Open Die Forging
Open die forging is another drop forging process that metal is getting deformed for desire shapes without any limitation between the top and bottom anvils in all directions utilizing power or pressure. So it is also named as free forging.
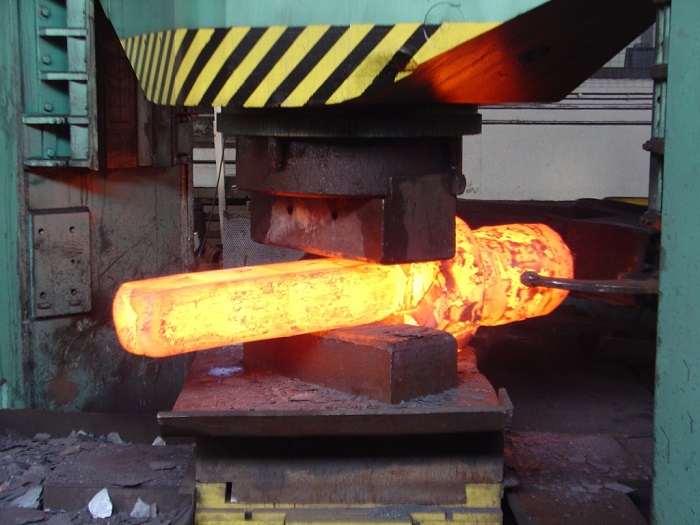
Main feature of open die forging is that the production equipment is relatively simple, so the cost is low. Compared with the casting blank, open die forging eliminates the defects such as shrinkage, gas holes, porosity, ect. So products after open die forging have higher mechanical properties. Unlike closed die forging, open die forging shape is simple and the operation is flexible, therefore, it always act as important parts in heavy machinery equipments.
Another feature is that the shape and dimensions of open die forgings is mainly controlled by manual operation. So the size accuracy of products is relatively low, and the machining allowance will be large with high working strength. That is why open die forging is mainly applied for single and low volume production.
Open die forging is currently operated by labour and machines.
With labour operation, the production efficiency is low, and working strength is large, so this kind of production way is only suitable for simple and single production.
In modern prodcution, machines have become the main way for open die forging production.The degree of operator's profession will also affect the dimensions and accuracy of products.
Open die forging equipments are mainly devided into forging hammer and hydraulic press. Main used forging hammers are air hammer and steam hammer. Hydraulic press is working and getting blanks deformed by using of static pressure that produced by liquid. This is the only method to produce large forgings.
Basic open die forging process includes upsetting, drawing out, punching, bending, torsion, mismatch, cutting and welding, etc.
Drawing out is also called as elongation. This process will reduce the cross-sectional area ahnd add the length of blank. Drawing out is commonly used for forging rod and shaft parts. There are two ways of drawing out:
1. Drawing out on flat anvil
2. Drawing out on core shaft. When forging, first insert core shaft into punched blank, then draw out as solid blank. The drawing out is not one time operation, we will first need to draw the blank into hexangular shape and forge it to required length, then break edges and rounded, next get out of core shafe. This drawing out method can longer the hollow blank and reduce the wall thickness, but inner diameter keeps the same as before.This kind of forging method is suitable for sleeve type forgings.
Upsetting is the forging process that reduce the height and add the cross-sectional area of blanks. Upsetting is mainly used to produce gear blanks, ring blanks, ect. By upsetting, we can effectively improve the structure of blanks and reduce the anisotropy of mechanical properties.
There are three types of upsetting:
1. Completely upsetting. Completely upsetting is the plastic deformation that reduce the height and increase cross-sectional area under the hammer of upper anvil by putting blank vertically on the anvils.
2. End upsetting. End upsetting is the process that, after heating the billet, place one end in mold for limiting its plastic deformation, and hammer the other end of billet to get upset.
3. Middle upsetting. This method is used for forgings whose middle cross-sectional area is large, but small in both ends. Before upsetting billet, should first will pull out fine on both ends of the billet, and then make the billet upright between two leaking plate for hammer, thus to make the middle part of billet upsetting.
When upsetting, in order to avoid bending the blank, the ratio of billet height (h) and diameter (d) should be less than 2.5.
Punching is the forging process that rushing out through hole or unthrought hole on the billet.
Bending is operated for desired shape under the force of a certain tool or mould.
Cutting is the process that divide the billet into several sections, or cut a small area from one end.
Mismatch is that moving part of the billet for a certain distance, but still keep parallel between the two axises. This method is more used for forging crankshaft part.
