop forging, let’s first talk a bit about the drop forging process.
Drop forging is a metal working process that involves forcing solid metal under high pressure into the cavity of forging dies. Drop forging allows for the filling of metal into dies with accurate dimensions, sharp definition, and smooth surfaces.
A General Breakdown of the Drop Forging Process
Drop forging is one of the most popular manufacturing methods due to its simplicity, speed, and stability. Here’s a step-by-step look at the drop forging process:
When starting a drop forging project, there are a number of metals and alloys that can be used. Each of the alloys has unique physical characteristics that have benefits for different applications.
It can be tricky to understand all of the mechanical properties, physical properties, and the compositions of different alloys, so it’s always a good idea to speak with an experienced drop forging company. The most commonly used drop forged metals are as follows:
Steel
Steel is the world's most important engineering and construction material. It is used in every aspect of our lives; in cars and construction products, refrigerators and washing machines, cargo ships and surgical scalpels.
Due to its low cost, steel is the most common drop forging material. Types of drop forged steel include: stainless steel, alloy steel and carbon steel. Steel is a strong, durable, and versatile drop forged material, but it also has another key trait: sustainability.
Drop forged steel is an alloy of carbon and iron that is compressed under extreme pressure to make a very hard and strong substance. It has been used for thousands of years to create all types of materials. Modern drop forged steel is conducted using specialized machines or hydraulic hammers. Drop forged steel is used in a variety of industries. Everything from manufacturing to pharmaceuticals utilize the benefits of drop forged steel. Anything that can be made of metal can generally be made stronger and more weight-conscious by drop forged steel.
Aluminum
Aluminum is one of the most popular metals used in drop forging. Aluminum is a very lightweight metal, so it’s great for creating lightweight parts without sacrificing strength. Drop forged aluminum parts can also withstand higher operating temperatures and have more finishing options.
Despite being pricier options, aluminum and aluminum-zinc alloys are definitely worth the cost in industrial applications. They are incredibly corrosion-resistant materials that contribute to an extended lifespan and improved safety. Furthermore, the strength, hardness, and weight ratios are unparalleled.
Another clear advantage of aluminum is that – plainly – it’s easy to forge. Its electrical and thermal conductivity properties are optimal. These characteristics make aluminum an excellent option in the drop forging production of components for computing, energy management, and other tech fields.
Because of these many benefits, drop forged aluminum is very popular in the production of things like industrial components, automobile parts, tech products, aerospace products, and much more.
Copper
The outstanding characteristics of copper, are high electrical and thermal conductivities, ductility and corrosion resistance. Many applications of drop forged parts are based on these characteristics.
Copper powder with a purity of more than 99% copper is available commercially, and drop forged parts produced from these powders have electrical conductivities of 80% to 95% IACS as pressed and sintered. Higher conductivities, approaching 100% IACS can be achieved by further densification. High electrical conductivity also means high thermal conductivity. Thus, drop forged parts have a significant advantage for the production of electronic and electrical components, where electrical or thermal conductivity is an essential attribute.
Copper is a very ductile and malleable metal. Parts drop forged from copper have excellent ductility. Besides good strength, drop forged copper alloys are resistant to a wide variety of corrosive environments.
Drop forging is a thriving facet of the metal working industry. It’s tried, tested, and proven method that is conducive to streamlined, high-quality production. Not only is it a cost-efficient way to produce custom metal parts and components, but also allows you to create complex net shapes and good surface finish features.
If you’re interested in finding out more about our drop forging services, contact CFS Forge to speak with one of our experienced sales team today to get a free quote on your project.
Of course, like with casting processes, drop forged products will only be as good as the metals being used in their production. There are serveral types of metals available in drop forging process. As such, this blog will explore the various metals involved in the drop forging process.
Before getting into the most ideal metals for drop forging, let’s first talk a bit about the drop forging process.
What is Drop Forging?
