Manufacturing Guide of Drop Forging
What is Drop Forging?
Drop forging is manufacturing process where metal is pressed under great pressure into high strength parts known as drop forgings. The process is normally (but not always) performed hot by preheating the metal to a desired temperature before it is worked. It is important to note that the drop forging process is entirely different from the casting process, as metal used to make forged parts is never melted and poured (as in the casting process).
The drop forging process can create parts that are stronger than those manufactured by any other metalworking process. This is why forgings are almost always used where reliability and human safety are critical. But you'll rarely see drop forgings, as they are normally component parts contained inside assembled items such a airplanes, automobiles, tractors, ships, oil drilling equipment, engines, missiles and all kinds of capital equipment - to name a few.
How are Drop Forgings Producted?
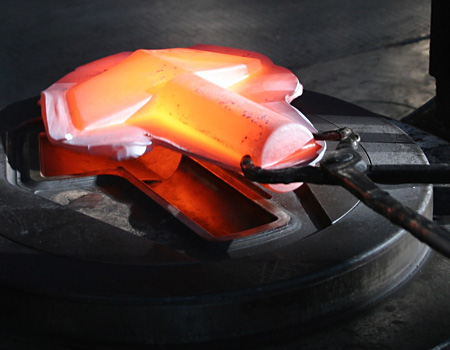
In the most basic example of closed die drop forging, which accounts for the majority of forging production, two dies are brought together and the workpiece undergoes plastic deformation until its enlarged sides touch the die side walls. Then, some material begins to flow outside the die impression, forming flash. The flash cools rapidly and presents increased resistance to deformation, effectively becoming a part of the tool. This builds pressure inside the bulk of the workpiece, aiding material flow into unfilled impressions.
Drop forgings may be produced on a horizontal forging machine (upsetter) in a process referred to as upsetting. In upsetting, stock is held between a fixed and moving die while a horizontal ram provides the pressure to forge the stock. After each ramstroke, the multiple-impression dies can open to permit transfer of stock from one cavity to another.
A form of drop forging, closed die forging does not depend on flash formation to achieve complete filling of the die. Material is deformed in a cavity that allows little or no escape of excess material, thus placing greater demands on die design.
For closed die drop forging, forging dies become more important, and operator skill level is less critical in press forging operations. The press forging sequence is usually block and finish, sometimes with a preform, pierce, or trim operation. The piece is usually hit only once in each die cavity.
Drop forging, especially closed die drop forging, normally means close-to-final form or close-tolerance forging. It is not a special technology, but a refinement of existing techniques to a point where the forged part can be used with little or no subsequent machining. Improvements cover not only the forging method itself but also preheating, descaling, lubrication, and temperature control practices.
The decision to apply drop forging techniques depends on the relative economics of additional operations and tooling vs. elimination of machining. Because of higher tooling and development costs, drop forging is usually limited to critical components with the requirement of high strength.
Related Article: What Makes Drop Forging Best for Industrial Metal Components?
All things being equal except for the Blowing Force of the drop forge hammer. Will a hammer with a higher blowing force produce a stronger metal?
For example if you had a Lasco HO-U 500 with a Blow energy of 50 [KJ] vs a Lasco 2000 with a Blow energy of 200 [KJ].
Will the 200 [KJ] hammer forge a stronger metal? Again all other things being equal . Only the Blow energy is different.