Brass Forging
Forging is the metal processing process that puts pressure on metal billets, which will occur plastic deformation to achieve a certain mechanical properties and desired shape by the use of forging press machinery. Brass is the most common material in copper forging.
Brass Forging Aims to:
Although brass has good plasticity at room temperature and high temperature, there is a medium temperature brittleness zone, so the forging temperature range is narrow. Temperature control is of vital importance. Taking HPb59-1 for example, the proper forging temperature should be at 680-750℃。
1) Billet
Based on the design of forging dies, choose billets with proper outer dimensions and cut into required length.
2) Heating
Heating billets to designed forging temperature.
Under the conditions of the thermal conductivity and internal stress allowed by metal materials, heat up to the preset temperature as fast as possible, improve efficiency and save energy.
When heating brass, reduce absorption of harmful gases as far as possible, such as oxygen, hydrogen, nitrogen and other gases. Besides, try to avoid defects like oxidation, thus to improve heating quality.
In the low temperature heating stage, the cracks caused by improper heating should be prevented.
3) Forging
Forging heated billets to desired shapes by forging dies.
Brass hot forging is the plastic forming in solid state, which deforms the blank by the external force. This brass forming method is mainly shaped in the high temperature by pressing.The grain of brass can be refined and its physical properties are also improved.(Solid to Solid)
Brass casting is the process of filling the mold cavity with molten brass in liquid state and cooling it into solid. In simple terms, it is the process of turning the metal liquid without shape into shaped solid. After heating and melting the copper material, it is poured into the mold, cooled and solidified into the desired brass workpiece.
Brass casting does not have the advantages of forging, so it is easy to produce gas holes in the production process, but it can make parts with complex shapes, so it is often used in the manufacture of blank with low mechanical performance. Brass forging can cause plastic deformation of brass billet and refine grain. Therefore, it is often used in the manufacture of important components.
Why do customers choose CFS Drop Forge at their supplier for high quality brass forgings? We furnish assistance at every stage in the process of creating excellent custom-designed forgings. Our goal remains complete customer satisfaction.
By selecting our company, you’ll obtain an outstanding selection of brass alloys to use in the creation of forging components meeting your specifications. We support a wide variety of applications.
Additionally, our well-equipped manufacturing facility enables us to draw upon high-precision equipment to assist the creation of forgings meeting customer requirements. We’ll complete projects using modern machinery. We perform rigorous quality control procedures to help maintain part consistency.
We take great pride in supplying high quality customized brass forgings at competitive prices. Looking for a reliable brass forging company in China? Email us to send your RFQs right now!
Brass Forging Aims to:
- Compared with machining, forging brass billets can form various shapes with metal flows, which will save material and time.
- Refine the inner structure to improve its density and mechanical properties.
Although brass has good plasticity at room temperature and high temperature, there is a medium temperature brittleness zone, so the forging temperature range is narrow. Temperature control is of vital importance. Taking HPb59-1 for example, the proper forging temperature should be at 680-750℃。
Basic Steps of Brass Forging
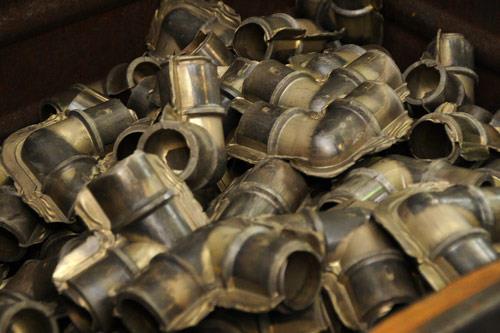
Based on the design of forging dies, choose billets with proper outer dimensions and cut into required length.
2) Heating
Heating billets to designed forging temperature.
Under the conditions of the thermal conductivity and internal stress allowed by metal materials, heat up to the preset temperature as fast as possible, improve efficiency and save energy.
When heating brass, reduce absorption of harmful gases as far as possible, such as oxygen, hydrogen, nitrogen and other gases. Besides, try to avoid defects like oxidation, thus to improve heating quality.
In the low temperature heating stage, the cracks caused by improper heating should be prevented.
3) Forging
Forging heated billets to desired shapes by forging dies.
Difference Between Brass Forging and Brass Casting
Brass hot forging is the plastic forming in solid state, which deforms the blank by the external force. This brass forming method is mainly shaped in the high temperature by pressing.The grain of brass can be refined and its physical properties are also improved.(Solid to Solid)
Brass casting is the process of filling the mold cavity with molten brass in liquid state and cooling it into solid. In simple terms, it is the process of turning the metal liquid without shape into shaped solid. After heating and melting the copper material, it is poured into the mold, cooled and solidified into the desired brass workpiece.
Brass casting does not have the advantages of forging, so it is easy to produce gas holes in the production process, but it can make parts with complex shapes, so it is often used in the manufacture of blank with low mechanical performance. Brass forging can cause plastic deformation of brass billet and refine grain. Therefore, it is often used in the manufacture of important components.
Why Customers Select CFS Drop Forge for Brass Forgings?
Why do customers choose CFS Drop Forge at their supplier for high quality brass forgings? We furnish assistance at every stage in the process of creating excellent custom-designed forgings. Our goal remains complete customer satisfaction.
By selecting our company, you’ll obtain an outstanding selection of brass alloys to use in the creation of forging components meeting your specifications. We support a wide variety of applications.
Additionally, our well-equipped manufacturing facility enables us to draw upon high-precision equipment to assist the creation of forgings meeting customer requirements. We’ll complete projects using modern machinery. We perform rigorous quality control procedures to help maintain part consistency.
We take great pride in supplying high quality customized brass forgings at competitive prices. Looking for a reliable brass forging company in China? Email us to send your RFQs right now!