
Drop forging manufacturer

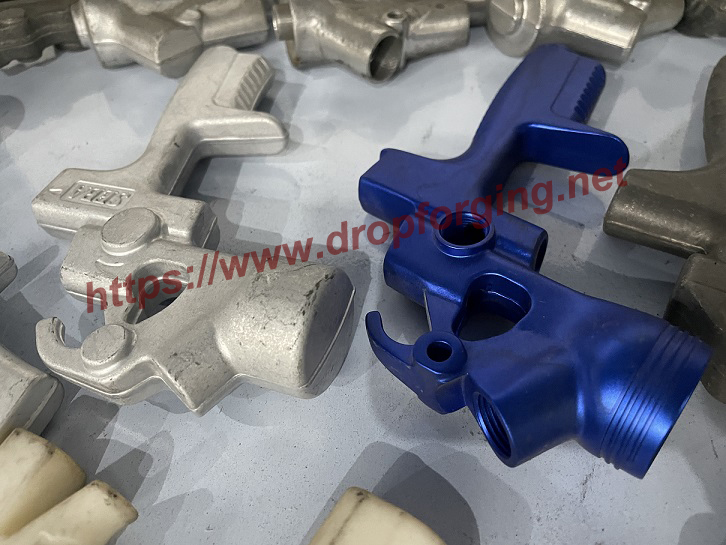
A forged aluminum spray gun body is the central part of a spray gun, which has been formed using a forging process involving aluminum. Essentially, it's the framework that houses various components of the spray gun, including the trigger, nozzle, and paint container.
The term 'forged' signifies the manufacturing process utilized to create the spray gun body. Aluminum forging is a process in which a piece of aluminum is heated and then shaped using a hammer or a press, under high pressure, to achieve a specific design, in this case, the structure of a spray gun body.
The forging process refines the grain structure of the aluminum and aligns it to the shape of the part, thus enhancing its overall strength and durability. Aluminum, and in particular 6061 aluminum alloy, is a popular choice for forging spray gun bodies due to its excellent mechanical properties, good corrosion resistance, and lightweight nature.
The forged aluminum spray gun body thus produced is not only light and easy to handle but also durable and resistant to wear and tear, making it suitable for heavy-duty applications and ensuring a longer lifespan of the spray gun. Furthermore, it maintains its dimensions and shape even under extreme conditions, ensuring the consistent performance of the spray gun.
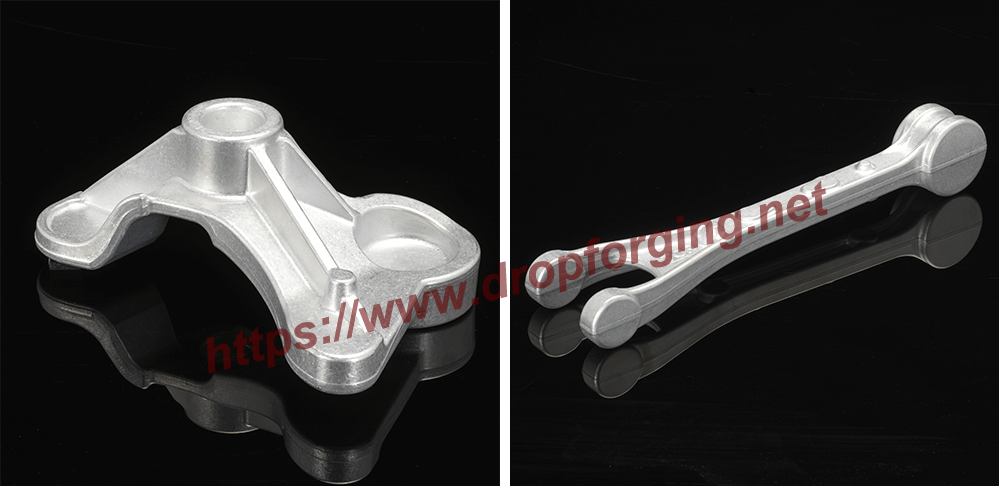
Automotive suspension parts are essential components of a vehicle, responsible for providing a smooth and comfortable ride, as well as ensuring the safety and stability of the vehicle on the road. In recent years, the use of forged aluminum suspension parts has gained popularity in the automotive industry due to their many benefits over traditional materials like steel.
