Automotive Parts Made by Closed Die Forging Process
1. Background
Metals and alloys are able to be formed into desired shapes by plastic deformation. In deformation process, they also produce a wide range of properties particularly strength and toughness. The working of the metals into shapes by means of closed die forging methods refines grain structure, develops inherent strength giving characteristics, improves physical properties and produces structural uniformity free from hidden internal defects. What's more, the special feature of flow lines along the contour of the clsoed die forging produce marked directional properties. These features in closed die forgings give the automobile designers great confidence regarding the reliability of the vehicle. Learn more about advantages and disadvantages of closed die forging in detail...
2.Features of closed die forging in automotive industry
An automobile vehicle need to carry loads at high speed and has to be light enough to save fuel. In this way, the following points regarding closed die forging are noteworthy:
(a) Closed die forged components have made possible many design to accommodate higher loads and greater stresses.
(b) Due to close tolerances, automated machining lines can be used to machine these at faster rate.
(c) Because of the use of hot-rolled products as input, reliability of internal structure is ensured. As indicated earlier, grain flow characteristics of closed die forgings give improved properties of strength, ductility and resistance to impact and fatigue.
(d) Because of the controlled sequence of production steps consistency of material composition and structure is assumed from piece to piece, and better response to heat treatment is achieved.
(e) With the elimination of internal discontinuities, low rejection rates, better machinability, less machining allowances--cost of production of aggregates is reduced considerably.
(f) Saving in weight of parts is achieved due to the inherent characteristic of higher strength to weight ratio.
Therefore, many models of auto and trucks contain over 200 separate closed die forgings.
3.Typical closed die forged components are:
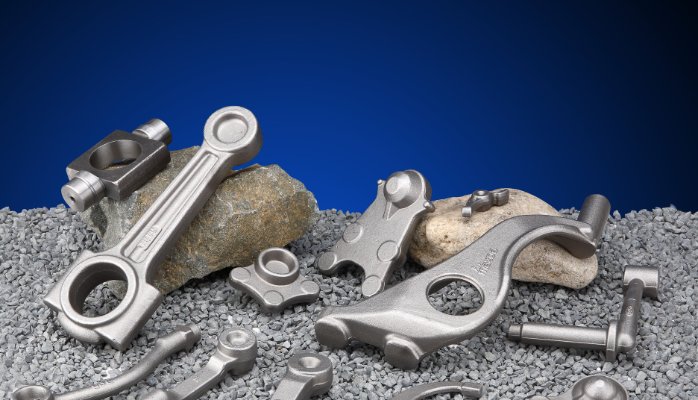
Engine components: crank shafts, connecting rods, rocker arms, cam shafts.
Transmission: gear blanks, gear shift levers, drive shaft, main shaft, propeller shaft yokes, flanges brake levers.
Steering: steering knuckle, steering shafts, steering levers, pitman arms.
Front axle: front axle beams, stub axles, front hubs.
Rear axle: rear axle shafts, differential cases and covers, crown wheels and pinions, differential gears, etc.
4.Automotive parts made by closed die forging process
This consists of hammering or pressing heated bars or billets within close impressioned dies. These impressions impart the desired shape to the work pieces. In view of the many variables in this process such as material temperature, die condition, machine load, complexity of job, die lubrication, etc. The closed die forging process consists of several steps of manufacture:
Billet heating
Reduce rolling or fullering
Bending or flattening (if necessary)
Blocker or mould
Finish forging
Billet heating (to around 1250°C) is done in forge furnaces which may be either box type pusher, walking beam, rotary hearth or induction furnaces.
Reduce-rolling is done to distribute the metal to suit forging shape in a separate rolling machine.
Flattening, bending, blocking and finish forging operations are done in the main forging unit i.e Press or a Hammer.
Trimming and hot coining operations are done on auxiliary units.
Heat treatment, shot blasting, grinding, etc are the finishing perations, which are done in separate equipments.
Automotive forgings are made by close die forging process and hence it is essential to elaborate the various features of this technology. In the first instance designs of the forged part, die and tool design are to be considered. Broadly speaking, adding material around the contours of machined piece profile constitutes the design of forged part.
