Where Can I Get High Quality Drop Forgings?
What is Drop Forging?
Drop Forging is the metal working process by heating metal and hammering it in to a special die to form a final product. Manufacturers use the drop forging process to produce a series of metal products which need to be strong and durable.
Types of Drop Forging
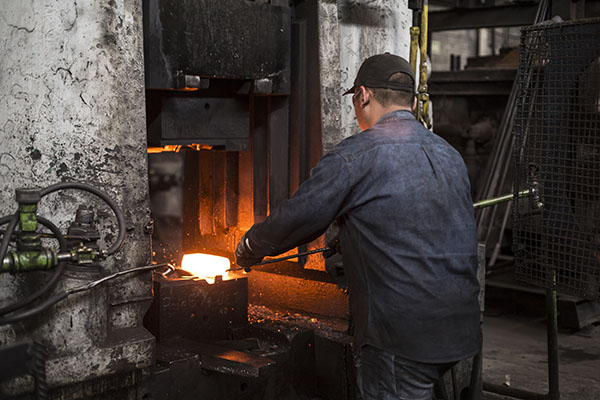
Open Die Drop Forging
Open-die drop forging is also known as smith forging. In open die drop forging, a hammer strikes and deforms the workpiece, which is placed on a stationary anvil. Open die forging gets its name from the fact that the dies (the surfaces that are in contact with the workpiece) do not enclose the workpiece, allowing it to flow except where contacted by the dies. The operator therefore needs to orient and position the workpiece to get the desired shape. The dies are usually flat in shape, but some have a specially shaped surface for specialized operations. For example, a die may have a round, concave, or convex surface or be a tool to form holes or be a cut-off tool. Open-die forgings can be worked into shapes which include discs, hubs, blocks, shafts (including step shafts or with flanges), sleeves, cylinders, flats, hexes, rounds, plate, and some custom shapes.[10] Open-die forging lends itself to short runs and is appropriate for art smithing and custom work. In some cases, open-die forging may be employed to rough-shape ingots to prepare them for subsequent operations. Open-die forging may also orient the grain to increase strength in the required direction.
Closed Die Drop Forging
Closed die drop forging is also called "impression die forging". In closed die forging, the metal is placed between upper and lower dies, which is attached to an anvil. Usually, the hammer die is shaped as well. The hammer is then dropped on the workpiece, causing the metal to flow and fill the die cavities. The hammer is generally in contact with the workpiece on the scale of milliseconds. Depending on the size and complexity of the part, the hammer may be dropped multiple times in quick succession. Excess metal is squeezed out of the die cavities, forming what is referred to as "flash". The flash cools more rapidly than the rest of the material; this cool metal is stronger than the metal in the die, so it helps prevent more flash from forming. This also forces the metal to completely fill the die cavity. After forging, the flash is removed.
In commercial impression-die forging, the workpiece is usually moved through a series of cavities in a die to get from an ingot to the final form. The first impression is used to distribute the metal into the rough shape in accordance to the needs of later cavities; this impression is called an "edging", "fullering", or "bending" impression. The following cavities are called "blocking" cavities, in which the piece is working into a shape that more closely resembles the final product. These stages usually impart the workpiece with generous bends and large fillets. The final shape is forged in a "final" or "finisher" impression cavity. If there is only a short run of parts to be done, then it may be more economical for the die to lack a final impression cavity and instead machine the final features.
Impression-die forging has been improved in recent years through increased automation which includes induction heating, mechanical feeding, positioning and manipulation, and the direct heat treatment of parts after forging. One variation of impression-die forging is called "flashless forging", or "true closed-die forging". In this type of forging, the die cavities are completely closed, which keeps the workpiece from forming flash. The major advantage to this process is that less metal is lost to flash. Flash can account for 20 to 45% of the starting material. The disadvantages of this process include additional cost due to a more complex die design and the need for better lubrication and workpiece placement.