One of the primary benefits of using forged aluminum suspension parts is their strength-to-weight ratio. Forged aluminum parts are typically lighter than their steel counterparts, but they can be just as strong or even stronger. This means that vehicles equipped with forged aluminum suspension parts can be lighter overall, which can improve performance and fuel efficiency.
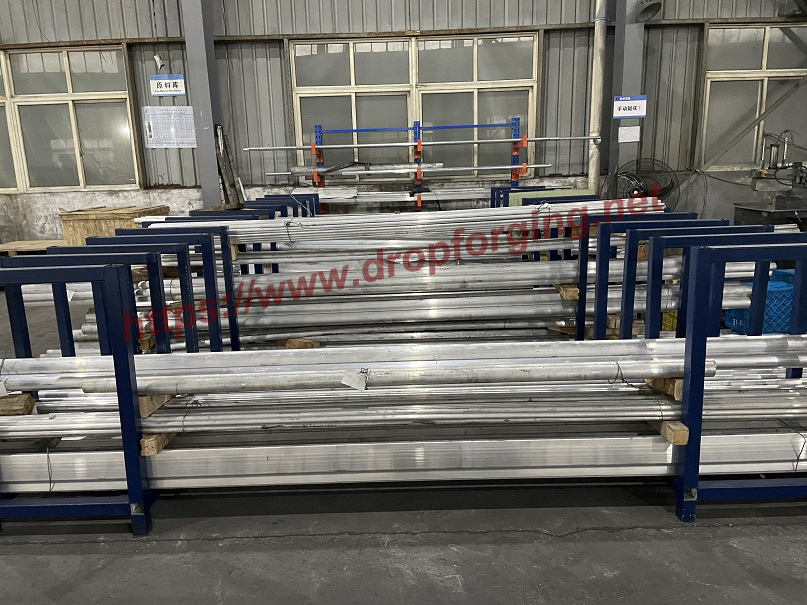
Aluminum forging is a widely used technique in the manufacturing industry. It involves shaping the metal by heating it to a high temperature and then applying pressure to deform it. Aluminum forging alloys are specifically designed to withstand the extreme temperatures and pressures involved in the forging process. In this article, we will discuss the most common aluminum forging alloys and compare their differences between these alloys.
Aluminum forging alloys are an important part of many manufacturing processes. These aluminum forging alloys discussed above are some of the most commonly used in the industry, each with its own unique set of properties and characteristics. By understanding the differences between these alloys, our customers can choose the best alloy for their specific application, ensuring optimal performance and efficiency.
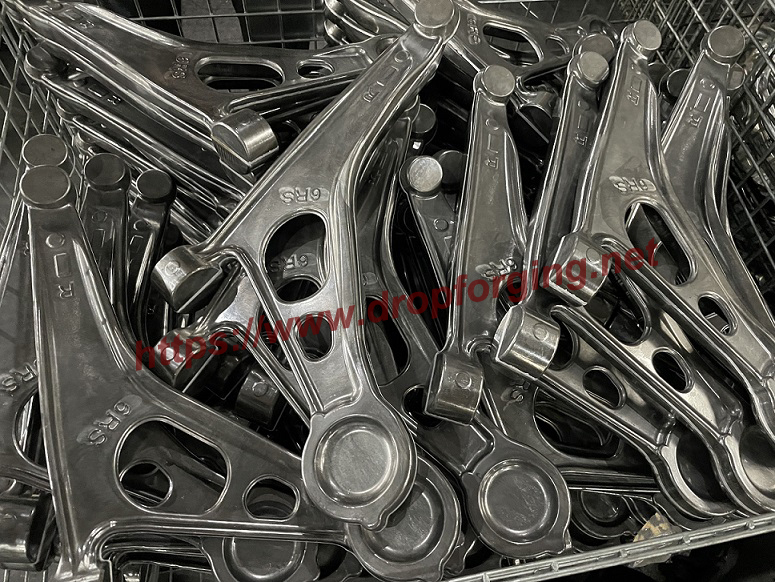
Control arms are essential components of a vehicle's suspension system, which connect the suspension to the frame of the car. They help maintain the wheel's position relative to the car's body, absorb shocks and bumps, and help control the steering and handling of the vehicle. Forged aluminum control arms are a popular choice for many car enthusiasts due to their strength, durability, and lightweight properties.