Metals and alloys are able to be formed into desired shapes by plastic deformation. In deformation process, they also produce a wide range of properties particularly strength and toughness. The working of the metals into shapes by means of closed die forging methods refines grain structure, develops inherent strength giving characteristics, improves physical properties and produces structural uniformity free from hidden internal defects. What's more, the special feature of flow lines along the contour of the clsoed die forging produce marked directional properties. These features in closed die forgings give the automobile designers great confidence regarding the reliability of the vehicle. Learn more about advantages and disadvantages of closed die forging in detail...
2.Features of closed die forging in automotive industry
An automobile vehicle need to carry loads at high speed and has to be light enough to save fuel. In this way, the following points regarding closed die forging are noteworthy:
(a) Closed die forged components have made possible many design to accommodate higher loads and greater stresses.
(b) Due to close tolerances, automated machining lines can be used to machine these at faster rate.
(c) Because of the use of hot-rolled products as input, reliability of internal structure is ensured. As indicated earlier, grain flow characteristics of closed die forgings give improved properties of strength, ductility and resistance to impact and fatigue.
(d) Because of the controlled sequence of production steps consistency of material composition and structure is assumed from piece to piece, and better response to heat treatment is achieved.
(e) With the elimination of internal discontinuities, low rejection rates, better machinability, less machining allowances--cost of production of aggregates is reduced considerably.
(f) Saving in weight of parts is achieved due to the inherent characteristic of higher strength to weight ratio.
Therefore, many models of auto and trucks contain over 200 separate closed die forgings.
3.Typical closed die forged components are:
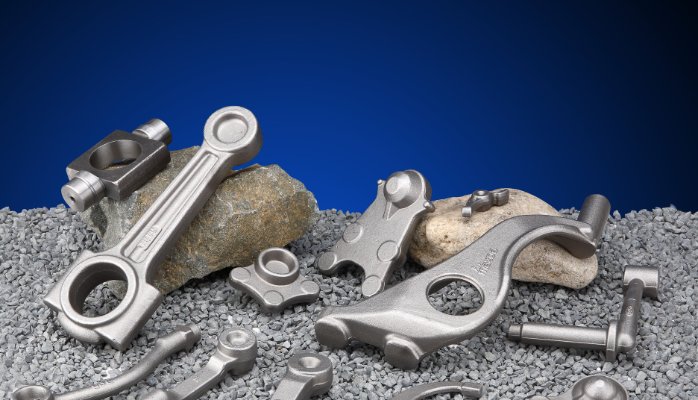
Engine components: crank shafts, connecting rods, rocker arms, cam shafts.
Transmission: gear blanks, gear shift levers, drive shaft, main shaft, propeller shaft yokes, flanges brake levers.
Steering: steering knuckle, steering shafts, steering levers, pitman arms.
Front axle: front axle beams, stub axles, front hubs.
Rear axle: rear axle shafts, differential cases and covers, crown wheels and pinions, differential gears, etc.
4.Automotive parts made by closed die forging process
This consists of hammering or pressing heated bars or billets within close impressioned dies. These impressions impart the desired shape to the work pieces. In view of the many variables in this process such as material temperature, die condition, machine load, complexity of job, die lubrication, etc. The closed die forging process consists of several steps of manufacture:
Billet heating
Reduce rolling or fullering
Bending or flattening (if necessary)
Blocker or mould
Finish forging
Billet heating (to around 1250°C) is done in forge furnaces which may be either box type pusher, walking beam, rotary hearth or induction furnaces.
Reduce-rolling is done to distribute the metal to suit forging shape in a separate rolling machine.
Flattening, bending, blocking and finish forging operations are done in the main forging unit i.e Press or a Hammer.
Trimming and hot coining operations are done on auxiliary units.
Heat treatment, shot blasting, grinding, etc are the finishing perations, which are done in separate equipments.
Automotive forgings are made by close die forging process and hence it is essential to elaborate the various features of this technology. In the first instance designs of the forged part, die and tool design are to be considered. Broadly speaking, adding material around the contours of machined piece profile constitutes the design of forged part.