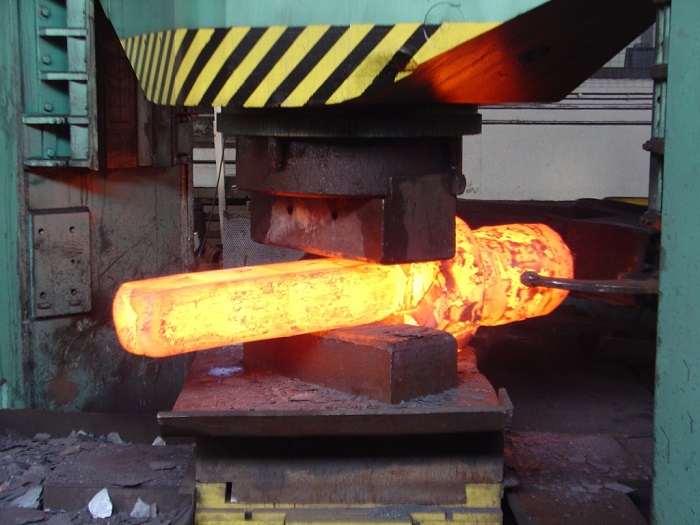
Main feature of open die forging is that the production equipment is relatively simple, so the cost is low. Compared with the casting blank, open die forging eliminates the defects such as shrinkage, gas holes, porosity, ect. So products after open die forging have higher mechanical properties. Unlike closed die forging, open die forging shape is simple and the operation is flexible, therefore, it always act as important parts in heavy machinery equipments.
Another feature is that the shape and dimensions of open die forgings is mainly controlled by manual operation. So the size accuracy of products is relatively low, and the machining allowance will be large with high working strength. That is why open die forging is mainly applied for single and low volume production.
Production of Open Die Forging
Open die forging is currently operated by labour and machines.
With labour operation, the production efficiency is low, and working strength is large, so this kind of production way is only suitable for simple and single production.
In modern prodcution, machines have become the main way for open die forging production.The degree of operator's profession will also affect the dimensions and accuracy of products.
Main Equipments
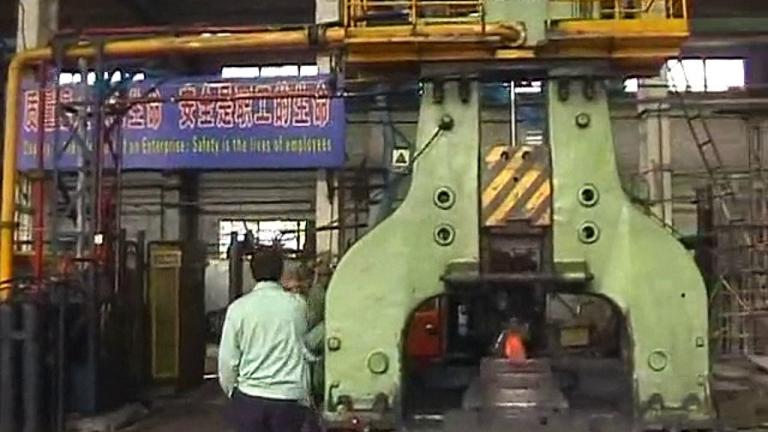
Open Die Forging Process
Drawing out is also called as elongation. This process will reduce the cross-sectional area ahnd add the length of blank. Drawing out is commonly used for forging rod and shaft parts. There are two ways of drawing out:
1. Drawing out on flat anvil
2. Drawing out on core shaft. When forging, first insert core shaft into punched blank, then draw out as solid blank. The drawing out is not one time operation, we will first need to draw the blank into hexangular shape and forge it to required length, then break edges and rounded, next get out of core shafe. This drawing out method can longer the hollow blank and reduce the wall thickness, but inner diameter keeps the same as before.This kind of forging method is suitable for sleeve type forgings.
Upsetting is the forging process that reduce the height and add the cross-sectional area of blanks. Upsetting is mainly used to produce gear blanks, ring blanks, ect. By upsetting, we can effectively improve the structure of blanks and reduce the anisotropy of mechanical properties.
There are three types of upsetting:
1. Completely upsetting. Completely upsetting is the plastic deformation that reduce the height and increase cross-sectional area under the hammer of upper anvil by putting blank vertically on the anvils.
2. End upsetting. End upsetting is the process that, after heating the billet, place one end in mold for limiting its plastic deformation, and hammer the other end of billet to get upset.
3. Middle upsetting. This method is used for forgings whose middle cross-sectional area is large, but small in both ends. Before upsetting billet, should first will pull out fine on both ends of the billet, and then make the billet upright between two leaking plate for hammer, thus to make the middle part of billet upsetting.
When upsetting, in order to avoid bending the blank, the ratio of billet height (h) and diameter (d) should be less than 2.5.
Punching is the forging process that rushing out through hole or unthrought hole on the billet.
Bending is operated for desired shape under the force of a certain tool or mould.
Cutting is the process that divide the billet into several sections, or cut a small area from one end.
Mismatch is that moving part of the billet for a certain distance, but still keep parallel between the two axises. This method is more used for forging crankshaft part.
Common Open Die Forging Defects
- Crack. It could be caused by bad billet quality, unsufficient heating, low forging temperature or wrong cooling method. Besides, unproper forging method may also cause the crack.
- Depressed deformation on end and crack in axis.
- Fold