Aluminum forging is a manufacturing process that involves shaping a metal by heating it to a high temperature and then pressing it into the desired shape using a die. Forged aluminum control arms are made using this process and are known for their strength, durability, and lightweight properties.
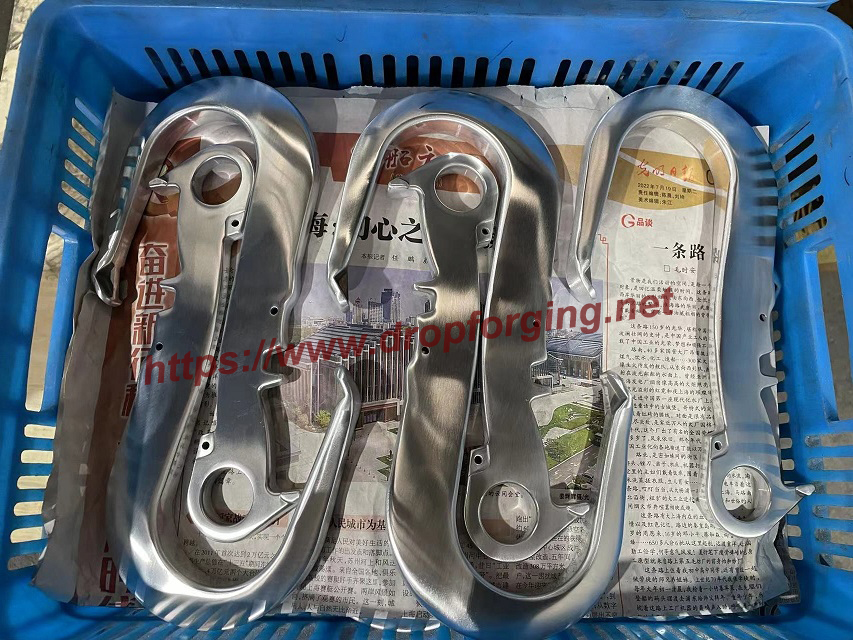
Carabiners are one of the most important safety equipment used in mountaineering, rock climbing, and other outdoor activities. These small, yet robust metal hooks, are often used to secure ropes, harnesses, and other gear, and are crucial in ensuring the safety of climbers and hikers. Aluminum forging is a popular manufacturing process used to produce carabiners due to its many advantages. In this article, we will explore the process of aluminum forging and its benefits for carabiner production.
Forging is a manufacturing process that involves shaping metal by applying pressure to it. Aluminum forging, specifically, is the process of shaping aluminum into various forms, such as carabiners, using compressive forces. In this process, a piece of aluminum is placed between two dies and subjected to high-pressure forces until it takes the shape of the die. The die is a tool that is specially designed to form the metal into a particular shape. The process is often done at high temperatures to make the metal more malleable and easier to shape.
The process of aluminum forging involves several steps, including heating the aluminum to a high temperature, placing it in a die, and applying high pressure to shape it. The heating process ensures that the aluminum is malleable enough to be shaped, while the die ensures that the shape of the ATV wheel spacer is accurate and consistent. The high pressure applied during forging creates a strong, durable product that is resistant to wear and tear.
Aluminum forging requires a specific type of aluminum alloy, which has a high strength-to-weight ratio. This type of aluminum is ideal for ATV wheel spacers, as it can withstand the harsh conditions of off-road driving. The most commonly used alloy for ATV wheel spacers is 6061-T6 aluminum, which is strong, lightweight, and corrosion-resistant. This alloy is also easy to work with, making it a popular choice for aluminum forging.