Where Can I Get High-Quality Drop Forgings?
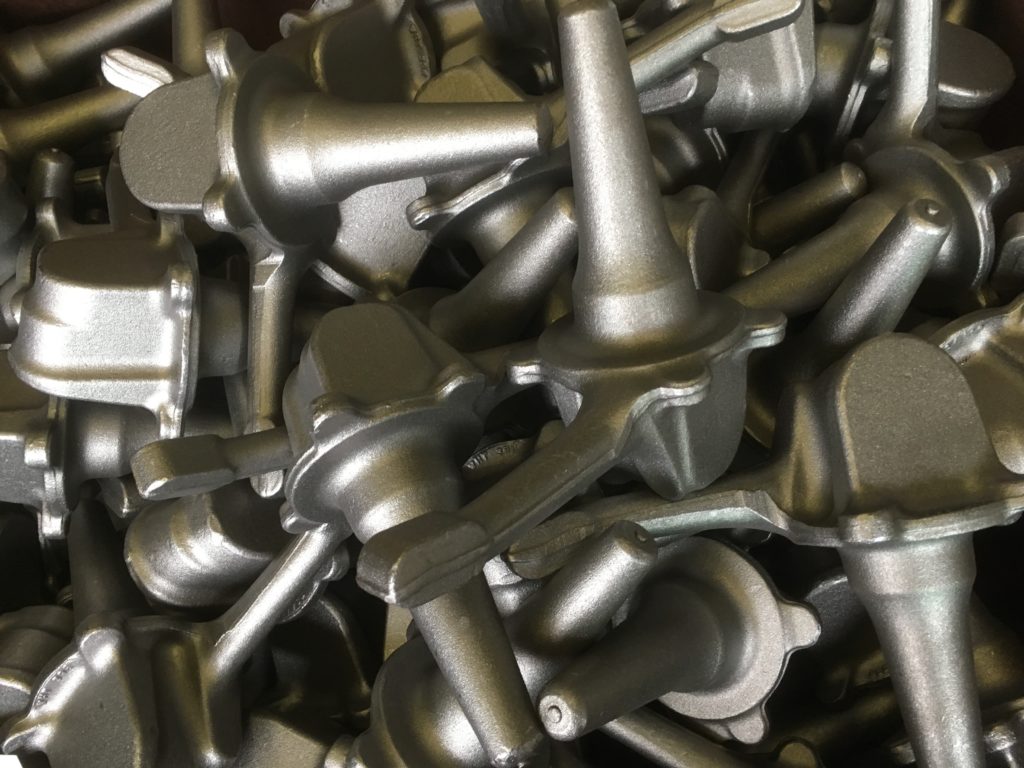
Drop forging is a superior to casting or machining bar stock since the metal’s natural grain flow is made to conform to the shape of the product. Castings have an isotropic grain structure and, for a given part, may be as strong in compression loads, but forgings are superior in tensile and shear loads due to the utilization of the grain flow.
Fly Forge typically uses specialty bar stock as our incoming raw material. As these metal bars are heated and forged, the grain structure within the material is forced to flow along the centerline of the bar. When a forging is produced from the bar, this inherent grain flow follows the contour of the forged shape. Any machined part, whether produced from bars or plate, will by definition cut through part of the grain flow. Castings essentially have no grain direction. This is one of the primary reasons forging produces a superior part.
The structural reliability of drop forgings allows designers to trust the material to adhere to the safety factors of the design. It also can provide more uniform response to heat treatment and machining operations.
Drop forging is the most wear-resistant and heat-resistant option available, no matter it is steel forging or aluminum forging.
In many cases, drop forgings also offer a cost-savings over other methods of manufacture. Drop forgings can be made near-net or net in shape, therefore reducing machine time and/or scrap.
Turn to Fly Forge for all your sourcing of closed die drop forgings! Here you will get high quality drop forgings with the most competitive prices in the shortest lead time.