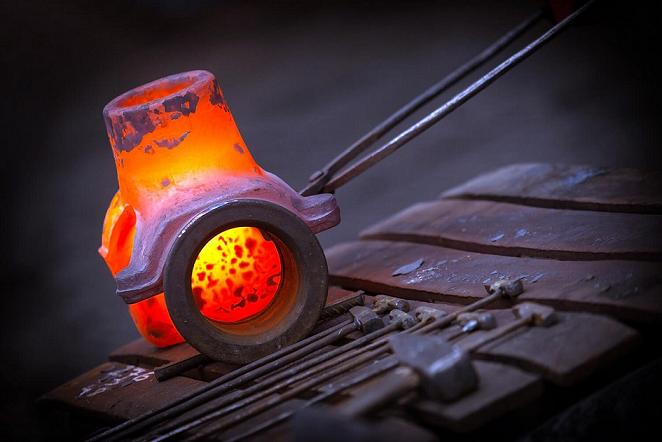
A General Breakdown of the Drop Forging Process
Drop forging is one of the most popular manufacturing methods due to its simplicity, speed, and stability. Here’s a step-by-step look at the drop forging process:
- A pair of forging dies must be made into two halves to allow for the forging of metals.
- This mold can produce ten thousands of forgings quickly in succession.
- After heating of metal billets, place them under upper and lower dies to get pressed, then take out the forged blanks from the dies carefully.
- Remove the flash by punch machine with trimming dies.
- Shot blasting to achieve good surface.
What Metals Are the Most Popular Options for Drop Forging?
When starting a drop forging project, there are a number of metals and alloys that can be used. Each of the alloys has unique physical characteristics that have benefits for different applications.
It can be tricky to understand all of the mechanical properties, physical properties, and the compositions of different alloys, so it’s always a good idea to speak with an experienced drop forging company. The most commonly used drop forged metals are as follows:
Steel
Steel is the world's most important engineering and construction material. It is used in every aspect of our lives; in cars and construction products, refrigerators and washing machines, cargo ships and surgical scalpels.
Due to its low cost, steel is the most common drop forging material. Types of drop forged steel include: stainless steel, alloy steel and carbon steel. Steel is a strong, durable, and versatile drop forged material, but it also has another key trait: sustainability.
Drop forged steel is an alloy of carbon and iron that is compressed under extreme pressure to make a very hard and strong substance. It has been used for thousands of years to create all types of materials. Modern drop forged steel is conducted using specialized machines or hydraulic hammers. Drop forged steel is used in a variety of industries. Everything from manufacturing to pharmaceuticals utilize the benefits of drop forged steel. Anything that can be made of metal can generally be made stronger and more weight-conscious by drop forged steel.
Aluminum
Aluminum is one of the most popular metals used in drop forging. Aluminum is a very lightweight metal, so it’s great for creating lightweight parts without sacrificing strength. Drop forged aluminum parts can also withstand higher operating temperatures and have more finishing options.
Despite being pricier options, aluminum and aluminum-zinc alloys are definitely worth the cost in industrial applications. They are incredibly corrosion-resistant materials that contribute to an extended lifespan and improved safety. Furthermore, the strength, hardness, and weight ratios are unparalleled.
Another clear advantage of aluminum is that – plainly – it’s easy to forge. Its electrical and thermal conductivity properties are optimal. These characteristics make aluminum an excellent option in the drop forging production of components for computing, energy management, and other tech fields.
Because of these many benefits, drop forged aluminum is very popular in the production of things like industrial components, automobile parts, tech products, aerospace products, and much more.
Copper
The outstanding characteristics of copper, are high electrical and thermal conductivities, ductility and corrosion resistance. Many applications of drop forged parts are based on these characteristics.
Copper powder with a purity of more than 99% copper is available commercially, and drop forged parts produced from these powders have electrical conductivities of 80% to 95% IACS as pressed and sintered. Higher conductivities, approaching 100% IACS can be achieved by further densification. High electrical conductivity also means high thermal conductivity. Thus, drop forged parts have a significant advantage for the production of electronic and electrical components, where electrical or thermal conductivity is an essential attribute.
Copper is a very ductile and malleable metal. Parts drop forged from copper have excellent ductility. Besides good strength, drop forged copper alloys are resistant to a wide variety of corrosive environments.
Starting A Drop Forging Project With CFS
Drop forging is a thriving facet of the metal working industry. It’s tried, tested, and proven method that is conducive to streamlined, high-quality production. Not only is it a cost-efficient way to produce custom metal parts and components, but also allows you to create complex net shapes and good surface finish features.
If you’re interested in finding out more about our drop forging services, contact CFS Forge to speak with one of our experienced sales team today to get a free quote on your project.