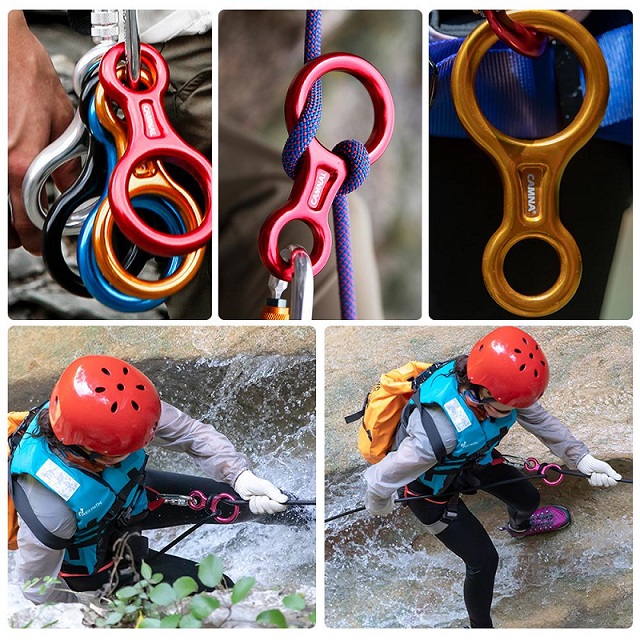
The forged aluminum figure 8 descender is an important item for any climber’s kit due to its unparalleled reliability and strength. Professional climbers have trusted the figure 8 descender for generations, as it allows them to control the descent with utmost confidence safely. Whether you are just beginning your climbing journey or experienced in scaling heights, understanding the features of the figure 8 descender is essential to make an educated selection when it comes to choosing your gear. With its wide range of safety features and customizable capabilities, adventurers can rest assured they have high-quality equipment perfect for their climbing needs.
Aluminum forging has been a key element of metal manufacturing for centuries, making it possible to create higher-strength mechanical parts and improved internal material structure. Due to its superior performance, aluminum and aluminum alloys have quickly become the preferred choice for aluminum forging in machinery, electricity, electronics, automobile production, shipping, construction, instrumentation and hardware. Today aluminum forgings are used heavily in the aviation industry, accounting for over 77% of all airframe materials, 68% of tank builds and a substantial 76% of vehicle components. Obviously, aluminum forging is the correct way to make forged aluminum figure 8 descender.
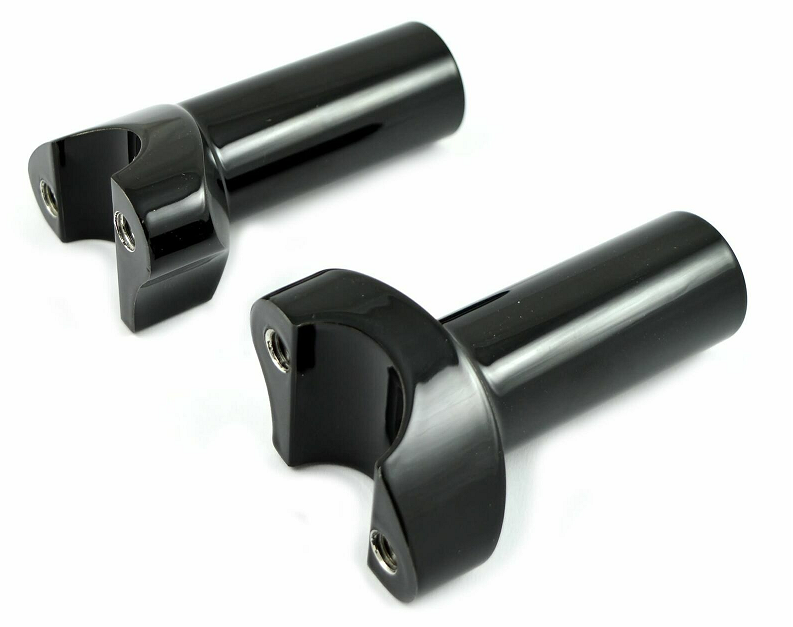
Aluminum is a lightweight and versatile metal famous for various applications in the manufacturing industry. One of its many uses is in making handlebar risers for motorcycles. These components are crucial for the vehicle’s ergonomics, improving comfort and handling.
In recent years, forged aluminum is a preferred material for motorcycle handlebar risers. While aluminum has many advantageous properties, applying heat and pressure while forging aluminum parts also provides it with great durability and strength. Here, we will discuss more on aluminum forging process of motorcycle handlebar riser.
Aluminum snap hooks are essential in various industries due to their reliability, durability, and versatility. These hooks are popular with outdoor enthusiasts, construction workers, and manufacturers. Hence, let us talk about aluminum forging of snap hooks.
Forging aluminum snap hooks involves heating the metal to a high temperature. And then shaping it using specialized hammers and anvils. So this results in more uniform and denser snap hooks created than other manufacturing methods.
In addition, forging allows for a high degree of customization. This allows the ability to create snap hooks in various shapes and sizes to suit different applications. As a result, forged aluminum snap hooks can be a reliable solution for rigging, climbing, and arborist applications.
Aluminum forging is perfect for applications where performance and safety are critical but a lighter-weight metal is needed for speed or energy efficiency. When performance and strength are important factors for motorcycle footpegs, aluminum forging is the way to go.
To withstand the harsh conditions of a challenging environment, structures must be strong, durable, and lightweight. Forged aluminum has a lower density than forged steel, which makes it an ideal solution for motorcycle footpegs.
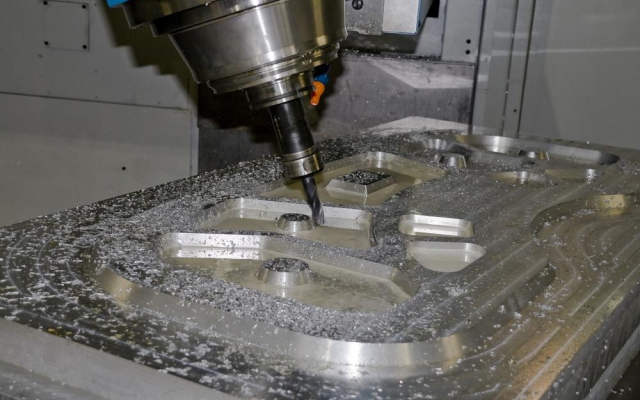
For the closed-die forging of aluminum components, die or mold is critical element in the overall aluminum forging process, because the dies are a major element of the final cost of such forgings. Further, forging process parameters are affected by die design, and the dimensional integrity of the finished forging is in large part controlled by the die cavity. Therefore, the forging of aluminum alloys requires the use of dies specifically designed for aluminum because:
- The deformation behavior of aluminum alloys differs from that of other materials; therefore, the intermediate and final cavity die designs must optimize metal flow under given forging process conditions and provide for the fabrication of defect-free final parts.
- Allowances for shrinkage in aluminum alloys are typically greater than those for steels and other materials.
- Temperature control of the dies used to forge aluminum alloys is critical; therefore, the methods used for die preheating and maintaining die temperatures during forging must be considered in the design.
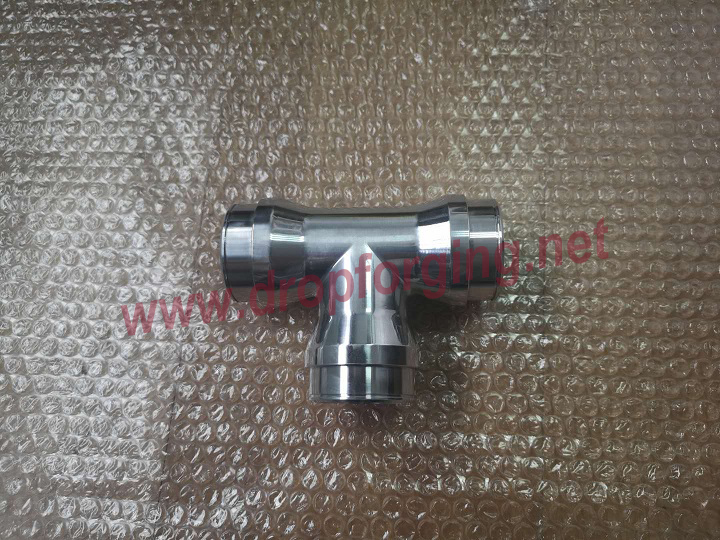
Pipe fittings are the fittings used in the piping systems to connect the straight pipe or tubing sections, adapt to different sizes or shapes and for other purposes, such as regulating (or measuring) fluid flow. Pipe fittings can be designed and made in different kinds of metal materials, including steel, aluminum and brass. Compared with steel and brass pipe fittings, aluminum pipe fittings can offer light weight but good corrosion resistance.
Aluminum forging for pipe fittings are the hot forging process that pressing aluminum billets into shapes of various pipe fittings. There are several steps involved in forging aluminum pipe fittings, including billet cutting, billet heating, forging, trimming and shot blasting. To achieve qualified production, each step of manufacturing pipe fittings during the aluminum forging process must be strictly controlled. As the professional aluminum forging company in China, CFS Forge is able to supply custom aluminum forging and machining service of various pipe fittings for our customers. If you have any inquiry on aluminum forged pipe fittings, pls contact us.